Web Monitoring System guides further board machine improvement
In order improve runnability on its PM3 board machine, AB Grigeo Klaipėda in Lithuania recently installed a Valmet IQ Web Monitoring System (IQ WMS) to discover more about the origins and causes of web breaks.
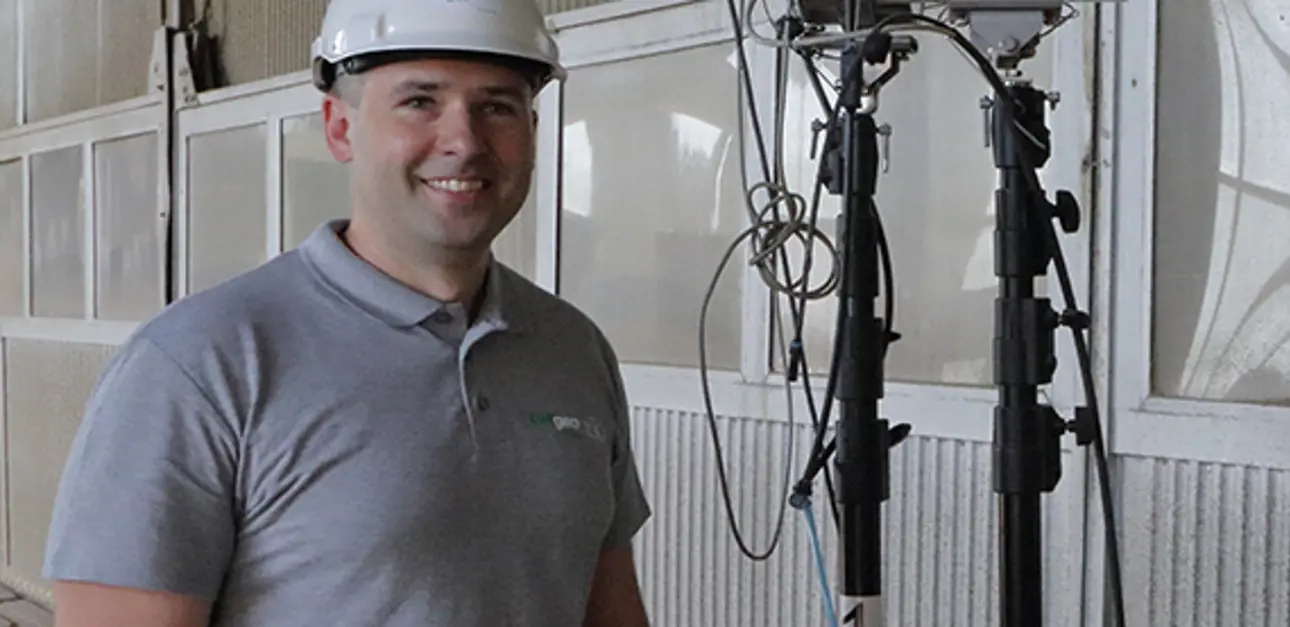
AB Grigeo Klaipėda in the Lithuanian coastal town of Klaipėda was founded in 1898 and is one of the oldest companies in Lithuania. The mill produces raw material for production of corrugated cardboard – testliner (used for outer plies of corrugated board) and fluting for corrugated boards as well as cardboard paper honeycomb from a 100%, mainly OCC, recycled furnish. Main grades produced on the two layer machine are between 90 and 140 gsm.
Improving runnability
As part of continued investment on the machine to improve product quality and productivity the forming section was rebuilt in 2016 together with the installation of a silent drive system in the dryer section. Upgrades to the Valmet distributed control and quality control systems were also done at this time. As well as improved quality an increase of 20% in machine speed was also achieved. Vidas Beržonskis, Managing Director, takes up the story, “Our next target was runnability. One of the problems we faced were increased breaks in the drying section, part of the reason was of course the increased speed but we also faced dust problems, stickies and some dirt as well. We knew they affected breaks but had no proof. So finding the reasons behind the breaks became a priority and we decided to install a web break camera system.”
Making the right choice
![]() |
![]() |
“The camera system has enabled the next step of our investment plans,” says Vidas Beržonskis , Managing Director. | “We saw how easily the operators used the system,” says Paulius Sereikis, Technical Director |
The Valmet IQ Web Monitoring System was top of the list, “Technically, the systems we looked at were very similar but the operator interface to the Valmet system was easily superior, as well as the easy integration tothe existing Valmet DNA DCS and Valmet IQ QCS on the machine,” says Beržonskis.
A visit to a Finnish reference installation sealed the deal, “We saw how easily the operators used the system and when Valmet offered newer and more compact camera designs with separate high power light sources we were convinced that it was the right choice,” says Paulius Sereikis, Technical Director. A total of 14 cameras were installed from the press section to size press with flexibility added by two moveable cameras that can be setup to monitor other areas on the machine. Startup was made in October 2017. “We worked very well with Valmet through the design phase and implementation. We have had good experience with the existing Valmet systems and now we are able to focus to important areas“, says Paulius Sereikis.
Easy to use
Irmantas Zubrus, Head of the Technology Group, is similarly impressed, “We can look at the break from 22 seconds before it occurred to 8 seconds afterwards, synchronized for all the cameras, so we can follow a problem through the machine as it develops. Now we see exactly what has happened on the paper and where it started. By knowing the reasons behind a break we have been able to find some good solutions, whether it involves stock preparation or changes on the machine,” he says. “The interface is so easy to use, very user friendly and intuitive. The time cursor for multiple video clips is easily dragged with the mouse and the high resolution video makes it easy to see areas of interest. We can now have a history of particular problems and can analyze further when necessary.”
Guiding further improvements
For Vidas Beržonskis the Valmet IQ Web Monitoring System has been a great success and is guiding the mill to future improvements. “We have probably found the reasons behind 75% of the breaks and the camera system has enabled the next step of our investment plans to reduce the problem. When breaks occur at the same area and in the same location, we can actually see what caused the problem. This may mean we stop the machine to clean the wire or dryer fabrics and thus avoid another break. Now we have ordered a dryer fabric cleaning system from Valmet that will be installed during our August 2018 shutdown to reduce the problems caused by dust and stickies. The main proof that this would be a good investment was the break camera system. With no more guessing, we are very confident now with the decision for the fabric cleaning system.”
The easy to use interface requires virtually no training to use although Irmantas Zubrus says that correctly interpreting the pictures requires more experience.
Irmantas Zubrus, Head of the Technology Group pictured here with one of the two mobile cameras at the dryer section.
Related articles