From local fiber resources to sustainable paper products
In many parts of the world, we see innovative efforts in the search to produce paper more sustainably. The development is coming on strong as tissue producers are exploring if regional and local fiber resources might be an opportunity for them.
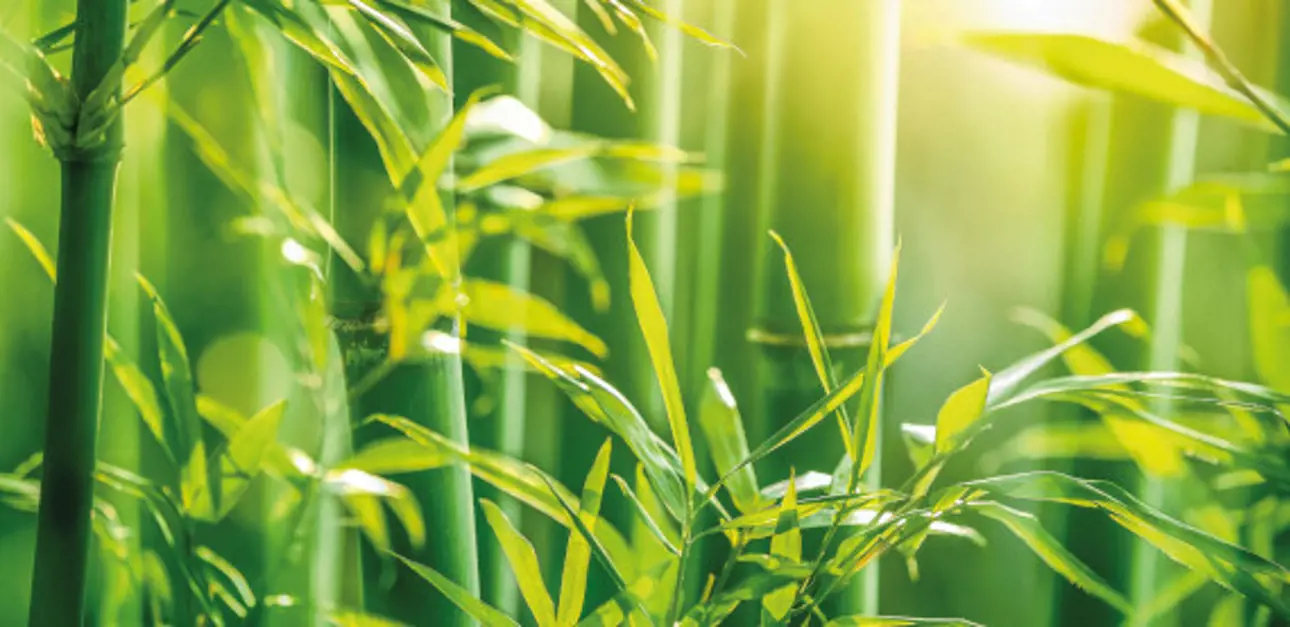
Wood fiber has been the main source of paper production since the mid-1800s. Although it is considered a sustainable material, it can’t be grown everywhere: In most cases, transportation is a necessary part of the supply chain. It is also known that transportation brings energy use and CO2 emissions. Separately, burning residue from various crops makes a major contribution to air pollution.
Burning residue from various crops such as wheat straw makes a major contribution to air pollution.
By utilizing resources close to home and turning them into sustainable paper products, local business owners are empowered, job opportunities are created, and entire communities can benefit positively from such investments.
In this article, we will introduce you to various materials that can be used to make tissue, such as straw, bagasse, bamboo and microfibrillated cellulose (MFC). We have spoken to some leading experts, all with their own area of expertise.
Adding wheat straw fiber to the product mix
More than 20 years ago, wheat straw burning in the state of Washington contributed to more air pollution than the top 20 industrial manufacturers in the state. So they started to look at an alternative commercial use for the wheat instead of burning it. A question was raised: Could a new technique make it possible to explore the potential of creating pulp from straw?
