Celebrating 65 years of flow control
Celebrating 65 years of flow control
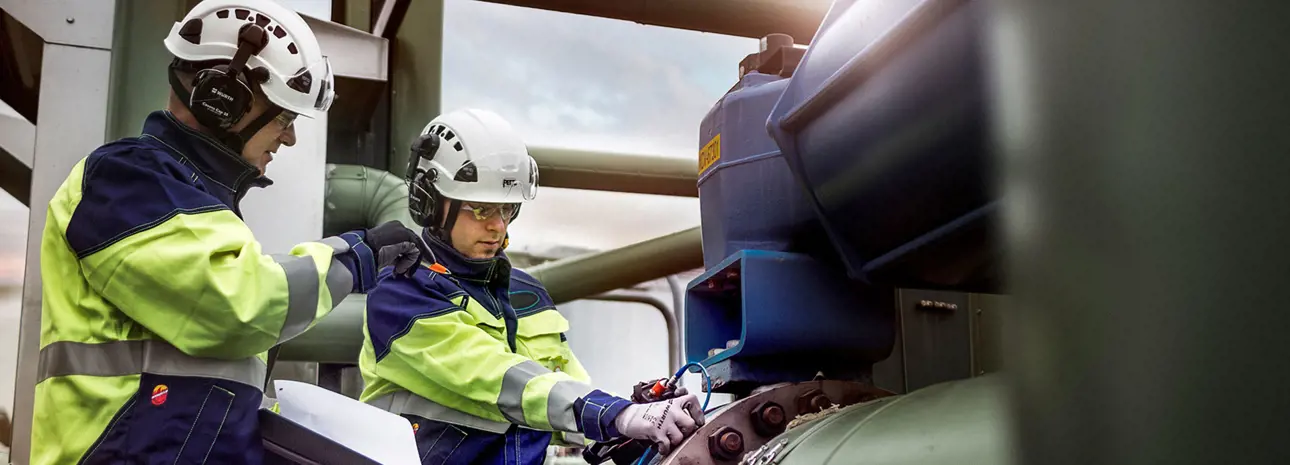
CHAPTER ONE History of Neles
Valve World Americas had the opportunity to speak with Fred Porth, North American Business Manager, Todd Harrison, Regional Sales Manager for the Southwest Region of North America, and Kyle Rayhill, Vice President of MRO and Distribution to learn more about Neles progressive history, its current innovations in the industry, and how it intends to achieve a green future.
Founded in 1956, Neles was initially established, alongside Jamesbury, as two prominent valve manufacturers. The president of Jamesbury at the time, Howard Freeman, had a famous patent for a polymer seated ball valve, which led the company to become a large industrial valve name in North America.
The Neles brand achieved global recognition with pioneering metals seated valve technology and made a significant mark to start with in the pulp and paper industry. The two companies would later merge in 1988. “Right from the beginning, this company was dedicated to providing solutions that went beyond the customer’s needs,” expressed Rayhill. With the two brands, the company was able to flourish both as an international manufacturer and a supplier of a wide range of products.
Since its inception, the company has experienced many milestones, including the introduction of metal seated valves in 1970, the Neldisc butterfly valve in 1975, and the creation of valves that were used in NASA’s space shuttle pads in 1981. In the following decade Neles was acquired by the predecessor of Metso, which led to an increase in its valve offerings, and expansion of its operations. After establishing the Metso Corporation in 1999, and introducing digital valve technology, more expansion occurred within the company.
In 2020, Neles became an independent company following a partial demerger of Metso Corporation. “It has been quite the development up until now, taking the company to the next level was a large accomplishment for Neles,” stated Porth.
CHAPTER TWO Current valve offerings
Having been recognized in the industry for its rotary control valves for several decades, Neles holds a strong position in several industries. The company has evolved from focusing primarily on valves, to offering actuators and intelligent valve control solutions. “In addition to valves, Neles manufactures automation and field instrumentation products, which includes actuators and controller products which are used to fulfill end user requirements for control, emergency shutdown and on/off valve applications,” said Rayhill.
One of most prevalent products in Neles current portfolio is its butterfly valve. The inception of the NelesTM butterfly valve platform has two distinct roots: Neles NeldiscTM and Jamesbury Wafer-SphereTM products. The Neldisc butterfly was created in 1973, with the aim of developing a valve that could withstand temperatures up to 600°C (1100°F) and still maintain excellent tightness characteristics with long-lasting durability. This product has evolved into a unique triple offset valve design, which is used around the world. While Neles was focused on perfecting the metal seated, Jamesbury was dedicated to developing a zero-leak, bi-directional soft seated butterfly valve; the Wafer-Sphere.
Today, the Neles Neldisc and JamesburyTM Wafer-Sphere have come together to form a modular butterfly valve platform that has the ability to meet all of today’s industrial butterfly valve needs.
The dedication to continuous development and new product upgrades and added features which has resulted in the Neles butterfly valve, ensure that these valves are poised to exceed expectations in most industrial applications, regardless of end product, flow media, temperature or pressure. The comprehensive approach ensures a simple and easy selection and configuration process that enables efficient valve operations at a competitive lifecycle cost.
CHAPTER THREE Safety and sustainability
Following safety practices across a customer’s facility is a priority. In addition to minimizing fugitive emissions, one of key way of improving safety in the process is to manage noise in control valve application. Noise generated through valves can lead to ambient noise, premature valve failure, and safety risks. Noise is commonly caused by acoustic shockwaves or cavitation. Using noise abatement strategies, such as path and source treatment, solutions can be found to prevent or greatly minimize this issue. Neles developed its first noise cavitation trims in 1980. “We were the first to patent a cavitation solution in a quarter turn valve, and today, we still continue to develop this technology,” said Porth.
