Continued investment in the best technology
The Heinola Fluting Mill is part of the Stora Enso Renewable Packaging business unit. The integrated mill consists of a power plant, pulp and paper mill, which has been producing high-quality corrugated board since 1961. The products are mainly exported to customers manufacturing strong and durable boxes for fruit and vegetable packaging. Continuous investment in best available technologies has been a key factor in maintaining the mill’s reputation as one of the world’s best and most productive semi-chemical fluting manufacturers.
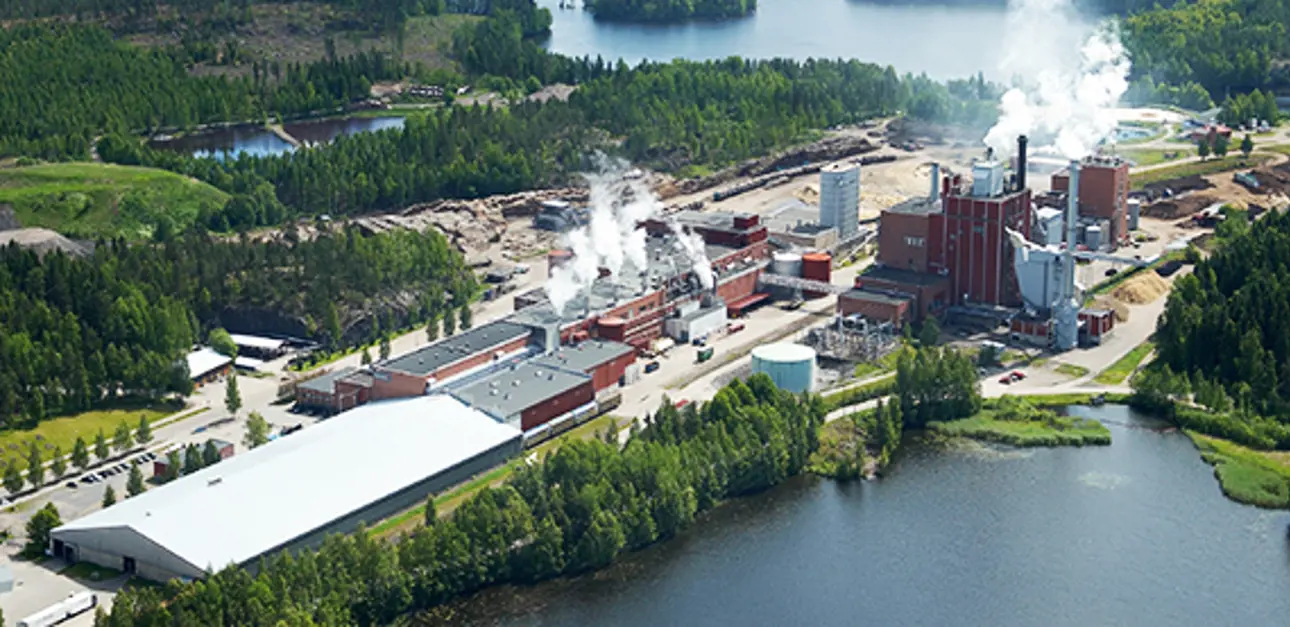
Environmental friendliness guides operations
As regards protection of the environment, the pulp and paper industry is one the most closely regulated and monitored industries in the world. Operating permits that govern the maximum allowable emissions are fully defined and enforced on a regular basis. The permissible limits usually require application of the best available technology (BAT) in manufacturing processes as well as in the recovery of substances harmful to the environment. The latter is an important part of mill operations to minimize environmental impact. For Heinola mill operations manager, Timo Riuttanen, the goal is to be the safest, healthiest and most productive mill, as well as quality leader in many markets and selected end-uses.
Even the best process technology will not work properly without modern and reliable measurement and control systems. Valmet Automation has developed new measurement technologies for process applications where real-time measurements of process variables were earlier impossible. Controlling the process with continuous measurements is the only way to minimize any negative environmental effects.
Measuring eco-effect
To increase the effectiveness of process control, one of the most recent investments has been in measurement equipment from Valmet Automation to continuously measure the very low levels of suspended solids. Of special focus was the wastewater treatment sludge drying with the need to optimize polymer chemical dosage to the centrifuge, and from time to time also the ferric sulfate amount added to improve drying.
To measure the dry solids concentration of sludge fed to the centrifuge, a Valmet TS (Total Solids Transmitter) was installed together with a Valmet LS (Low Solids Transmitter) to monitor the solids content of the filtrate exiting the centrifuge. Incoming solids content to the centrifuge is about 2% with solids content of the filtrate ranging between 200–1500 mg / liter. According to Riuttanen, both of these solids contents could previously be reliably monitored only with laboratory tests, which were conducted once a day.
Measurement operating principles
The Valmet TS measures the time-of-flight of a microwave signal through the flowing slurry without any moving parts. The signal propagation time is dependent upon permittivity, i.e., how the slurry influences the electric field. For organic substances, this is practically constant, while the permittivity of water is considerably different. Using this difference, the solids content in the flow-through measuring chamber can be accurately calculated.
The Valmet LS measurement is based on LED and laser technology. The device has two light sources, as the light passes through the fluid, the absorption, scattering and depolarization of both light sources is measured. The method allows the measurement of very low solids contents. Using a sample flow system, air bubbles and debris are filtered to have no detrimental effect on the measurement, and automatic flushing cleans the sample line and optics on a regular basis.
![]() |
![]() |
|
Valmet Total Solids transmitter | Valmet Low Solids transmitter |
Results
The newly installed measuring devices make it possible to run a smoother suspended solids load at the centrifuge. This is in itself a beneficial effect on the centrifuge operation, as well as sludge mass management. Polymer dosage is now controlled in relation to suspended solids load based on the solids content of the centrifuge reject water. It is thus possible to obtain a better degree of separation and minimize the internal circulation of suspended solids.
Riuttanen comments that the Valmet LS indicates immediately if the solids content of the centrifuge reject water is increasing. The system continuously measures the amount of solids in the reject water and the air volume index, which indicates a possible overdose of polymer. Too high a solids content in the reject water leads to a large suspended solids circulation and needs retreatment through the plant. “Corrective measures can be done immediately to keep the filtrate clean. The wastewater plant permits mill operation, and the internal load is very important to the operation of the wastewater treatment plant,” says Riuttanen.
When asked whether the equipment performance has met expectations, Timo Riuttanen replied, “Wastewater is a very challenging environment for measurement cleanliness and, through good cooperation with the supplier, reliability is at a high level. Polymer dosage is now under accurate control and overdosage is avoided. Similarly, the centrifuge filtrate purity is better than before. Compared with laboratory measurements, it can be said that the devices provide reliable information.
For more information: Heli Karaila
heli.karaila @ valmet.com
Product and company names changed from Metso to Valmet. Valmet acquired Metso’s Process Automation System business and products on April 1st 2015.
Related articles