By utilizing an agricultural residual product, both energy and water savings can be achieved.
Today, Columbia Pulp, located in the eastern part of Washington state, is a manufacturer of wheat straw. We spoke to the CEO, John Begley, who says the company is strategically located in the center of one of the world’s largest wheat-growing areas.
John Begley, CEO of Columbia Pulp.
As a substitute for hard wood fiber, Columbia Pulp has added their fiber to various end-use products. And the findings have been successful. By utilizing an agricultural residual product, both energy and water savings can be achieved. Only a quarter of the water is used compared to that required by a normal pulping process. There is little or no odor, as it is a sulfur-free process. The product is unbleached and completely chlorine-free. Begley is proud of the state-of-the-art process operated by Columbia Pulp.
Pulp made from bagasse
The residue that remains after sugarcane stalks are crushed and the sugar is extracted are called bagasse. As alternative use is limited, it contributes to the problem of agricultural waste in India and air pollution when burned. However, bagasse can be transformed into an environmentally friendly product.
Sugarcane bagasse is a clean fiber with low lignin, and is easy to wash and easy to bleach.
Naini Group and its Managing Director Pawan Agarwal may be pioneers when it comes to producing pulp from bagasse. The company had already started in 1998, so this relatively unknown source of fiber is anything but new to them. According to Agarwal, bagasse has some wonderful characteristics. It is a clean fiber with low lignin, and is easy to wash and easy to bleach. If the production process is done properly, you can get good fiber from bagasse. Where paper properties are concerned, it is very comparable with paper made from wood pulp.
Pawan Agarwal, Managing Director of Naini Group.
Three of the biggest advantages that Agarwal sees with bagasse are its bleachability, uniformity and the strength of the paper. If he must pick one drawback, it would be the lower bulk.
Microfibrillated cellulose – the green solution for today and beyond
What is it, and how can it be used? If there is one person who can answer those questions, it’s David Cowles, Global Market Development Manager, Nanotechnologies at Valmet. He is currently working with a team of Valmet experts and researchers in collaboration with the University of Maine. Microfibrillated cellulose, also called MFC, is a cellulose material that falls under the fibril range. At Valmet, we measure it as a percentage of total fines. And a fine in this case is a fiber that is less than 0.2 mm long.
Microfibrillated cellulose, also called MFC, is a cellulose material that falls under the fibril range.
The benefits of MFC are many. It is a sustainable tree-derived resource. Cowles gives us an example. Let’s imagine a tree made of eucalyptus. It may take between six and eight years before it is fully grown and ready for harvesting. That tree root can then be used a total of two or three times in a possible 20 years or so. MFC also offers production flexibility, because it uses mechanical or chemical processes, or a combination of the two. Cowles summarizes MFC as a toolbox of opportunities for papermakers that are only limited by the imagination.
David Cowles, Global Market Development Manager, Nanotechnologies at Valmet.
Naturally, at Valmet, we speak about MFC in relation to paper products. But its use is being explored in personal care, biomedical products, anti-fog coatings, hand sanitizers and material reinforcements.
The benefits of using bamboo in tissue making
The characteristics of bamboo fibers are similar to soft- and hardwood fibers and because of this, it can be suitable for producing tissue. –Ulf Johnson, Concept Manager, Mill Technology at Valmet, explains that in Asia, bamboo is frequently used to produce facial and bath tissue. Concerning its environmental aspects, it is fast growing and ready for harvest in one to two years. Locally or regionally grown bamboo often means less transportation. And it emits more oxygen than a comparable tree. Exploring the possibilities of producing tissue from non-wood is like going back in history. Johnson means we are now revisiting lost expertise, and he is hopeful for the future. Together, we have many opportunities to produce paper more sustainably than ever.
Ulf Johnson, Concept Manager, Mill Technology at Valmet.
Text Anna Boström Mora
Interested in learning more?
In-depth recorded 20-minute presentations
are available on request.