Meeting customer needs – with Valmet Recovery Boiler technology
In the last few years, we have seen a boom in pulp investments in China, where Valmet has five ongoing recovery boiler projects. The key drivers for recovery boiler technology selection have been to achieve high availability, a high reduction rate and energy efficiency.
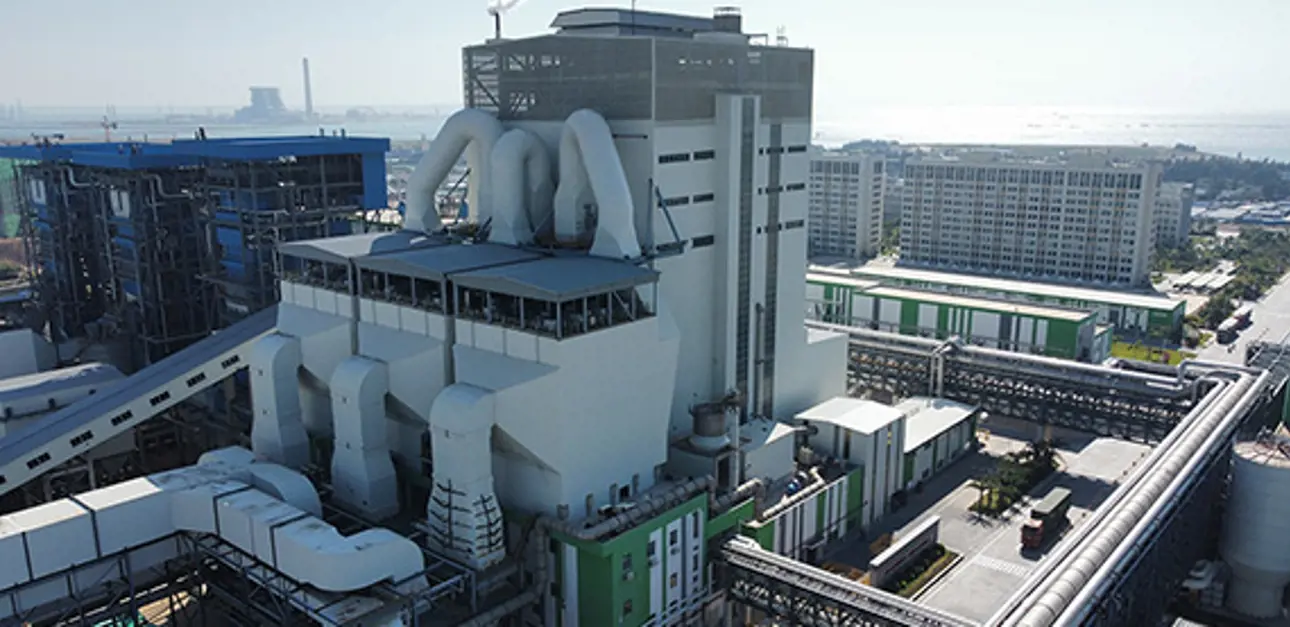
The recovery boiler is typically the most visible building at a pulp mill, rising 60 to 80 meters above the ground. The recovery boiler also plays a key role in a chemical pulp mill’s chemical cycle, as well as in power and steam production.
We would not have been successful in these projects without the capability of executing them locally in China.
The capacity of pulp mills and therefore recovery boilers has increased significantly in recent decades. In addition to increasing in physical size, the technology has been developed to be more resource efficient. The chemical recovery efficiency has improved, and the boilers play a key role in handling the mill’s odorous non-condensable gases. With high-power features, pulp mills can produce significant amounts of renewable energy for paper and board production or for the national grid.
An investment boom in China
“In recent years, we’ve seen many new pulp mill investments in China. These mills are built with the latest technology. For us, the latest boom started with a project for Huanggang Chenming Pulp & Paper in 2015. Over the last two years, we’ve had five ongoing recovery boiler projects in China at the same time,” says Jussi Mäntyniemi, Vice President of the Recovery business unit at Valmet.
The recovery boiler start-up at the Sun Paper Beihai pulp mill went smoothly.
In late 2021, a recovery boiler Valmet delivered was started up at Sun Paper’s new Beihai pulp mill. Three recovery boiler deliveries are scheduled to start up at Nine Dragons’ pulp mills in 2021 and 2023, and one recovery boiler will start up in 2023 at Asia Symbol Shandong’s Rizhao pulp mill.
Technology that meets customer needs
The customer drivers for these investments in China are very much the same as anywhere else in the world. From the mill’s operational perspective, the goal is to achieve high availability and a high reduction rate. Energy efficiency and power production have also become increasingly important.
“We’ve been able to meet customer needs with our technology and local presence in China,” says Jussi Mäntyniemi, Vice President, Recovery business unit, Valmet.
“The key to us winning these projects has been successful concept development. We’ve been able to meet customer needs with our technology and local presence. The phase out of coal and the preference for biomass-based power production have become a significant driver in recent recovery boiler investments. With various high-power features, we can produce between 20 and 25 percent more electricity than with traditional designs. The emissions limits are very tight in China. We’ve already successfully delivered NOx scrubbers for existing recovery boilers, and some of these new mills will also be equipped with them,” Mäntyniemi explains.
![]() |
|
“In selecting Valmet as our partner, we’ve had many expectations of their technology. We have low carbon emission targets, and we want our partner to help us achieve high energy efficiency and low consumption. In our Beihai project, the recovery boiler start-up went smoothly. We enjoyed positive cooperation with Valmet, which demonstrated their technical and project execution capabilities,” says Ying Guangdong, Vice General Manager and Chief Engineer at Sun Paper.
Successful delivery during Covid restrictions
These projects have been executed almost completely during the global Covid-19 pandemic. This has caused delays to shipments and has significantly restricted travel.
We enjoyed positive cooperation with Valmet, which demonstrated their technical and project execution capabilities.
“We would not have been successful in these projects without the capability of executing them locally in China. Our teams in Tampere, Finland, Chennai, India and Shanghai, China have worked seamlessly together in engineering and project delivery. We were unable to send in commissioning teams from Finland, so our local teams took on the challenge, and they did a great job with our customers. Some of our key experts provided remote support from Finland. This has also taught us how we can serve our customers better and faster in the future,” Mäntyniemi concludes.
“I’m very proud that despite the challenges in our operating environment the pandemic has posed, all the projects are proceeding to schedule. It’s easy to collaborate with customers when there are professional teams on both sides. I can say that we really do stand behind our motto of being the global champion in serving our customers,” says Yingmin Yu, Senior Manager, Valmet’s pulp business in China.
Text Lotta Forssell
Related articles