High-quality tissue machine clothing
For all positions in the tissue machine
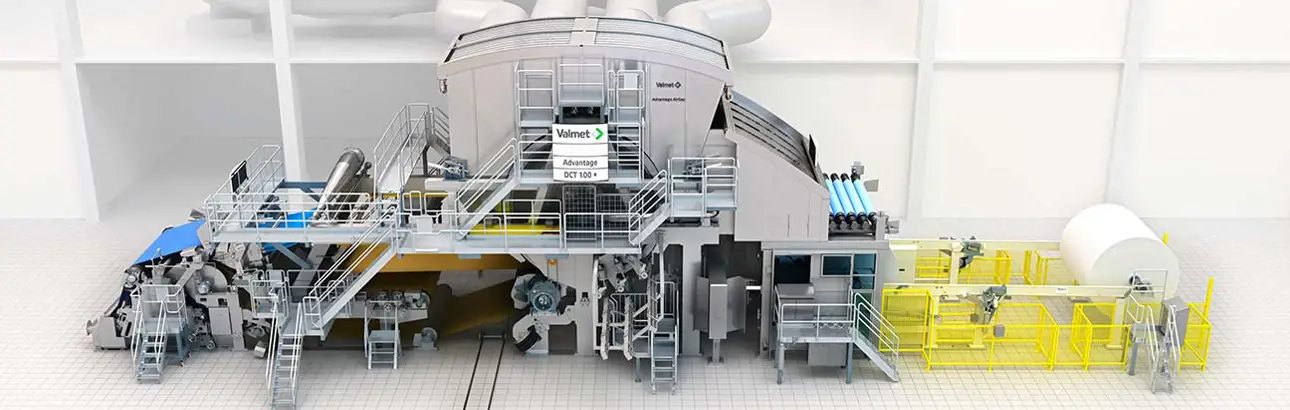
Forming fabrics, press felts and shoe press belts are developed hand in hand with tissue machines. Focused R&D, professional workforce and innovative approach are key in developing fabric structures that meet customer demands on performance, quality, energy savings and cost reductions.
One important step in the development phase are the test runs performed at Valmet’s pilot machine in Karlstad. Each forming and press position of the tissue machine requires a product especially designed for its conditions.
Valmet's tissue machine clothing is tailor-made and optimized according to your needs. Our application expertise together with repeatable high quality clothing ensure a reliable production process with lowest possible life cycle costs without compromising the end quality. The right fabrics, felts and belts also clearly contribute to energy savings.
Explore our machine clothing and filter fabrics for tissue making
Want to talk to our fabric experts?
Our professionals are here for you, let us help you with your concerns.
Contact usArticles and news
