Palm Aalen PM 5 – a sustainable investment for the next 50 years
PM 5 at the Papierfabrik Palm Aalen-Neukochen site in Germany is the world’s widest high-capacity containerboard line. It is an investment for the next 50 years and has been producing high-quality and sellable board since the start-up in July, 2021.
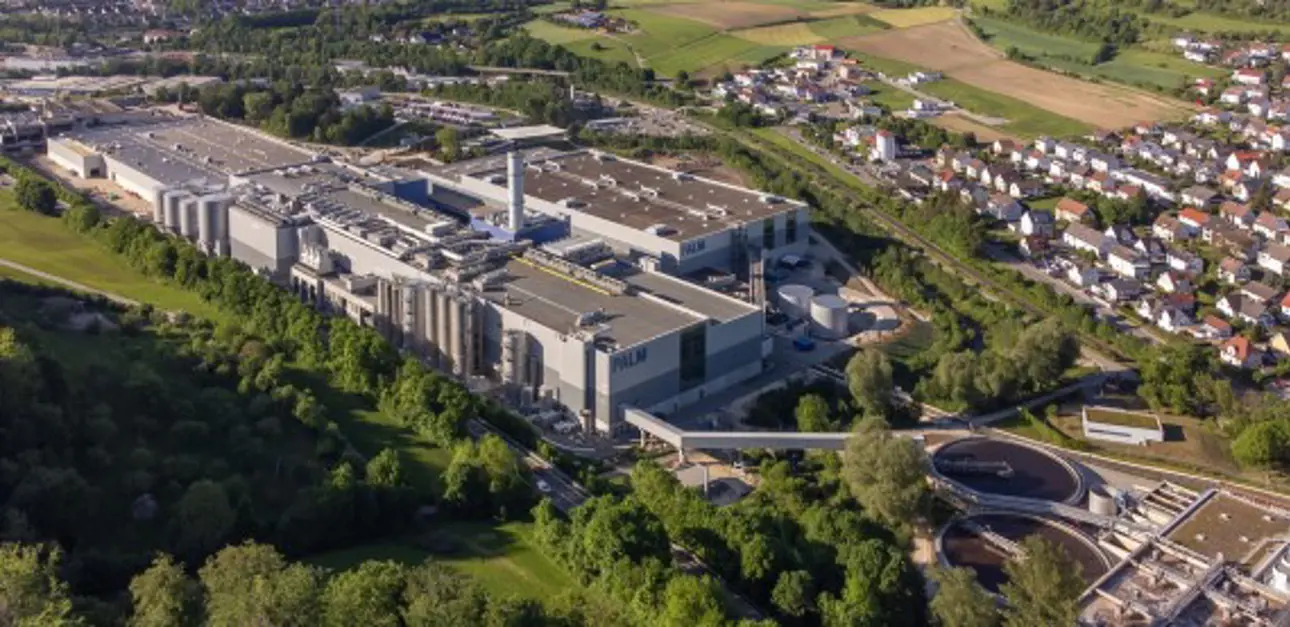
I strongly believe that PM 5 has a lifetime that is much longer than 50 years.
Palm Aalen’s PM 5, which was delivered by Valmet, is 10.9 m wide, with an annual capacity of 750,000 tonnes and a design speed of 2,000 m/min. It is designed for the production of very lightweight corrugated case material made from 100 percent recycled fibers. The production line comprises many novel papermaking innovations, including a mill-wide automation system. It is a true showcase of CO2-efficient board production. The new production line replaced three old machines at Palm’s Aalen site in Germany.
Palm PM 5 was started up in July 2021. It is a trendsetter for ultra-light weight corrugated base paper, providing further ecological savings in corrugated packaging.
Ready for future changes
“There’s a clear trend – even pressure – to be more sustainable in everything we do in the market. If we didn’t react to these demands, we’d probably quickly go out of business. I strongly believe that PM 5 has a sustainable lifetime that is much longer than 50 years,” says Dr. Wolfgang Palm, owner and CEO of Papierfabrik Palm.
