Joining forces for innovation with SAICA El Burgo's new off-line coating machine
SAICA was aiming for improved quality, reduced costs, and responsible fiber use, but it found itself with innovative coated white top liner grades with better properties than they bargained for. This was a result of three partners – SAICA, Valmet and pigment supplier Omya – joining forces.
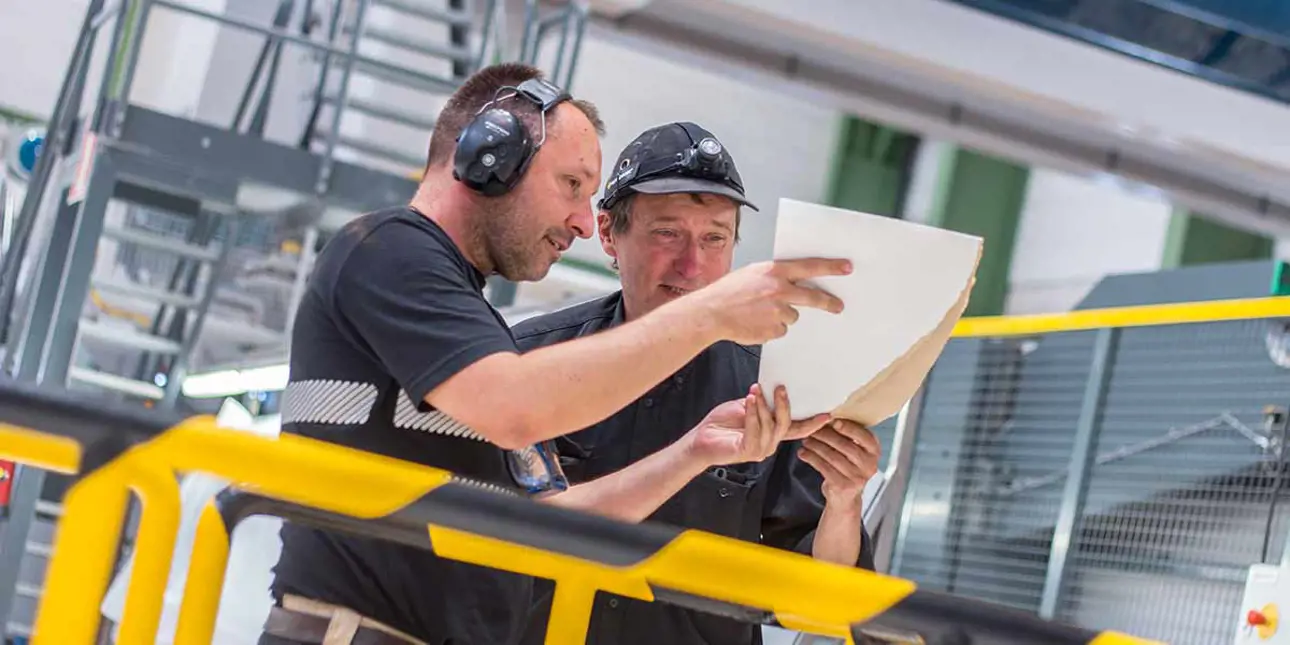
"SAICA is a fully integrated containerboard producer. We go from recycling of paper all the way to box production. Among the players in the containerboard market, we consider ourselves as the one with the strongest focus on papermaking innovations,” says Federico Asensio, Group Director for R&D&i at S.A. Industrias Celulosa Aragonesa (SAICA). “Our idea with the new offline coating machine was, if we wanted to replace white fibers with something else, it had to be printable with a standard flexo printing technology,” Asensio says. Having the full cycle of box production in its own hands, SAICA started its development journey for the new product together with Valmet and the pigment supplier Omya.
“We were about to do something nobody else had done before. We knew that Valmet wanted to make this project fly.”
A cycle of trial and improvement
Trust and partnership have been the forces carrying this project forwards. The development partnership between SAICA and Valmet was completed when pigment supplier Omya joined. This group had what it took to make excellent boxes. Asensio describes the three partners: “We worked as a group, as a team. We made the base paper at our industrial units, and we went together to Valmet’s pilot facilities to coat it. We took the new paper to our corrugators and converting units to produce the board and run the printing trials. It made us realize the goal was achievable, although there was still room for improvement in several variables.” The cycle of development started again – the cycle of trial and improvement. Eventually, SAICA and Valmet shook hands on a complete offline coating machine.
