Small decisions, big significance
Industrial gas processes are known to have high requirements on absolute gas production plant availability. Maximal availability is possible by having reliable components. As industrial gas processes are highly dependent on valve operations, valves play a critical role in the availability of most industrial gas process plants. Pressure or vacuum swing adsorption (PSA and VSA, respectively), as well as air separation (ASU), all depend on reliable valve operations to secure the constant supply of industrial gases, such as hydrogen, oxygen or nitrogen, to the wide variety of processes requiring these gases.
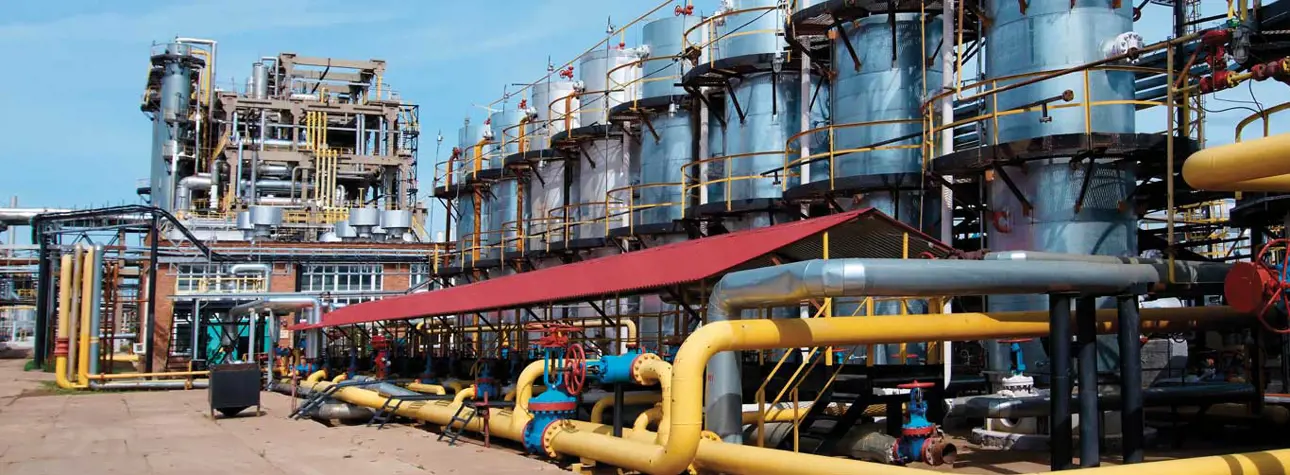
Industrial gas process essentials
The most critical challenge regarding industrial gas production is ensuring reliability and the subsequent availability of industrial gases in processes needing the supply. In practice, this means maximising uptime and a continuous, uninterrupted supply of gases. At the same time, profitability is an important parameter. Industrial gases are used in diverse industries, in particular, in capital intensive processes, such as refineries and the chemical industry. Therefore, the availability of industrial gases plays a crucial role in helping upgrade the raw materials into valuable end products. Without consistent availability, significant losses result because the processes would experience disturbances or even unplanned downtime.
- Highlights:
- In this article you will learn about the solutions Valmet has developed to assist industrial gas producers.
- Producers need solutions that ensure availability of industrial gases in processes requiring their supply, while maintaining profitability and minimizing environmental impact.
- Valmet's vast experience in the industrial gas production field has led to a number of innovations.
- Innovative valve design along with complimentary solutions provides efficiency, uptime, easy maintenance and control.
Industrial gas processes can be divided into three categories: membrane technologies, swing adsorption technologies, and air separation technologies. These technologies have a lot in common from a product specification point of view, but they differ a lot in terms of production scale. Whereas air separation technologies are used in large scale production, swing adsorption and, in particular, membrane technologies provide less output. Air separation technologies are able to produce several industrial gases at the same time. This differs from swing adsorption and membrane technologies, where the gas plant is always built for one specific end product only. Moreover, ASU only separates air gases, whereas PSA/VSA and membrane technologies can be used to purify feed gases, such as syngas, biogas and oxygen/hydrogen/nitrogen rich gases from various impurities, such as CO2, carbon monoxide and, hydrogen sulfide. Membrane technologies can also remove water from feed gas. Still, membrane technologies are typically not as effective as the other methods at producing all the industrial gases mentioned above, and typically, the maximum purity of the end product is not as high as with PSA or ASU processes.
