The paper machine and user experience
From the first sketch to the final product, how something works should be discussed every step of the way. Digitalization is shaping the working environment at paper mills as well, and when data meets the physical world, things can get complicated. When Valmet develops future paper machine solutions, the focus is on how people feel about using the system as much as it is on performance.
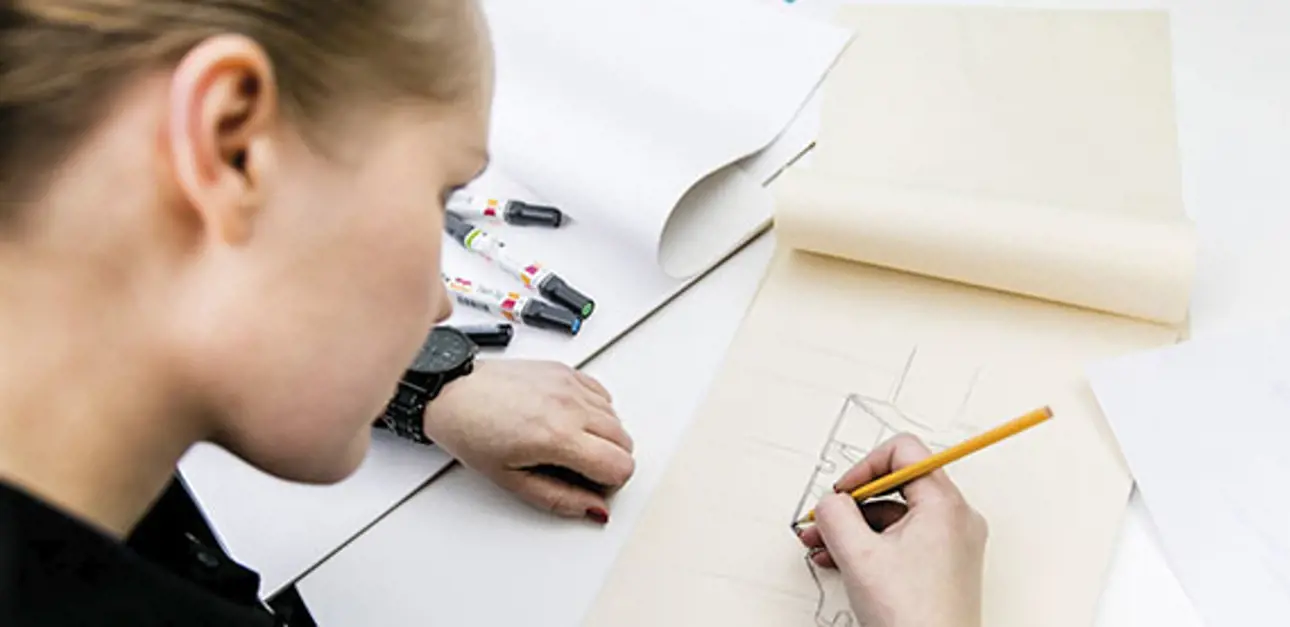
“There are several definitions for user experience, depending on the background of the person giving the definition,” says Mari Airio, Industrial Design Manager at Valmet, who is responsible for the design of the user experience (UX). “I’d say user experience is about how users feel when they use a certain product, service or system. In recent years, the hype around digitalization has led to a wider interest in the topic, so UX has been often defined in digital contexts,” she explains.
UX in the papermaking industry
Besides digital user interfaces and applications, the user experience is about what the interaction between the human and the machine is really like. “UX starts from the first moment a user encounters our products. Be it reading a maintenance manual, at a product training event, or doing actual maintenance work. UX can be considered as being part of the early stage of a product’s life cycle, like assembly: How does the assembler feel about the product during installation? How easy is the product to manufacture or engineer? UX affects the whole delivery process and of course end users”, Airio says in explanation. “At Valmet, we want to consider UX from its widest possible perspective. You should never limit UX only to the UX of one product, but always consider the whole process in question,” she argues.
Why should our customer be interested in UX?
