Rethinking steam and combustion at Parenco
Since 2012, when the ownership of Parenco transferred to H2 Equity Partners, the company has been investing regularly in its paper production. One of the latest investments has been to enhance the steam distribution in the power plant with Valmet’s solutions.
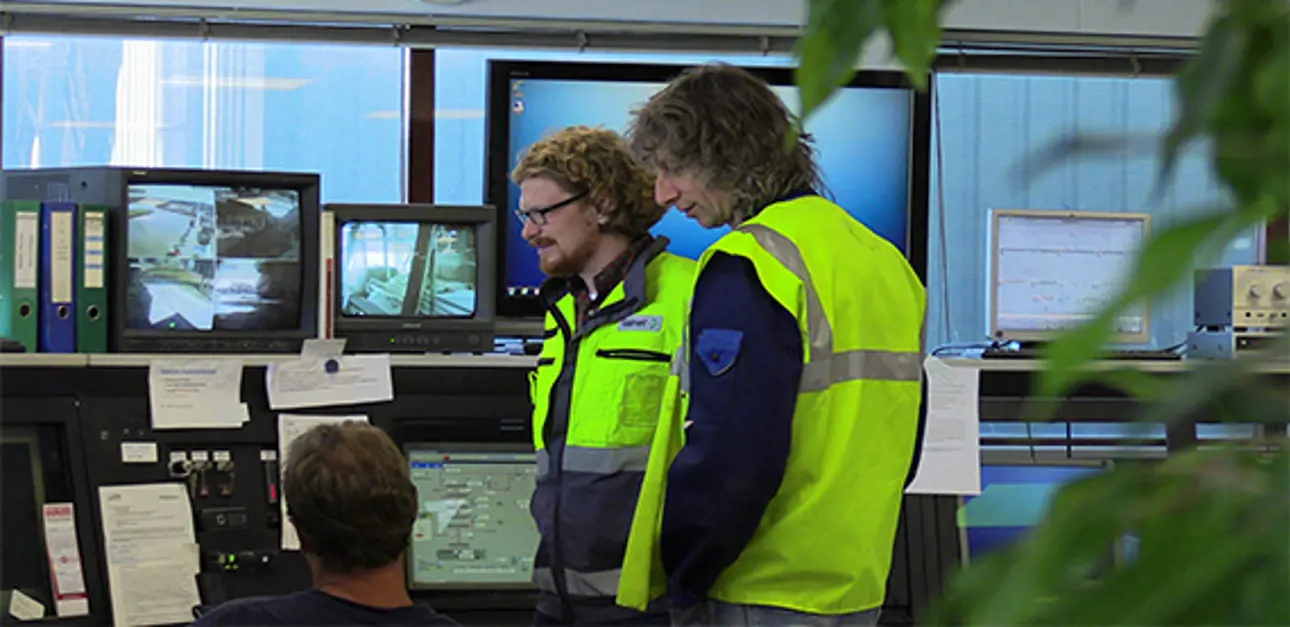
Based in Renkum, Netherlands, Parenco has a yearly turnover of approximately EUR 140 million. The company’s PM1 has a capacity of 270,000 tons per year and is used for the production of so-called SC-B paper for magazines and brochures. In 2016, PM2 has been transformed from a newsprint machine to a packaging production line with a production capacity of about 385,000 tons of packaging paper.
Stabilized steam network targeted
Hans Hietbrink, Assistant Line Manager, Pulp & Energy, Parenco, is primarily responsible for the steam production at the site. At Renkum, Valmet BFB Boiler (formerly HYBEX) using bubbling fluidized bed (BFB) technology, called K62, is the main steam producing boiler with a production capacity of 50 megawatt (MW). The boiler produces steam at 48 t/h, has a pressure of 60 bar and uses biomass as fuel.
In 2015, major investments were made to enhance the steam production at the site. Hans Hietbrink describes the challenges Parenco wanted to solve: “The main target was to stabilize the steam network and pressure as well as to minimize the steam upload by using the steam accumulator more proactively.”