“Corrugated boxes only have a great future as a packaging material if you can reduce CO2 emissions further in the production process. One way to do this is to reduce the basis weight. We worked closely with Valmet to design a board machine that could produce more lightweight containerboard than any other board machine in the world,” continues Dr. Palm.
Novel innovations for sustainable board making
“PM 5 features many technological innovations, which were tested and proven at Valmet’s pilot plants in Finland. An outstanding highlight is Valmet’s Sleeve roll technology in the forming section, which enables high water removal capacity without using any vacuum. We’ve already reached our dryness target, and we would absolutely install this unique technology again,” says Stephan Gruber, Managing Director and CTO of Papierfabrik Palm.
“We wanted to make a competitive investment for the next 50 years and aimed for a very wide and high-capacity containerboard machine to be ready for future changes. Valmet was selected because of their high-level and differentiating technology for lightweight grades. The concept was verified at the pilot trials,” says Dr. Wolfgang Palm, owner and CEO of Papierfabrik Palm.
He continues: “We selected a three nip press concept with Transfer belt system to remove open draw from the press to the drying section with an excellent dryness level. This has proved an excellent combination with the OptiDry Twin impingement dryer, which increases dryness and sheet temperature before entering the drying section. OptiDry Twin enables a very low deposit level at the beginning of the cylinder drying, and the drying section’s runnability components stay absolutely clean. There are no stickies or dusting at the pre-dryer section. In the drying section, the reliable and compact geometry of the Valmet Hirun Compact runnability system works very well to even further improve both runnability and cleanliness. We believe that selecting these innovations was the right decision.”
PM 5 features the novel OptiSizer Hard surface sizing technology for improved runnability, higher strength properties, the cleaning of starch in the recirculation, and lower operating costs than conventional film sizing. “The hard nip sizing is working really well, with excellent runnability. This is the right solution for low basis weight production with a low draw, high sheet stability and savings in starch consumption. Because the spray size application is contactless, the recirculated starch is never in contact with recycled fibers,” says Gruber.
“The reel and winder area are streamlined and highly automated, and roll movement is minimized, making it very operator friendly. The winder is like a robot that performs better and better every day. There aren’t any quality issues with the finished rolls,” Gruber explains.
Mill-wide automation as one platform
The industry-leading distributed control system (DCS), quality control system (QCS), machine control system (MCS), analyzers and measurements were selected for PM 5 to improve process performance and achieve savings in fibers, chemicals and energy.
“We’ve had very good experiences with the Valmet DNA Automation System, which is utilized mill-wide from the power plant and wastewater treatment system through to the stock preparation and paper machine to the winder,” says Dr. Palm.
“We see clear advantages for both operators and maintenance getting the mill-wide automation system from one supplier. The Valmet platform is very reliable, and there’ve been no issues with the start-up,” says Gruber.
Production line performance reinforced with the latest Industrial Internet solutions
PM 5 was started up during the Covid-19 restrictions. Valmet’s data-driven Industrial Internet applications with remote connections worked as a valuable support to achieve a world-class start-up. “Industrial Internet applications help us a lot, because Valmet’s specialists can very quickly connect to our process directly from Finland. Industrial Internet solutions are part of our daily routine – for example, in strength development with Valmet experts,” says Gruber.
“The end product quality shows we’ve selected the right solution. The very first paper produced just after the start-up was sellable without any waste. PM 5 has notable high-speed potential, because there are no open draws in Valmet’s machine concept, and the runnability is outstanding,” says Stephan Gruber, Managing Director and CTO of Papierfabrik Palm.
We worked closely with Valmet to design a board machine that could produce more lightweight containerboard than any other board machine in the world.
High-quality ultra-lightweight packaging material with low operating costs
The market for recycled containerboard has good prospects, especially due to its sustainability as a packaging material: it is renewable and recyclable. Containerboard production needs to deliver high efficiency and advantages in sustainability. Producing packaging grades with a low basis weight while maintaining high strength and excellent printing properties is always a challenge for board makers. Palm overcame this challenge with Valmet’s experts and the right solutions.