Membrane processes
Membrane technology is most suitable for producing low to mid volume industrial gas with purity le vels of approximately 95% or lower. The technology is based on the use of partially permeable membranes, which selectively allow gases to pass through the membrane while others are left in the basic gas str eam. Over the past 10 years, the membrane gas separation technology has advanced greatly and is now regarded as a competitive industrial gas separation method. Most often, membranes are used in nitrogen production to remove moisture and hydrogen from the source gas. When compared with PSA technologies, the benefits of membrane technologies include a lower capital investment and simpler construction. Another benefit of the technology is that it requires less space. Additionally, a membrane gas plant is e asier to run at partial capacity. Typically when using membrane technologies, the operating costs are low, as it is an ambient temperature process, which requires hardly any labour during normal operation.
Swing adsorption processes
Swing adsorption processes, which typically separate or purify gases in normal room temperature or mildly elevated temperature conditions, include three different main adsorption processes based on either pressure alternation (PSA/VSA) or temperature alternation (TSA, temperature adsorption). These processes are used to purify gases from a mixture of gases under pressure or temperature. The source gas is fed into tanks consisting of adsorbent material, which adsorbs the impurities of the inlet gas and allows the separated end product gas (hydrogen, nitrogen, oxygen) to flow through. As a batch process, it is highly cyclic with continuous and frequent switching between adsorption and desorption, which is the regeneration of the adsorbent.
Adsorption cycles in the process are typically fast with even 2 - 4 cycles/min and the operating time for valves is limited to even less than 1 s per operation. This sequence is then repeated over and over again at a very precise pace in process trains consisting of 2 - 10 similar adsorption beds.
High-pressure differentials are typically present on both sides of the valve during the different process stages. Moreover, the valves need to be absolutely tight. In very extreme cases, the valves might see 1 million cycles/y, which is obviously challenging for any valve design. As gas producers typically have continuous supply contracts with their customers that involve substantial financial penalties for downtime, valves must have engineered high cycle characteristics to ensure long maintenance intervals between servicing to allow plants to maximize their efficiency. To meet these requirements, special valve designs must be employed. At Valmet Flow Control, R&D teams have been working together with industrial gas customers for many years. As a result, we have been able to develop widely accepted butterfly valve concepts under both the Mapag and Jamesbury brands for industrial gas.
"Industrial gas processes are known to have high requirements on absolute gas production plant availability. Maximal availability is possible by having reliable components".
With the newest generation, Neles is now setting new standards for valve performance. Neles™ high cycling butterfly valve, series BO will provide improved efficiency, especially in the higher pressure classes up to ASME class #600. This coincides with the movement of the industry in hydrogen PSA production. This new level of efficiency can be reached through unparalleled innovations within both valve internals and basic assembly. Controllability and maintainability have been improved, without compromising the renowned, best in class capacity of the valve. Intelligent valve controllers, such as Neles™ SwitchGuard (Figure 1), are often used in switching processes. The embedded intelligence makes it possible to see what is going on with the valve online and also to store the diagnostic data for later analysis. With the help of an asset management solution, such as Neles™ FieldCare, this information can be used to plan the maintenance to ensure the maximal availability of switching valves in the PSA process.
Figure 1. Intelligent valve controllers, such as Neles™ SwitchGuard (shown here on top of a Neles™ L6 butterfly valve), are often used in switching processes to secure reliable valve operations and to maximize the valve availability in PSA processes.