From the customers’ perspective, UX makes using products more effective and safer. According to Airio, designing technical maintenance work to work seamlessly with machinery can reduce monotonous maintenance actions. This, in turn, motivates users, making it easier to learn and understand the product. This reduces mistakes and makes things quicker. “When the user gets a sense of being in control, it amplifies the feeling of the experience, and this reduces frustrations and lessens everyday struggles,” Airio says.
From a broader perspective, digitalization and the Industrial Internet are bringing in more applications and data, which in turn are making the working environment more complicated. Airio sees a need for solutions that help users to operate both in the physical and digital environments. “The physical and digital worlds really are inseparable. We need to help users handle both new applications and machines at the same time, and to work effectively in that interface.”
From the customers’ perspective, UX makes using products more effective and safer. Designing technical maintenance work to work seamlessly with machinery minimizes repair times and eases cleanability.
Users’ needs in focus
Valmet has been systematically focusing on industrial design and usability for several years. The OptiConcept M paper machine is a good example of this work. It has been designed with the needs of its users in mind. The design of the machinery allows easier and safer changing of rolls and wear parts, thus reducing the duration and cost of service shutdowns. The new, more spacious walkway design improves accessibility and safety also on the drive side, and all tending side walkways are at one level, eliminating the need to walk up and downstairs. There is also no need to remove walkway parts during fabric changes or monthly maintenance procedures.
“With the design of the OptiConcept M, we’ve tried to remove critical UX errors. It creates a great base to develop the user experience further,” Airio says. Recently, Valmet has been studying how to use light as a visual element to improve usability and safety. “Lighting can be an integral part of the whole machine environment – we can light up the machine parts and sections that are critical at any particular moment, and fade out the lights in areas where they aren’t needed. And the new LED screens beside the paper machine make the internal world of the machine visible”, Airio says.
“We need a strong user-based viewpoint, as users’ expectations are rising.”
Designing our way to better safety
Valmet's paper machine designs take a proactive approach to fulfilling the safety-at-work requirements of the European Machinery Directive and various other standards around the world. “The OptiConcept M walkways were the first in the world that really met the end-user needs and fulfilled all safety standards,” Airio says. “To meet the tightened standards, we are currently developing new, higher handrails, that are easy to lower and put back manually during maintenance without needing to remove the railing.”
Valmet also has a unified machine coloring system that is based on ergonomics. The human eye works so that lighter surfaces are prominent and darker surfaces tend to fade into the background. “In the coloring system, this means that the less-relevant process components are dark grey, and thus visually fade into the background, and we use lighter colors to highlight the significant process parts,” Airio explains.
“We are also working towards using safety color coding more coherently. For example, we think that yellow is the safety color that should be used only to show the dangerous areas and the moving parts, not on the safety fence,” she explains.
The future is human
Most of the new UX developments happen first in the consumer market, but the emphasis on user experience in the business-to-business market is growing. “It’s easy and intuitive for users to adopt new conventions that they are already familiar with from consumer products. Maybe one day we’ll be able to operate a paper machine with hand and voice gestures,” Airio suggests.
In the future, it will not be enough that the machine works and it’s possible to perform maintenance actions on it. “We need a strong user-based viewpoint, as users’ expectations are rising. It’s not enough anymore for things to be possible – they need to be easy as well. It’s not enough for a product just to meet the safety standards, because it’s not the same thing as feeling like you are using a safe product.”
Digitalization is changing the traditional machine–operator interaction. “It is interesting to think about how the machine itself should change when there are advanced applications to help users. Data and multiple apps that need the user’s attention can be a burden,” Airio points out.
The UX can bring clarity and simplicity to that complexity. “Could lights be used to point out places that need maintenance? Could we highlight the machine operators’ checkpoints during regular rounds with lights? Or it could be something we haven’t even recognized yet.” Airio says that the main tool of a UX designer is empathy. “You need to be able to walk a mile in the user’s shoes, to listen and observe and understand their pains and gains when designing the future solutions”.
Related articles