You cannot copy know-how and experience - Valmet’s filter fabrics for various processes since 1965
Valmet supplies filter fabrics for the mining, chemical, pulp and paper industries, for sewage treatment plants, energy production, food manufacturing industry, and for the building materials industry. An increasing percentage of our solutions go to filtration applications which use or serve environmental technology and contribute to reach sustainability targets. This article focuses on filter fabrics for mining.
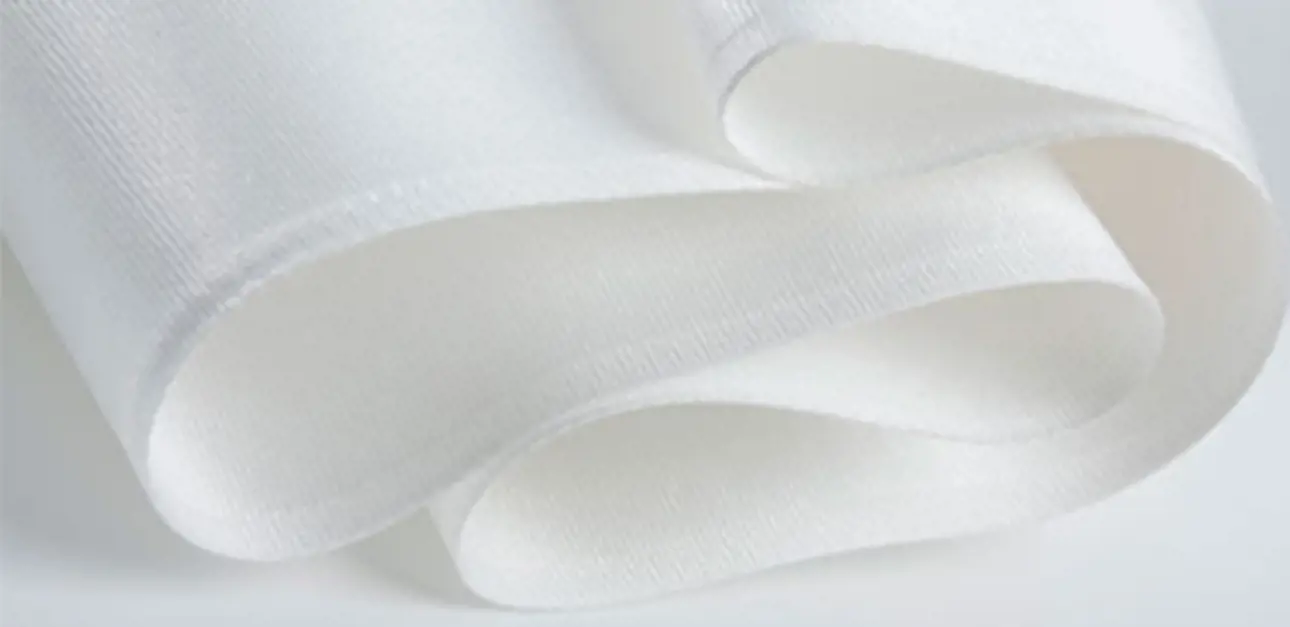
Valmet’s filter fabrics have been on the market since 1965, first with the brand name Tamfelt, followed by Metso and today they are an integral part of Valmet’s product portfolio.
“A filter fabric supplier must be innovative, flexible and owe strong filter and filtration process know-how. Application competence is a must to be able to deliver added value to customers. It is our responsibility as a market leader to find the right fabric solution for each filter application,” states Torsti Lähteenkorva, Senior Manager, Mining and Chemical, Filtration at Valmet and continues, “This is where we are strong. You simply cannot copy know-how and experience.”
The range of Valmet’s filter fabrics is the most extensive on the market and includes fabrics for tower press filters, belt filters, press filters, horizontal vacuum belt filters, drum filters, just to name a few applications.
Valmet Filter Fabrics well-known around the world
“During the past 50 years we have delivered filter fabrics to more than 100 countries around the world and. For example, Valmet Tower Press Fabrics are delivered to all world-leading copper, zinc and lead mines and many times we are their sole filter cloth supplier for tower presses. This shows that the global mining industry relies on us and our products,” Lähteenkorva points out.
Filter fabrics for tailings high on the agenda
Mine tailings are a challenge we face all over the world. The handling and reprocessing of tailings call for efficient filtration to support the mines to achieve dry tailings and meet environmental requirements. Valmet is continuously developing its filter fabric portfolio for tailings. Already with the existing fabrics it has gained a firm foothold on the market.
Filter fabrics for the fertilizer industry, too
To meet the food and energy demands of a growing world population, sustainable agriculture will continue to require mineral fertilizers. Today, these products need a low carbon footprint to reduce their environmental impact. Valmet has developed a wide range of filter fabrics for the fertilizer industry’s highly demanding applications, especially for phosphate rock washing, phosphoric acid and potash production.
Adding to sustainability in alumina production
As alumina production is one of the most significant users of filtration and separation technology globally, it’s also one of the areas where the right choice of filter fabrics makes a big difference to the production process and the end result in terms of sustainability. “Recently we received a very important order from a red mud residue dewatering plant in Asia Pacific,” Lähteenkorva says.
Each fabric is tailor-made
“The filter fabric is at the heart of the filter. It does the main work in producing a clear filtrate and a cake with a low moisture content. Only an optimal fabric that matches the customer's requirements is able to yield the best filtration result, both technically and economically,” Lähteenkorva points out.
Every filter is different, so each filter fabric is tailored according to specific needs, starting at the very first test filtration. During the life cycle of the filter, the fabrics are fine-tuned based on laboratory samples taken from filter cloths removed from operation. Our analysis reveals the wear and blinding level of each fabric, and this information is used in defining just the optimal fabric structure for the customer’s filtration process. Also, new innovative fabrics are being developed based on the findings.
Smart monitoring of cloths
Today, Valmet also provides Industrial Internet solutions for filter cloth performance optimization. By gathering information, the performance of filter cloths and filters can be analyzed and monitored, also remotely. Customers and Valmet experts can utilize the information on cloth lifetimes, the reasons for cloth removal and cloth consumption to optimize the whole filtration process. This information also helps to better operate the filter itself.
Good cooperation is key
“During the decades years that we have worked closely with our customers we have created a large data bank of slurry details, particle distribution, density, slurry pH etc. connected to several tests conducted with our different filer clothes,” explains Lähteenkorva and goes on, “We are always happy to share this information to new employees at our existing customers. We have also been asked for training regarding filtration media and these training courses have been very fruitful for both our customers and us. It’s important that the information goes both ways.”
“In addition to good cake release, long filter cloth lifetime and reliable performance, good cooperation with the customers is of utmost importance. We are committed to moving our customers filtration performance forward. The fabric recommendations we give are not our best guesses but are based on technical measurements, accurate follow-up of cloth performance and on fifty years’ experience. As we say you cannot copy know-how and experience,” Lähteenkorva summarizes.