Air separation
The basic ASU process separates air into its primary components, end products being nitrogen, oxygen and rare noble gases like argon, helium, krypton or xenon. The most common technology in this separation process is cryogenic distillation. Although it may sound like a straightforward process, cryogenic distillation actually requires multiple stages of compression, purification, cooling and distillation before the end products can finally be shipped to the user. Furthermore, depending on the type of plant, the end product supply and storage must be considered. If the gases are to be directly consumed, no further liquefaction of the gases is needed. Air separation as a process is more economical when high volumes are needed since these plants typically have a non-linear cost scale relationship in plant operations. Naturally, these extreme conditions require a lot from process valves, and extra attention to the valve design is needed to secure reliability.
Extreme operational and environmental requirements, such as very cold temperatures and oxygen enriched atmospheres, are the major challenges. Especially in oxygen enriched flow media, the wrong material selection may compromise the safety of the plant. Additionally, these valves have to provide long lasting safe and tight shutoff to avoid health hazards and safeguard uninterrupted production to reach maximum availability of the industrial gas plant. In addition, they must provide stable control over fugitive emissions. Valmet has a long history with ASU valves, covering the entire ASU process from the compressor and purification stage through the distillation in the cold box to the tank loading and distribution. For the valves in the cold area (Figure 2) the cryogenic testing of valves provides accurate information on the valve performance.
Figure 2. A 20 inch valve after cryogenic tests according to BS6364 standard.
The experience in cryogenic and oxygen applications plays an important role in defining the most efficient and safe valve designs for each specific application in the ASU process. In Neles, oxygen valves have the material selection and design completed according to the BAM (Federal Institute for Materials Research and Testing in Germany, specialized among others in oxygen applications) and European Industrial Gases Association (EIGA) recommendations. The main shut-off and ESD valves in cryogenic air separation processes are practically always tested in cryogenic temperatures to secure the tightness properties in actual use conditions. The testing is usually performed according to international standards, such as BS6364, or customer specific standards. At Neles, this testing is done in house in the cryogenic facilities available in Finland, Germany and the US. Finally, unlike in PSA, the ASU process contains many different process stages. Thus, in ASU, the optimal plant operation also includes an effective automation system to help optimize the total process. It also helps operators not only to control the process, but also to get relevant maintenance data through integrated condition monitoring, as is the case with Neles’ own DNA automation system.
Conclusion
As stated above, common to all cryogenic and non-cryogenic industrial gas processes is the requirement for reliability and efficiency in plant operations to provide a constant supply of industrial gas to the end process. Reliability and efficiency rarely come from a single source, but are created by multiple smaller aggregates. Smaller decisions, beginning from the design phase to the operational decisions, define how well the plant will perform. In practice, this is the reason why according to Neles, the best performance from industrial gas plants is not delivered by only using best in class and reliable valves, but by combining the reliable valve solutions directly with the effective maintenance planning of the whole plant. Preferably, the valve solutions should be combined directly to the plant automation system level, which can provide even more detailed information regarding effective maintenance planning to maximise the plant availability, even in the long run.
Hydrocarbon Engineering, June 2014. Text by Mikko Vuolanto. For additional information, please contact joshua.ruiz@valmet.com
Text originally published in 2014, and slightly updated in April 2022, due to the company name change to Valmet.
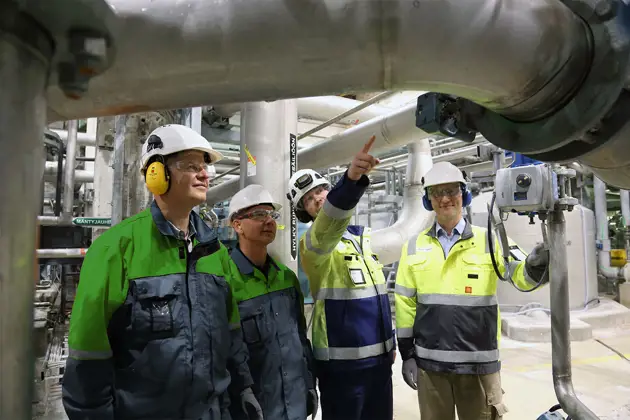
Subscribe to our newsletter
Subscribe now to flow control newsletter and receive the latest insights directly to your email.
SubscribeRead more