“If you produce ultra-lightweight board, you must achieve two things: you need to produce it efficiently and – even more important – economically. This means you have to increase the board machine’s speed much further. Our target was simply to have the fastest running containerboard machine in the world,” says Dr. Palm. “We’ve seen strong demand for ultra-lightweight containerboard, much higher than we anticipated. Our ultra-lightweight board strategy really is a major success.”
“We produce ultra-lightweight high-quality containerboard for strong packaging purposes, which means the same strength properties and more square meters in a roll than in conventional containerboard grades. The whole value chain starts from PM 5 and ends in households through e-commerce, for example. This means a much more sustainable supply chain,” explains Gruber.
Text: Marika Mattila
Photos: Palm
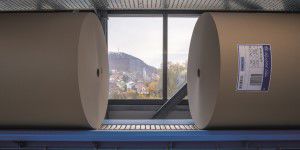
PM 5 is the world’s largest corrugated base paper machine, with a capacity of 750,000 tonnes per year. From 2022, the continuous development of their products has made it possible to achieve high grammage reductions by as much as 60 g/m². This means a material reduction of at least 15 percent, without sacrificing quality requirements.
Going strong: More than 1,000 winders and 50 Dual Unwind systems
Winders and their development have a long history at Valmet. We have already delivered more than 1,000 winders and 50 Dual Unwind systems, but their development is far from complete. The 1,000th winder delivered to Papierfabrik Palm PM 5 showcases all the great features it offers.
Palm values its gigantic winder: “It’s not just a winder for us – it’s a robot. Just one winder manages all the paper from PM 5,” says Stephan Gruber, Managing Director, CTO, Papierfabrik Palm. Having just one winder is a clear benefit for Palm: “It has reduced our investment cost compared to two winders, and it also reduces our personnel costs, because we need only two winder operators,” Gruber continues.
“The two key features of the winder at Aalen are the Valmet Industrial Internet (VII) and the Dual Unwind system to achieve high throughput,” Gruber says. Valmet developed the Dual Unwind system more than 10 years ago with the idea of having two unwinds at the winder. The innovation reduced parent roll change time from 6-10 minutes to one minute, improving winder capacity by as much as 50 percent. More than 50 Valmet customers are already enjoying the benefits of their Dual Unwind systems.
The VII provides completely new opportunities to optimize winder production and maintenance. For example, it can give detailed insights into winding performance, with data-driven analytics to avoid unplanned stops and increase end product quality.
Automation has always been an important part of improving winder capacity, usability and roll quality. When combined with a reel and automatic transfer rails, the entire reeling and winding process can be operated with a minimum of personnel safely and effectively, while providing higher production levels. The winder at Aalen is equipped with a Valmet DNA automation system to maximize its high performance.
Although Valmet is proud of its past and the 1,000 delivered winders, this is not the end of the story. Valmet’s two pilot winders are used to continually develop new innovations. And the culture of innovation will drive Valmet to create even better winding solutions for you in the future!
Palm PM 5 – a showcase of CO2-efficient board production
Valmet offers several technologies that enable the production of lighter board products without compromising on quality or visual properties. This is achieved with light weighting, which allows board and packaging producers to optimize raw material use, board quality and production capacity. The benefits of light weighting expand to each stage of the value chain: Packaging producers need less board for their products; transporting lighter products decreases the environmental impact; less energy is needed at every stage; and less waste is created thanks to recycling.
Palm’s PM 5 produces ultra-lightweight board in the basis weight down to 60 g/m2, which means raw material reduction of at least 15 percent, with comparable performance. In addition, OCC as 100 percent recycled raw material contributes to the conservation of natural resources.
The PM 5 replaces three old production machines, and it is equipped with the latest energy-efficient technological solutions, enabling substantial energy savings. Further environmental benefits are achieved through mill-wide automation, which improves process performance while enabling savings in fibers, chemicals and energy.