![]() |
“The paper had better brightness. It was totally even, with none of the impurities that usually result from recycled fibers,”
|
Pilot trials: a key element
Being able to test the final products at each step of the path has been essential. The pilot facilities at Valmet Paper Technology Center have been key to this. Alberto Mena, Head of Pulp and Chemicals for R&D&i projects at SAICA, explains about the pilots: “The final product is much better than we expected. This is due to the pilot trials. The people there were very flexible. We needed to make many modifications to the pilot machine and trial programs. They never expressed any irritation, and they always did their best. The flexibility was impressive – we believe it’s the best pilot facility we’ve ever used.” SAICA’s Innovation Technology Project Manager for R&D&i Diego Compaired was also complimentary: “The pilot trials sped up the coating definition with an opportunity to test different ingredients and different coating amounts.”
Now that the coating machine is up and running, the benefits of the pilot trials are clear. Sergio Alonso, Production Manager of PM 10 & OMC at SAICA, explains: “Now we are only fine-tuning the machine. The pilot trials ensured the very first rolls were of high quality.” The first high-quality rolls were produced by the end of January 2018, with the new coating machine.
Clear targets
The main idea at the beginning was to replace the white fibers with something else to save on costs and improve the appearance quality of the final paper. There were also other targets, as Compaired reveals: “One target of this project was to increase our product range, as we had a lack of coated grades. We wanted to offer our customers a wide range of products made from recycled raw material. The process we developed is one of the most innovative in the world in the recent years.”
OptiCoat Layer curtain coating
Using only brown fiber requires quite a lot from coating. “We wanted to have a wider range of products, to have more flexibility in the market. The coverage is very good, too. It is the main reason why we are not using a white layer of fibers. The very first day that we were coating, the appearance of the paper was excellent – much better than white top liners,” says Alonso about the importance of the even coverage of curtain coating and the good results of the project.
In May 2018, SAICA launched the new Infinite collection of high-quality, 100-percent recycled white papers.
Alberto Mena (on the left), Head of Pulp and Chemicals for R&D&i projects, and Diego Compaired, Innovation Technology Project Manager of SAICA.
More than bargained for
The results were much better than expected. “After some trials, there was a moment in the research project when we realized that the behavior of the new grade was completely different to the ones we wanted to replace. The paper had better brightness. It was totally even, with none of the impurities that usually result from recycled fibers. There were no minor defects of colored fibers, black spots, or changes in other color variables. But the most important property was the enhanced brightness of the paper, and the lightness and intensity of the printing colors. The colors appeared glossier,” Asensio explains more about the development phase.
“With standard white top testliners, you cannot control the three variables of whiteness. With this new way to produce the paper, we could control those with each parent roll. We managed to supply the market with products that add real value. It is a big advantage to have a very good-looking box at a very affordable price compared to the traditional double-coated grades,” Asensio continues. SAICA had managed to develop a novel product and with more properties than they bargained for.
Very positive feedback on the new grades
Customers who have experienced the new grades have been very positive towards the products: OMC Superintendent Javier Garcia Muñoz from SAICA shares their comments: “We have received very positive feedback from our customers about the quality and the printability of our papers.” Compaired adds: “Our customers are quite impressed with the performance of our papers. In terms of printability, they perform very well. The behavior in corrugating lines is very good. In fact, compared to the competition, this paper can be glued much more easily on corrugating lines, offering the possibility to reduce glue consumption. It also reduces the washboard effect – it gives a much more uniform surface on which to print.”
The new off-line coating machine.
A beautiful story of partnership
Customers seem to be very satisfied with the new product range. For Asensio, this was also a journey of trust and partnership: “When you are looking at an innovation project, you need to feel comfortable and trust the capabilities of your supplier – your partner. We needed a very strong partner capable of reacting to unknown events – we were about to do something nobody else had done before. We knew that Valmet wanted to make this project fly.”
“This is a very beautiful story of partnership. Together, the three of us have succeeded in delivering an innovative grade to the market. Together, we added value to our customers, to brand owners,” says Asensio and finishes the story of the new Infinite products.
OMC Superintendent Javier Garcia Muñoz from SAICA: “This new coating machine has met the requirements for us in the coating process. The most important pieces are the supply system, the coating head applicators, and the air dyer system. And all of them have been running very well and efficiently. In my opinion, SAICA choose Valmet because of the technology.”
TEXT Pauliina Purola PHOTOS Joonas Nieminen
Related articles on innovations and R&D