Empowering decision-makers through Mill-Wide Optimization
Production facilities across industries face increasing pressure to improve sustainability while meeting higher production and quality demands. Many initiatives address these challenges, yet a key opportunity remained untapped until now. Valmet optimization experts Greg Fralic and Matias Hultgren introduce the new Valmet Mill-Wide Optimization solution and benefits.
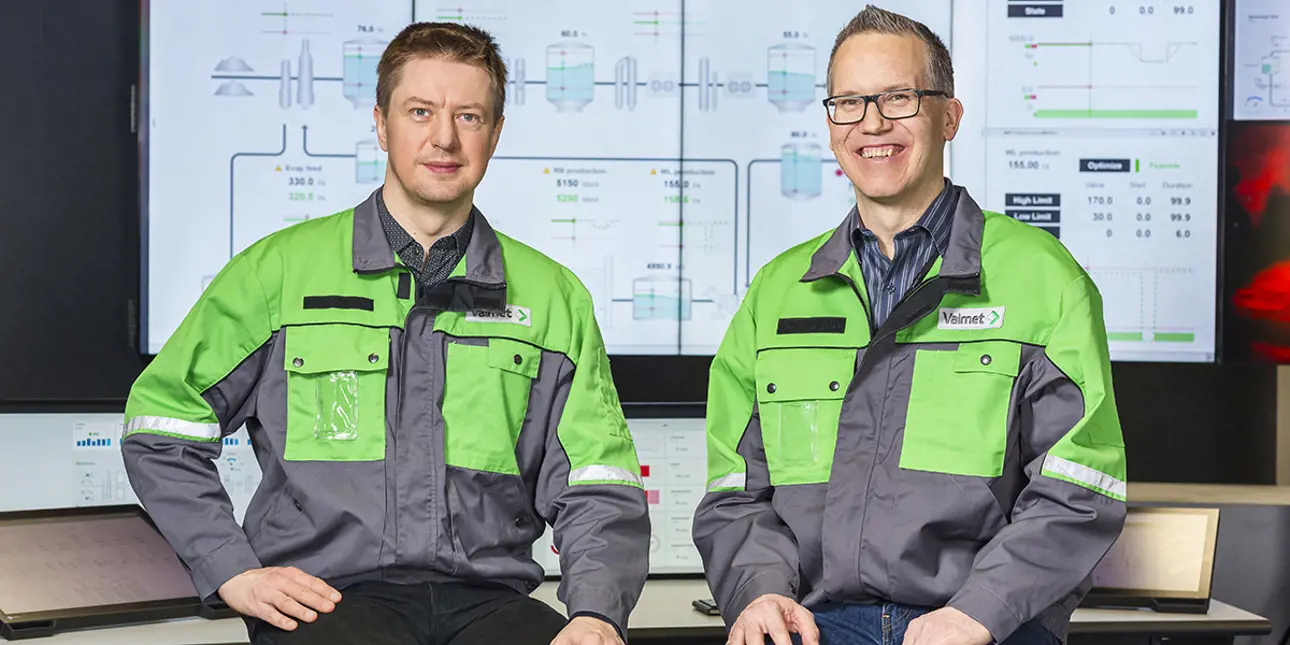
A hot topic now, particularly for pulp and paper
For decades pulp and paper producers have worked hard to optimize individual processes. However, the interactions between those processes, such as how chemical recovery performance impacts fiberline production, continue to limit throughput and quality.
“We built the Valmet Mill-Wide Optimization (MWO) solution to reveal a mill’s untapped potential,” says Greg Fralic, Product Manager, Mill-Wide Optimization. “It forms the missing link, bridging the gap between different process departments, helping mills orchestrate operations to achieve the best possible outcomes.”
The changing demographic of the workforce is also accelerating the need for a higher level of optimization. Experienced operators and engineers are retiring, with fewer younger recruits on the horizon. This is compounding the pressure from sustainability, costs and other factors that are driving demands towards increased performance.
Creating a digital flowsheet model
“The MWO solution uses a dedicated software platform to predict, optimize and visualize in detail the entire pulp and paper mill across all departments using mathematical flowsheet optimization,” explains Matias Hultgren, Technical Manager, Mill-Wide Optimization.
The mill flowsheet model used by the solution is a high-level digital twin of the facility, built by connecting individual unit process models together according to the process layout and modeling the relevant input–output relationships for each unit based on historical data.
The model is then simulated and optimized alongside the process multiple days into the future, based on real-time process data that is continuously used to update the model. This creates an advanced advisory solution, which leverages proven mathematical algorithms and Valmet’s extensive know-how to truly optimize the performance of the facility.
The solution uses the Valmet DNAe User Interface design language to create an intuitive main display. The main display is a compact flowsheet view of all process area trajectories. Directly from this visualization, users change the parameters for future production, quality and energy targets. Each process area and inventory can be adjusted, in addition to mill-wide targets.
The visualization helps users understand the past, present and future state of the whole mill, and offers practical guidance for achieving smooth and profitable operations.
