An intensive, educational and successful bale handling project
In 2021, Nordic Paper Säffle invested in a new bale handling system from Valmet to controllably handle incoming pulp. The amount of received pulp increased, as the mill ended its production of sulfite pulp after 138 years and switched to using only purchased sulfate pulp for its paper machines.
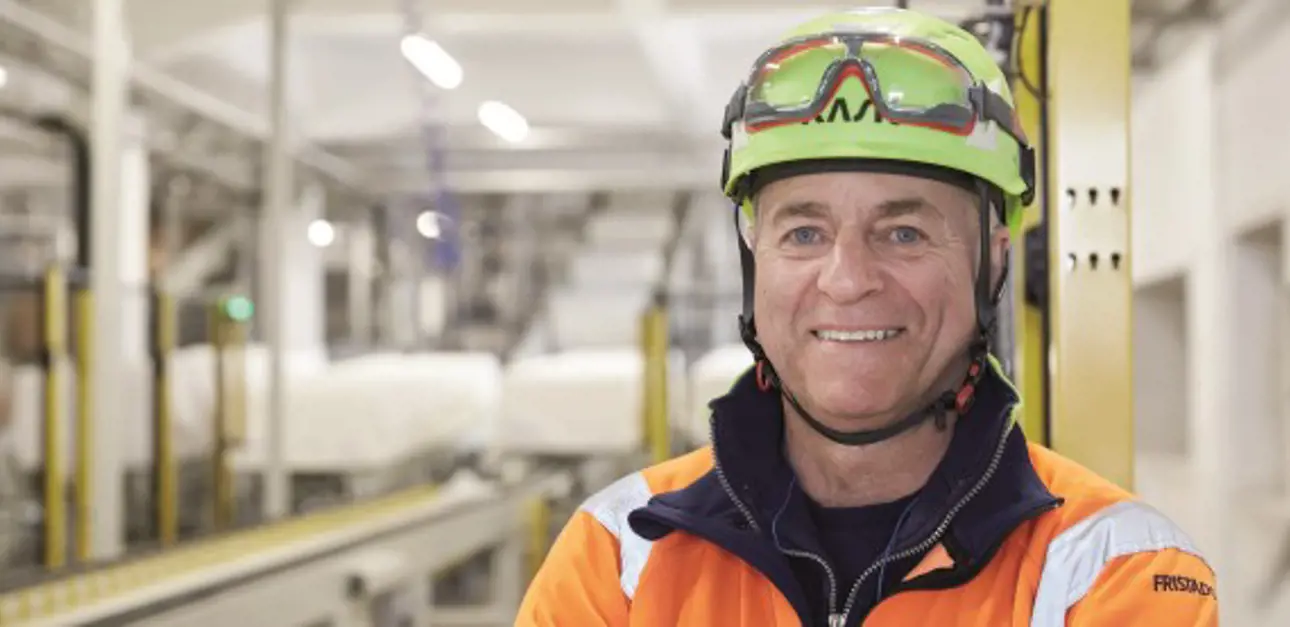
The main reason for investing in this bale handling system is that we produced far too little pulp for it to be at all economical. Safety needed to be improved, and the plant was simply obsolete,” says Peter Bergkvist, Project Manager at Nordic Paper. At the end of April 2020, it was officially decided to close down the pulp mill. This was expected, and discussions about various suppliers for the conversion project had already started. The plan was to build a new bale handling line in an existing building. Valmet was chosen as the supplier of both pulpers and the bale handling system.
Fast start-up of the new installation
“We looked for a supplier that could offer a complete solution, and the pulpers also needed to be low if they were to fit. Only Valmet could handle this,” says Bergkvist.
Bale handling overview.
The bale handling system consists of an automatic dewiring and pulp delivery solution. The system was checked out, and the last connections were made during Christmas week, when the factory was at a standstill.
We looked for a supplier that could offer a complete solution, and the pulpers also needed to be low if they were to fit. Only Valmet could handle this.
“It couldn’t have gone better. The deadline was January 3, 2022. That’s when we could start, and we did. Of course, it wasn’t painless, but we worked on and delivered the first pulp to PM 3 three days later. It’s basically been running all the time ever since. We haven’t stopped a minute because we’ve been out of pulp, which is absolutely fantastic,” says Bergkvist.
Automatic recipe handling is a prerequisite for good quality
The dewiring line’s control system ensures the correct pulp grade is delivered to the respective pulper based on which recipe the paper machine operators decide to run. The operators in the bale handling area are told which bales to load onto the line. The recipe handling software automatically calculates the mix of bales needed to ensure the required quality and guides the movement of bales to keep the production flow constant.
“Since we have different recipes for each paper machine, automatic recipe handling is a prerequisite for us if we’re to maintain good quality, quick changes, and good productivity on the machines,” Bergkvist explains.
Henrik Smedjegård, Project Manager at Valmet
An intensive and successful project
The project has been extremely intensive. The logistics had to work. Transportations had to arrive on time and in the right order. Everything had to enter through the same gate, and there was no room to move equipment around inside.
We haven’t stopped a minute because we’ve been out of pulp, which is absolutely fantastic.
“The equipment from Valmet was taken directly from the truck into the new premises and assembled by Valmet and some local contractors. There have been several challenges in the project that have been overcome with good cooperation. The biggest challenge was probably the short time schedule,” says Henrik Smedjegård, Project Manager at Valmet.
The displays are easy to use. The operators have quickly learned through on-site training from Valmet. Per-Arne Olsson, Operator at Nordic Paper, in action using the display.
“The response and commitment from everyone involved in the project has been extremely important to us in the project group, and we’ve really succeeded – the new plant was up and running on time. Very few people have been involved. The secret to the success is probably that they’ve worked very closely and have had many review meetings. It was intensive and educational – and above all, it was successful!” Bergkvist concludes.
Text Kerstin Eriksson
PHOTOS Torbjörn Bergkvist
Nordic Paper Säffle
The products manufactured at Säffle mill are natural greaseproof paper, and Nordic Paper is one of the largest brands on the market in that niche. The paper, which is produced without any added PFAS, is mostly used in the food industry, for everything from pan liners to food packaging and baking molds. It is a growing market because of increasing awareness about sustainable materials. Greaseproof paper is the natural alternative to aluminum and plastic.
“People tend to eat more at restaurants and coffee shops – dining out is becoming increasingly common, and this trend is supporting our business worldwide,” says Peter Bergkvist.