Valmet DNA Distributed Control System
One system for all process automation needs
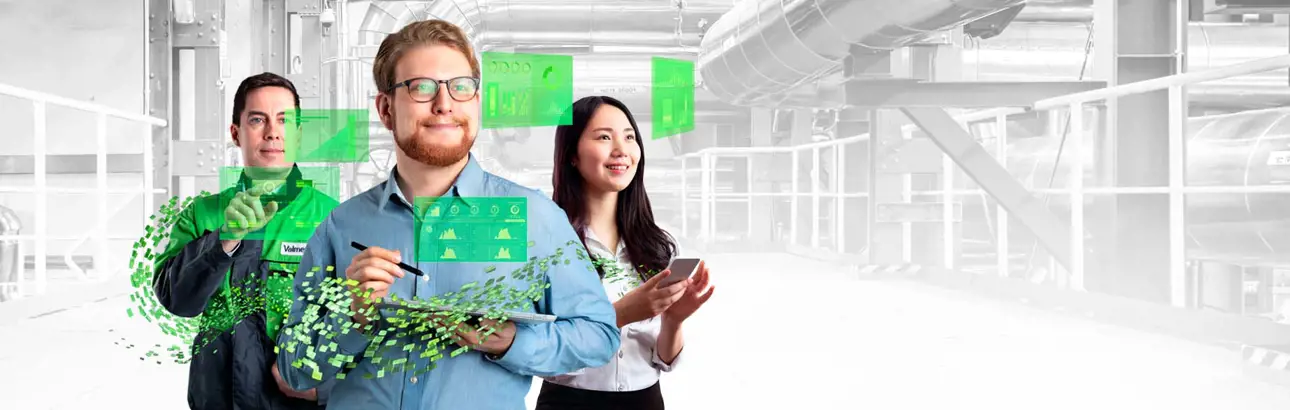
Valmet DNA is a future-proof Distributed Control System (DCS) designed to fulfill your process automation requirements across various industries, including pulp mills, board, paper and tissue machines, energy and hydrogen production, marine, and process industries. With Valmet DNA, you gain full command over all your processes and enjoy an exceptional user experience that surpasses conventional industrial control systems. This versatile DCS can be utilized for process controls, machine controls, drive controls, quality controls, and condition monitoring. Information management is integrated into the platform, and its unified system architecture ensures scalability and reduces costs.
The leading DCS user experience in pulp, board, paper and tissue mills, energy, marine, and process industries
Built-in control, optimization, condition monitoring, advanced analytics, and remote support
Certified cybersecurity based on ISO 27001 & IEC 62443-4-1 standards
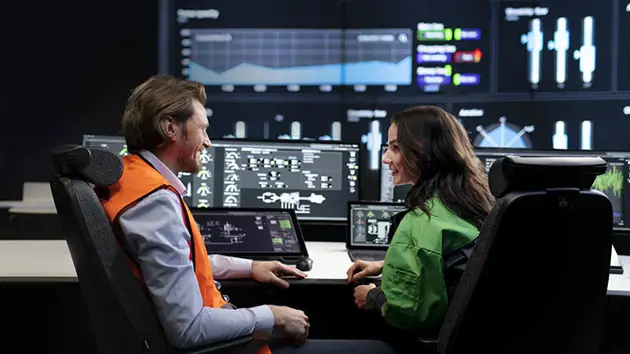
User experience
Towards autonomous operations
Valmet DNA distributed control system (DCS) integrates all the process automation needs under the same system. It enables effortless migration from your existing DCS and PLC systems and facilitates easy operator onboarding.
The system's new generation Valmet DNAe User Interface makes the most meaningful information available to all process automation users according to their roles, regardless of their location.
Built-in control & optimization
Interoperable applications
Valmet DNAe User Interface enables easy use of all control & optimization applications through the same user interface. Applications share the same data assets and visualization principles, making Valmet DNA the easiest-to-use automation system on the market.
Trends and event information are available through the same user interface. You can drag and drop any signal from any application to utilize the trend data. Instant troubleshooting, reporting, and process development take your operational efficiency to the next level.