“The visualization helps users understand the past, present and future state of the whole mill, and offers practical guidance for achieving smooth and profitable operations,” notes Fralic. “From mill management to process engineers, everyone can collaborate with a common understanding that was not possible before. The mill gains new opportunities for efficient coordination and collaboration across all mill departments to manage and optimize production.”
Planned changes are to the right; solid lines are past rates and dotted lines are future guidance. The tank shading shows states if guidance is not implemented.
Chasing the real bottlenecks
Once implemented, the Valmet Mill-Wide Optimization runs alongside the mill, constantly reoptimizing the production based on the current and future state of the mill, pushing the whole plant towards its real limits. The solution identifies upcoming bottlenecks that would impact the planned production targets and proposes changes to the relevant process areas.
"The location of production bottlenecks varies over time, determined by the current state of the mill and influenced by many factors, such as process equipment fouling and reliability," explains Fralic. "In our reference mill, we initially started with conservative cooking production limits. Over time, we expanded these limits until the true production bottlenecks, such as causticizing, were revealed."
"Mill-wide production planning helps to push productivity, but also to stabilize it by gradually driving mill inventories towards their preferred target levels. The calculation of liquor and lime inventory targets is automated based on the total balance and target distribution between tanks,” adds Hultgren. “You get a future projection of tank and chest levels with trajectories for non-optimized and optimized scenarios. Mill personnel can clearly see from the main display where department and inventory high or low limits become bottlenecks in the future.”
For slowdowns or shutdowns, the MWO solution first assesses whether a feasible setup exists within the specific process limits. Following this pre-solve step, it optimizes the production rates and inventories across the entire time horizon. Once the numbers are processed, teams get guidance on how to build up or draw down inventory in each subsystem to minimize production disturbance.
Addressing energy and quality optimization
Mill-Wide Optimization can be utilized to ensure that the mill meets necessary quality specifications, while minimizing costs, generated waste, and the overall carbon footprint. The solution also enables things like smarter integration with local energy grids for a better balance between consumption and generation.
“When production is fully optimized, we can incorporate energy planning and quality planning into MWO,” continues Hultgren. “The solution coordinates the quality targets across all process stages. Through quality planning, we determine current and future quality for each stage, accounting for upstream and downstream disturbances and process dynamics.”
In pulp and paper production, the MWO solution can optimize the cost of bleached pulp brightness based on digester yield and chemical costs. It can also be used to optimize pulp strength across each stage of a kraft mill or optimize furnish mix and quality for converters.
Optimization results even better than expected
"For brownfield mills, we can perform a Mill-Wide Optimization Audit to evaluate the benefits by conducting an analysis that re-optimizes past mill operations based on historical data," says Fralic. "This gives the mill a realistic baseline for what to expect in the future with MWO.”
Once implemented in practice, the mill achieved a 5.2% increase over the first eight months, including two months of record high production.
At a reference mill in Europe, for example, a full year of data was re-optimized to identify the production potential and possible bottlenecks. The predicted improvement was a 4.5% increase in production. Once implemented in practice, the mill achieved a 5.2% increase over the first eight months, including two months of record high production.
Who benefits from Valmet Mill-Wide Optimization?
This is a new type of solution that connects different levels of the mill organization. It supports operators and guides day-to-day actions. It helps production managers and process engineers set process targets that reduce the mill-wide impact of scheduled maintenance.
Valmet Mill-Wide Optimization empowers personnel at all levels of operation.
Teams can finally transition from reactive to proactive decision-making, giving everyone the time needed to both plan and prepare for future changes and manage unexpected disturbances when they occur. When everyone shares the same situational awareness, teams can transparently collaborate and coordinate actions towards common goals with a common understanding of where the challenges and opportunities lie.
Services add the ingredients for success
“For major decisions, production facilities have relied on the experience and know-how of senior experts” notes Hultgren. “These experts have their own way of doing things, even their own custom tools, to help them reach good decisions. With the Valmet Mill-Wide Optimization solution, the expert-centric decision process becomes a synchronized team effort.”
Instead of working in isolated teams, everyone needs to coordinate actions for multiple process areas. This is a significant shift in the ways of working that Valmet’s expert services help customers learn and adopt. Workshops and training sessions with our experts prepare personnel and align expectations that benefit the entire operation.
Mill-wide optimization also requires good data from the processes. Real-time measurements and intelligent process technology ensure customers get an accurate picture of the current situation and the forecasted future.
Valmet's worldwide service teams help mills establish the technological foundation for optimization success. Through continuous collaboration with customers, Valmet experts also ensure the Mill-Wide Optimization solution delivers consistent performance improvement and long-term value.
Text: Randel Wells
Optimization actions
Debottlenecking: adjusting process areas that are limiting production to achieve full production capacity capability
Balancing: running production according to plant-wide inventories
Planning: adjusting for known, isolated events to minimize the impact on production and speed up the recovery
Related articles