Fuel safety shutoff valves are designed for the safe shutdown of boiler and combustion systems. They are a critical part of most process facilities and must be specified correctly for reliable operation. They must meet legal requirements for plant safety in many cases. After installation, there can also be rigid service requirements. With all of this considered, Neles participates in standards organizations and committees within the valve industry. This helps us to understand and incorporate these challenges into our designs and service models. “At the end customer level, we support a large installed base of these specialized assemblies because of the quality of the product, and the ability to meet and manage the specification requirements,” said Harrison.
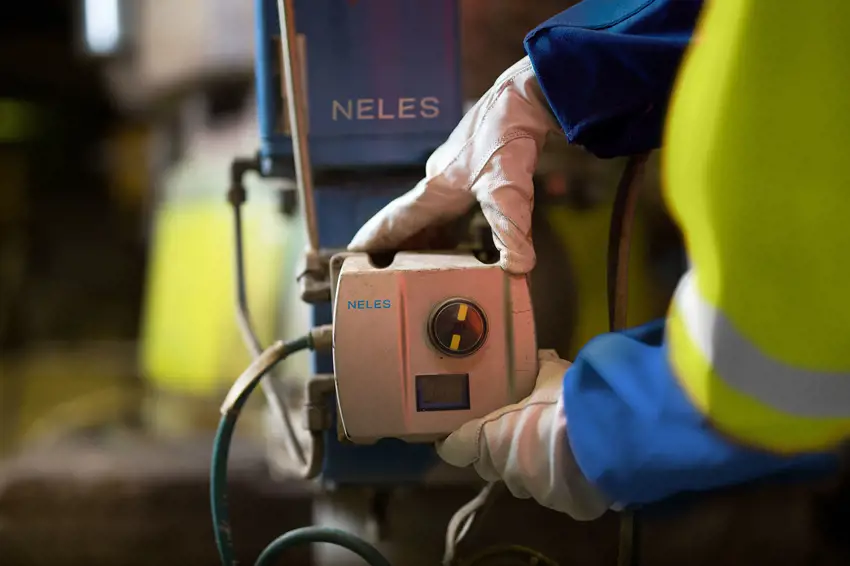
Sustainable solutions for the future are of great interest in the industry as legislation and concern for the environment is on the increase. “We have a very strong sustainability agenda, with a focus on health and safety, environment and society and the economy,” said Rayhill. Green hydrogen, as an up and coming industry, fits their sustainability practices already in place.
Neles has been in the hydrogen business for many years and works with the major industrial gas companies. “We understand the challenges of these applications. With a global Power to X focus for energy, there will be new technologies and requirements to consider. Neles will continue to work closely with end users and licensors to develop reliable and sustainable solutions for this new and exciting industry.”
CHAPTER FOUR Customer first approach
Beyond its innovative product lines Neles provides services that elevate it above its competitors. Throughout the Covid pandemic, companies across all industries faced fears of not being able to connect with their associates and customers. By staying active and keeping up with trainings and offering webinars, Neles remained close to its customers during this time. In 2020, the company held more than 75 webinars and virtual seminars for customers globally and 85 online trainings for channel partners in North America only. “The driving mentality behind our way of working has always been to stay close to customers, and put them first,” said Rayhill. “Although it is not the same as face-to-face interactions, virtual meetings and webinars provided a means for us to ensure that we never lose contact with our clients. It does not substitute for face-to-face meetings, but it definitely compliments it.”
Using a multi-tiered channel philosophy, Neles combines direct service and support, along with channel partners (distributors), to provide comprehensive coverage of their served market. “Overall, our goal is to make sure all new and existing customers have access to local representatives of our products so that we can bring high service levels to them,” explained Rayhill. “Neles puts the customer’s requirements in the forefront of all of our product development initiatives and engineered solutions,” stated Porth. “Neles becomes a valued partner rather than just a valve supplier to customers. So, in our eyes, customer success is our success.”
CHAPTER FIVE Comprehensive service
With years of experience, Neles has established unique solutions for a variety of industries. “With our extensive flow control offering, and a global team of almost 3,000 experts, spanning across 40 different countries, we can partake in a lot of different process industries; some of our larger ones include pulp paper, bio-products, and energy and hydrocarbon, which would include refining and petrochemical,” said Porth.
Maintaining a diverse customer base is a result of a strong direct sales team and channel partnerships, extensive experience, and years of credibility. “We have not only been a part of some of the older and substantial markets in North America, but we have also been able to adapt and design, and provide products into some of the newer industries,” said Harrison.
“Our goal at Neles is to always put the customer first. We work closely with customers to provide them with the best support and technology for their process needs. This begins with our engineers working closely with customers to define the needs and product expectations and continues through the various sales phases. This partnership continues for the entire equipment lifecycle process, with our service experts working with plant personnel for best practices with repairs, upgrades, shutdowns, etc.,” relayed Rayhill. “We are truly a full-service company.”
A global team of almost
3,000 experts
around the world
CHAPTER SIX Where Neles is now
Continuing with sustainable practices, Neles is now looking into a green-future with emission-free hydrogen production. To achieve this initiative, the company has valve solutions for hydrogen applications ranging from green electrolysis to blue carbon capture. The role of these as carbon-neutral fuel produced from renewable energy is growing and will continue to grow.
The future of emission-free production for valves will require reliable performance and finding new ways to produce and process materials. Neles is experiencing a shift from traditional hydrogens to emissions-free green fuels, using their decades of experience with industrial gas and hydrogen applications. “We welcome new types of processes for green hydrogen and look forward to developing new technologies and applications to compliment this progressive movement,” concluded Rayhill.
This article was originally published in Valve World Americas Journal, August 2021 issue.
Read more