No time to waste - textile industry’s new dawn is here
Novel cellulose-based textile fibers are changing the game for the textile branch. The textile industry now strives to meet the requirements of increasingly sustainability conscious consumers and the more stringent legislation to strengthen its license to operate.
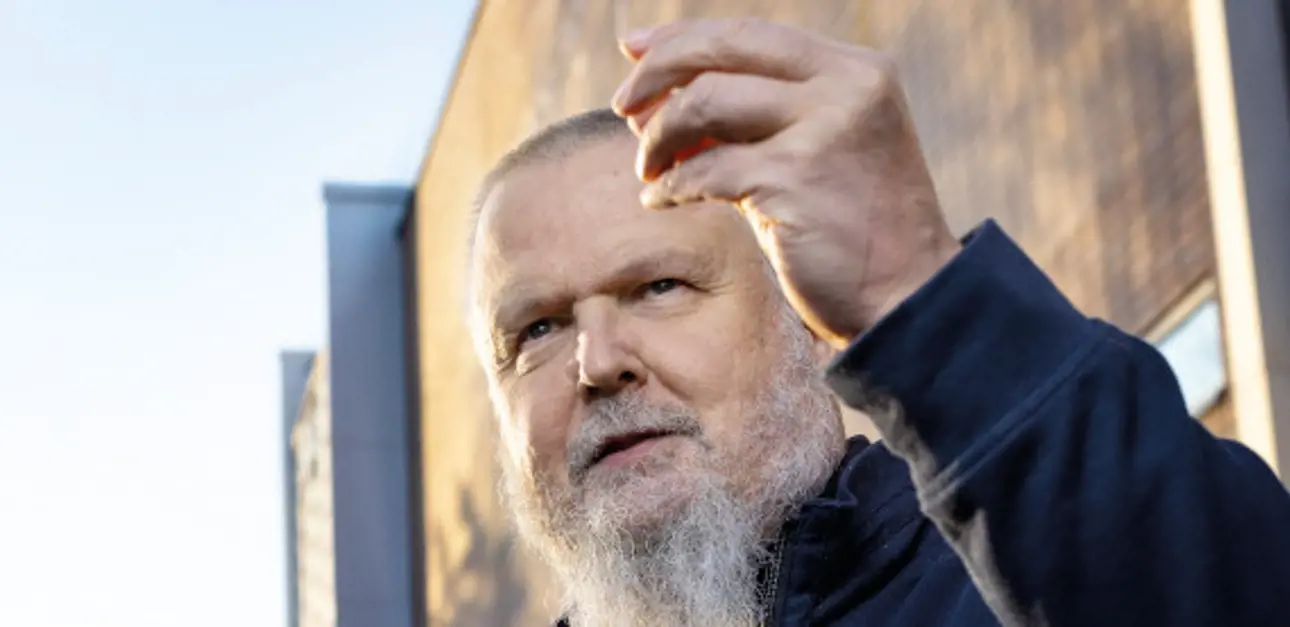
The most-used textile fibers in the world today – cotton and polyester – are challenging from the sustainability point of view. Cotton farming is land-, chemical-, and water-intensive. Approximately 2.5 percent of the world’s land area suitable for food production is used to grow cotton. The demand for cotton is high, but environmental challenges restrict its availability.
Polyester, on the other hand, is made of non-renewable fossil raw material, oil, and contributes to the microplastic burden we face today.
“With the demand for clothing and other fiber applications increasing steadily, there is a shortage of more sustainable and responsible fibers globally,” says Research professor Ali Harlin from VTT Technical Research Centre of Finland.
Harlin, with a background in polymer engineering, has been following and working with the world of textiles for over 20 years. His area of responsibility at VTT is the bioprocessing of renewable natural materials, and he is an active initiator and actor in the process that is now transforming the textile industry into a more sustainable branch with a brighter future.
Room for several new technologies
Further driving the development towards more sustainable fibers and production processes is consumer desire for more environmentally conscious clothing and for more transparent value chains, as well as the more stringent, circular economy pursuing EU legislation making textile recycling obligatory starting in 2025.
![]() |
According to Ali Harlin, there are alternative streams to produce textile fiber from cellulose-based raw materials: wood-based fibers, recycled cotton and viscose, and agricultural residue fibers, such as straw or bagasse. |
Some visionary companies have developed technologies that enable the textile industry to use new, more sustainable cellulose-based raw materials and textile and other waste to generate fibers – and with excellent results. Several technologies are near commercialization. Do we really need them all?
“Textile fibers are used to produce high-quality, luxury fabrics, denim, work clothes, and nonwovens, and as composites, to mention some of the end-use areas. This means that there is a need for fibers with varying properties produced through different technologies,” says Harlin.
Use of textile waste still challenging
According to Harlin, there are alternative streams to produce textile fiber from cellulose-based raw materials: wood-based fibers, recycled cotton and viscose, and agricultural residue fibers, such as straw or bagasse.
The most challenging of these three is, perhaps surprisingly, recycled textiles. The new legislation is likely to increase the availability of recycled textile in the EU, but there are still some challenges to solve. For a successful fiber production process based on textile waste, quite precise material information is needed for every piece of clothing going into the process.
“Clothes are complicated, not only with respect to their material or more accurately mixture of materials. There is a need for a digital platform that helps to identify material information or even brands and what sort of clothing is involved. How this can be done in reality is still being explored; even if RFID tags may offer a solution, there are issue that must be solved for example regarding privacy,” says Harlin.
Recycling would be much easier, of course, if clothes and other textiles were designed with recyclability and other sustainability themes in mind already from the start.
Sustainable innovations behind new technologies
Many novel fiber production solutions are based on the dissolving of cellulose. A traditional dissolving pulp from pulpwood is used for producing viscose – the downside is that the production process requires carbon disulfide, which is harmful both for people and the environment. Now, new, environmentally friendly and recyclable solvents have been introduced.
One of the latest dissolving technologies uses urea to produce cellulose carbamate fibers from cellulose-based recycled and residual materials. These fibers can be used to replace cotton and are suitable for use in a variety of applications. The production process consumes less water, chemicals, and energy than producing cotton – and the biodegradable fibers can be used repeatedly without any losses in performance.
Some other interesting fiber production processes introduced use a novel solvent called ionic liquid, an environmentally sound solvent that can be recycled. These processes use wood, wood pulp, recycled paper and board, and textile waste as raw material. Depending on the exact process and the raw material used, the fibers generated work well both for clothing and technical applications, and they are recyclable and biodegradable.
There is a need for fibers with varying properties produced through different technologies.
Another kind of approach – a “rebellious” one, as Harlin says – is the one where paper pulp is refined mechanically into microfiber, and a textile fiber is produced from the microfiber and water without any chemicals.
“The future may bring even more innovative solutions. Who knows, maybe someday we’ll grow cotton fibers artificially,” suggests Harlin.
Interdisciplinary collaboration needed
Sustainable fibers are, however, only the first step in the textile value chain. The fashion industry needs to meet consumers’ growing demand for sustainable, yet personalized, clothing.
“Succeeding in this will require a marriage between technological innovations from different areas and AI applications. It seems that many of these ’pieces’ already exist. Now it’s time to leverage them to create new business models – and excellent customer experiences – to really capture the potential of the whole value chain,” Harlin concludes.
Text Sanna Haanpää-Liukko
Photos Tomi Parkkonen
Related articles