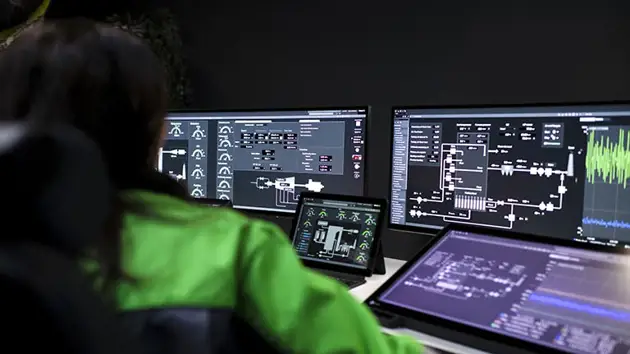
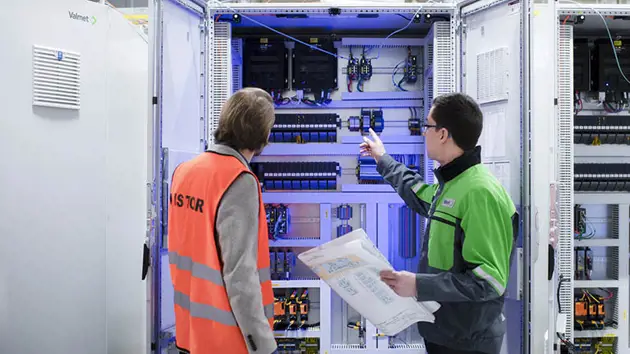
Reliable controllers & I/O
Robust DCS hardware
Valmet's future-proof controller and I/O family ensure a dependable platform for all your controls and external connections. These control nodes support the modern ACN I/Os and main industry field buses, such as PROFIBUS, PROFINET, Ethernet/IP, FF, and AS-i. Standard links like OPC DA, OPC UA Ethernet, and serial links ensure excellent connectivity to third-party systems.
Certified cybersecurity
ISO 27001 + IEC 62443-4-1 standards
Valmet DNA is the leading platform in cybersecurity. The security has been externally certified per the requirements of ISO 27001 and IEC 62443-4-1 (SDLA).
Valmet DNA automation system uses the Defence in Depth (DiD) approach from the beginning. The extensive Valmet Cybersecurity Lifecycle Services provide protection against any threat that might occur.

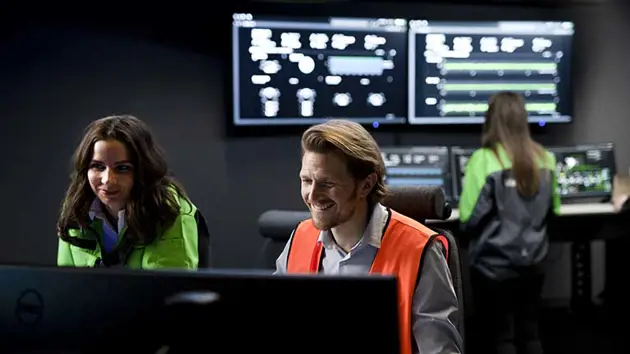
Information management
Valmet DNA Information management
Modern process plants generate a vast amount of online data that is often stored and processed efficiently for later analysis. Valmet DNA Information management combines process interfaces, calculations, and databases into one uniform solution.
Databases store all measurements, setpoints, controller outputs, device statuses, motor starts, alarms, operation tracking etc. into history databases.
Engineering & maintenance
A scalable multiuser environment
Distributed control systems are used in different kinds of processes, often requiring a scalable multiuser environment for concurrent engineering. Valmet DNA Engineering environment contains versatile tools to engineer and maintain plant automation.
The tools allow life cycle management for all control applications, field buses, and field devices, as well as network document management. In addition, advanced diagnostic tools offer easy maintenance support for both applications and hardware components.
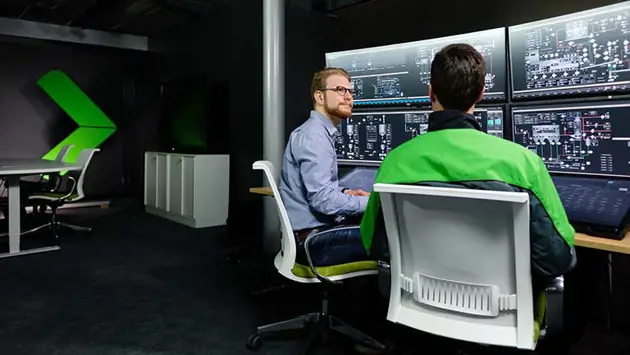