Wear protection is no-longer skin deep – the beauty of eliminating erosion start from the inside
We at Valmet Flow Control business line (formal Neles) know that the smallest of things can result in some of the biggest issues. Issues that can result in considerable unplanned costs for any industrial process. This is particularly true in processes involving valves and pipes. In these applications the small things are often minute particles resulting in wear. Whether we are talking about erosion, corrosion or abrasion, the effects and costs can quickly mount up without the right flow control solutions.
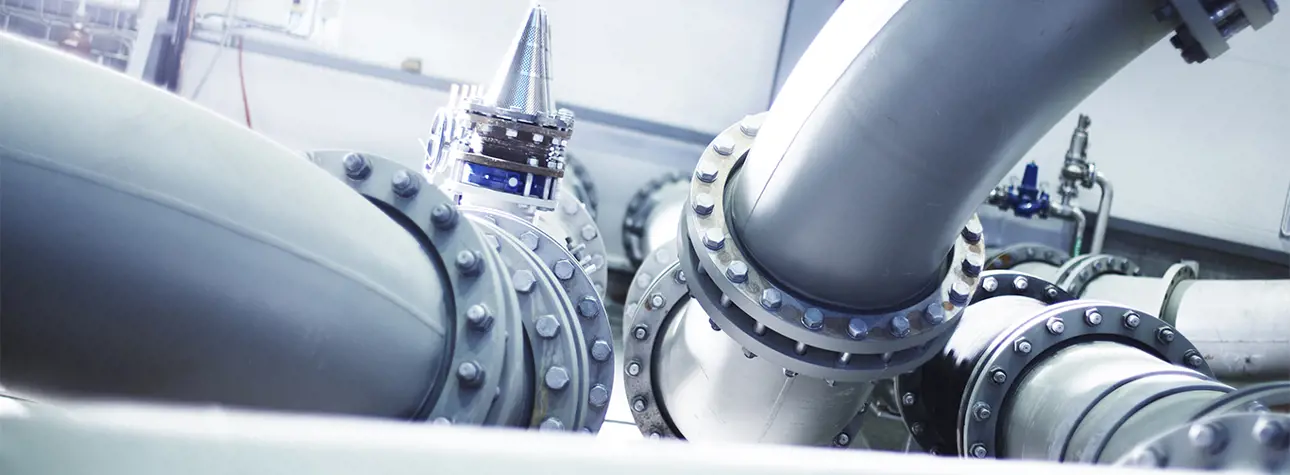
Wear is a potential issue wherever media flows through valves and pipelines. Wear doesn’t discriminate between flowing liquid or gasses, and it is an equal challenge in physically demanding and rough mining environments as it is in precision-requiring refining processes. The wear of process equipment is also a major issue in power generation processes as well as in autoclaves in hydrometallurgy – simply whenever a medium carries erosive or abrasive particles either intentionally or as unwanted impurities.
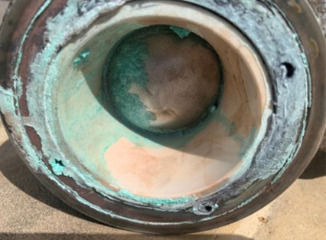
Life insurance for your valves
The effects of wear on the inner surfaces of valves and pipes can be, and often are, extremely expensive. The engineers at Valmet Flow Control however feel that in many cases these costly effects are completely unnecessary. The company’s unique WearBlock™ solutions can help improve reliability and improve uptime in erosive and abrasive applications. Imagine if you could minimize the risk of catastrophic valve failures and extend the lifecycle and replacement intervals for all the valves in your demanding processes. This is a vision that Neles could help you make into a reality.
Our unique WearBlock™ solutions can help improve reliability and improve uptime in erosive and abrasive applications.
We have to also remember that valves are intricate devices. Their functionality cannot be simply determined by saying that they work, or they don’t work. Ensuring that valves maintain their performance throughout their operating life is a matter of both efficiency and safety. Stability and durability of sealing surfaces are the key elements required for constant flow control performance and for the prevention of leakages and fugitive emissions. At the same time, wearing out of pressure retaining valve components can dramatically decrease operational safety. Such severe wear losses can be harmful to not only production output, but to health and safety at your plant and even in surrounding areas.
Proven materials and techniques
Valmet Flow Control business line (formal Neles) has actively developed materials and techniques for wear protection for well over 25 years. Some of these unique techniques for improving wear life have first been introduced in our heavy-duty mining equipment. Having proven themselves in these extreme conditions, these new materials and constructions were brought into valve design. The first valves utilizing our metal matrix composite materials and bi-metal construction were delivered and commissioned more than 5 years ago. Considering the fierce operating conditions of these first valves, it is a very positive outcome that a large number of those devices are still in working order and active service today.
These proven materials and valve construction techniques are applicable in most types of valves. Upgrading your valves to Neles valves with enhanced wear performance can increase not only reliability and durability, but also the effective lifetime of your valves in severe service applications where erosion is an issue. While even we can’t yet make a valve that would last forever, they can help select the right valves that are optimized to achieve the best possible performance in your specific applications and environments.
Tailored performance
Your valve performance can be tailored to align with your service and maintenance strategy. Depending on the process and the service schedule for other process equipment, a valve may be required to work for just weeks or months at a time, or for numerous years. Balancing out process requirements, planned maintenance schedules and lifecycle costs, Valmet can help you select the valve solutions that work best for you. Pairing your valves with our smart devices you can monitor valve condition and performance in real time, allowing for well-planned maintenance and service operations without any nasty surprises.