The project started in December 2015 with Valmet coming to the site to improve the steam production efficiency. First, the steam distribution to PM1 was completed in August 2015. Then, the project will be extended to cover also the renewed PM2 later in 2016.
Valmet’s solutions to enhance the steam production
To tackle the challenges, Valmet’s solution consisted of a Valmet DNA Steam Network Manager, an advanced process control (APC) application that stabilizes the steam network. The solution is based on multivariable model predictive control and is able to control several steam network variables simultaneously.
At the same time, a Valmet DNA FBB Combustion Manager, an APC application for optimized combustion, was also delivered. The application is based on fuzzy logic control and can regulate several combustion variables to improve the boiler combustion.
Caption: Hans Hietbrink from Parenco and Stephan Wenzel from Valmet.
Before the installation, a thorough investigation was conducted to find the best way to create the link between the existing automation and Valmet’s advanced controls. As a result, the connection was built through an OPC link to secure the data transfer.
Biomass boiler, the heart of the site
Parenco prefers to use biomass as a sustainable fuel and aims to use the biomass boiler over the gas boiler. A high output of the biomass boiler was something that Parenco was especially looking for. Thanks to Valmet’s solution, this was also achieved. The boiler load setpoints contribute to the steam consumption so that the biomass boiler now supplies the required load accurately. In this way, the steam accumulator compensates for the short-term steam balance. The steam turbine is out of operation and the gas boiler is used less and less. The unnecessary gas boiler usage has been reduced by over 70%.
“Valmet’s DNA Steam Network Manager takes care of the paper mill’s steam distribution. As a result, also the quality of the steam has been improved considerably. Additionally, fewer paper breaks are occurring since there is a relationship between the steam pressure, temperature and the number of breaks. Therefore, the steam network stability is very important for the paper production,” Hietbrink explains.
A steam load setpoint in the biomass boiler and a fuel feed setpoint in the gas boiler, for example, have been designated as variables that the mill can manipulate. In contrast, the HP steam pressure, MP2 steam pressure and steam accumulator pressure are used as controlled variables. When comparing the baseline with the results of today, it is visible that the whole steam production process has been optimized.
Combustion manager to stabilize the process
Valmet’s combustion manager application is used to protect the combustion process against variations in the production, fuel amount and combustion circumstances. “The boiler efficiency has been clearly increased with help of the DNA FBB Combustion Manager. Moreover, NOx and CO2 emissions have been minimized,” states Hietbrink.
Parenco has to follow the emission limits carefully, and the figures have to be reported to the authorities. “There are hundreds of parameters, like the furnace temperature, oxygen level and many more, that we consistently have to follow. Manually, this would be impossible to do. The application is looking constantly at those parameters and follows the situation. For instance, we have been able to minimize flue gas flow rate because it is one of those critical parameters,” Hietbrink says.
Training for operators at hand
Valmet’s Industrial Internet includes the APC solutions. By gathering and analyzing data, the mill’s efficiency and profitability can be improved. The main target of the APCs is to keep the best operating conditions in use, and for this, the operators are in a key position.
Fro
Parenco’s operators work in five shifts with three operators in each shift. Valmet was very well prepared to give a hands-on training to every operator at the site. “To get the full benefits of the APCs, you have to use them all the time and you need your operators to be motivated to use them. Our operators know how the system works – after all, they use it 24/7,” Hans Hietbrink confirms.
Jeroe
Reaching the targets by cooperating with Valmet
Parenco can now enjoy the fruits of its harvest, which are the benefits of the APCs. The desired ratio between the use of the biomass boiler and gas boiler, the minimized steam blow-out as well as many other advantages achieved with Valmet’s solutions are all helping the paper mill produce high-quality products with lower costs while being more environmentally sound.
The first part of the project was realized in about six months. Since the results so far have been on target, payback time for the investment is less than one year.
Caption: Jeroen Liebrand, Stephan Wenzel and Hans Hietbrink in the control room.
Hans Hietbrink is satisfied with the cooperation. “I can assure you that we have reached the main targets set for the project. Valmet’s experts have always been available and are happy to share their expertise with us. I look forward to the following project with Valmet.”
More information:
Stephan Wenzel
stephan.wenzel at valmet.com