Protection beyond the ordinary
The upgrades that Valmet brings to the table regarding materials and techniques takes wear protection beyond what most valve manufacturers offer today. The WearBlock™ bi-metal valves utilize advanced powder metallurgy to bind together standardized valve construction materials and unique wear protection materials covering the wear exposed surfaces inside the valves.
These robust constructions allow increased thickness of wear protection material, and there are no open seams or welds, or other points of discontinuity, which are known failure risk areas in traditional wear protection solutions. Performance is built into these valves, so that you don’t have to worry about the integrity of the construction. And, just think how a valve’s useful lifetime changes, as the wear resistance of materials is multiplied in comparison to traditional weld-clad materials. Also, this new material can be applied as a much thicker layer, leading to a longer lifetime than was possible with earlier technologies.
Performance is built into these valves, so that you don’t have to worry about the integrity of the construction.
Metal matrix composite (MMC) materials are another key innovation in the field of wear protection. Ceramics have long been used as a protective lining inside valves, and in many challenging wear applications our ceramic valves offer the best performance available. Still we must accept that monolithic ceramics have their inherent limitations, such as hydrothermal degradation, limited resistance to thermal shocks and lack of electrical conductivity. The superior hardness of ceramics and the toughness of metals are incorporated into our metal matrix composite materials, which thus offer the best combination of wear resistance and mechanical reliability. The MMC materials are available in WearBlock™ bi-metal valves, but also as an option (hybrid-E) for ceramic insert parts in our ceramic ball valves.
A solution for many demanding industries
As mentioned earlier, the mining industry has been the testing ground for many different wear protection solutions over the years. The processes involved are extremely demanding on machinery and devices, and so are the ore beneficiation processes following the excavation and comminution steps. One of the metal refining applications in which WearBlock™ ball valves have proven their performance is metal leaching in autoclaves. In a typical case the solids of the process solution sediment on the trim and the seat of a valve, and consequently the force needed for moving these jammed closing members during the valve operation becomes higher than the materials can tolerate without breaking. In this type of service, the hybrid-E ball valves assembled with MMC parts have helped overcome the reliability challenges seen in conventional valves equipped with fully ceramic or ceramic coated closing members. These hydrometallurgy processes can be continuous or of the batch type, but in both cases the benefits of increased reliability and extended lifetime of valves are critical for the output of the process.
Power generation processes can also enjoy significant extensions in valve lifetime with valves using the unique bi-metal construction and metal matrix composites (MMC). Erosion protection in syngas scrubbers is an area where some of the greatest results have been reported. Heavy erosion was reported by a customer in areas dealing with aqueous coke particle slurry, which led to valves being replaced every 6 to 12 months. WearBlock™ valves with MMC on the wear surfaces are now in their sixth year of operation, and only showing minimal wear. Reaching a target of 6 years between replacement instead of 6 months is a huge improvement and has brought significant economic savings for the customer in question.
In oil refineries, catalyst fines are a notorious cause for erosion. In FCC units (fluid catalytic cracking), the blow-out of catalyst fines is capable of puncturing unprotected valve bodies. A refinery reported their original steel valve bodies failing every 1-3 months, which is why they turned to Neles. In the very same operating environment Valmet's valves equipped with WearBlock™ features have reached a valve lifetime of 25 months. At the 6-month point, which was already double the operating life of the old valves, the bi-metal surface of the valves looked as good as new and the dimensions had remained completely unchanged.
It pays to be careful
Every service operation in itself is a major undertaking, which includes plenty of preparation. It involves minimizing the loss of production output during the downtime, but it also entails extremely careful planning in terms of HSE considerations. Regardless of how well a shutdown is planned, it is always a risky time on any site. So, by being able to extend the interval between valve maintenance and replacement from a matter of weeks to months, you could avoid a significant share of annual risk situations. These types of extensions in valve lifecycles have already been achieved with the valves with WearBlock™ features.
And as the case often is, the maintenance cost of one single valve can be thousands of euros a time, just think of the possible cost savings across your entire plant. Good planning and the selection of the most optimal valve solutions makes a great deal of economic sense. And these are just ballpark numbers that don’t take into consideration the possible costs and risks involved with an unplanned shutdown resulting from a failing valve. Just consider that a catastrophic valve failure could cost an oil refinery an entire day’s production output, which could be tens or hundreds of thousands of barrels. Certainly not an acceptable price to pay for saving on wear protection.
Text originally published in 2018, and slightly updated in April 2022, due to the company name change to Valmet.

Jussi Hellman
Materials Engineering Manager, Valve technologies
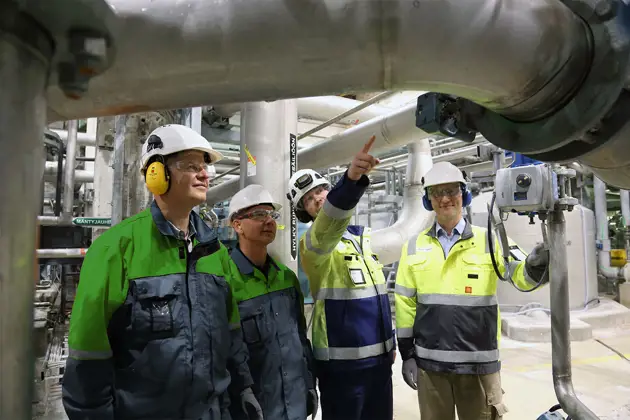
Subscribe to our newsletter
Subscribe now to flow control newsletter and receive the latest insights directly to your email.
SubscribeRead more