GSPP PM3 - sustainable containerboard production in Malaysia
In 2021, GS Paperboard & Packaging (GSPP) started up their PM 3 board machine at their Selangor site in Malaysia. It produces testliner grades from 100 percent recycled raw material and is equipped with the most modern Valmet-supplied papermaking technology.
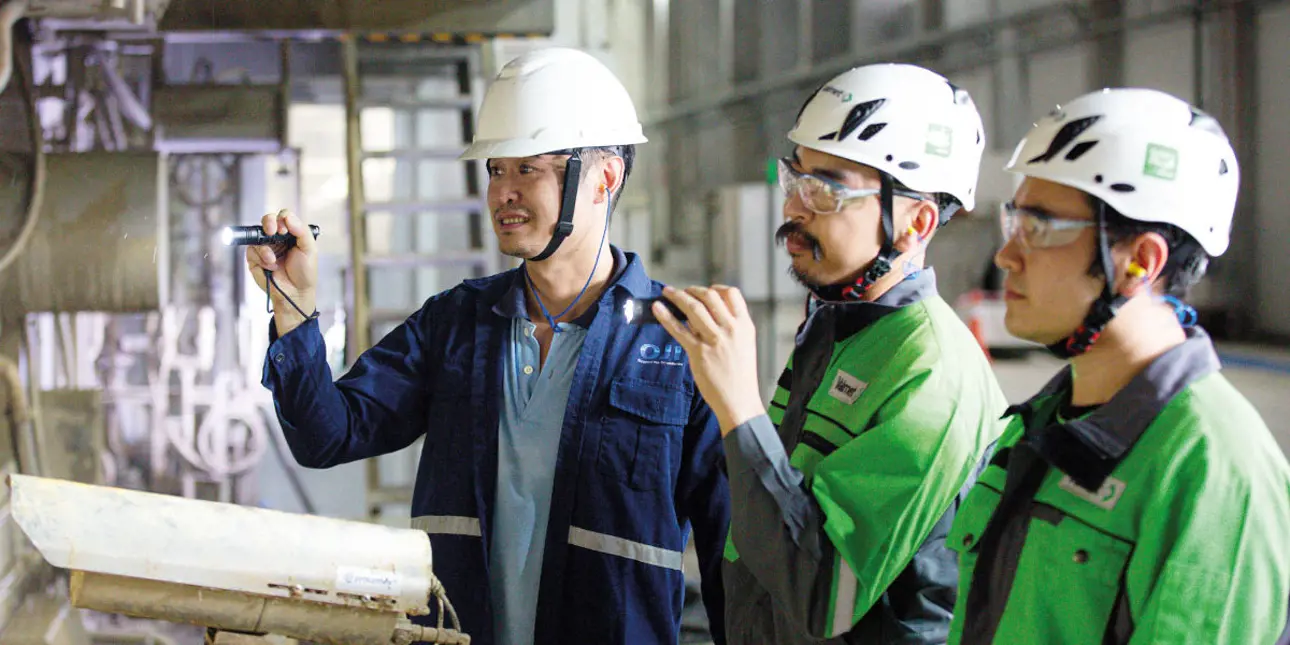
GSPP is a member of Oji Group, one of Malaysia’s largest integrated paper and packaging manufacturers. They continuously improve and develop superior products that meet international standards. “The main drivers for the PM 3 investment were the ability to produce lightweight grades and to further increase the mill’s capacity,” says Ng Chuan Teik, Production Manager of PM 3 at GSPP. GSPP produces extremely flexible corrugated packaging material for the manufacturing of innovative board boxes with a wide range of printing options. According to Kenichi Morishita, Technical Manager at GSPP, a major challenge for papermakers is to produce lightweight grades at high speed, which is one of the most important features of PM 3.
GSPP develops superior products that meet international standards. The PM 3 produces high-quality, lightweight testliner grades with high energy and raw material efficiency.
Ng Chuan Teik continues, “The most beneficial feature of PM 3 is its energy and raw material efficiency, because we produce lightweight products, and its machine safety, which greatly contributes to our operators’ daily work. We also achieve high end-product quality from PM 3.”
Process technologies, automation and clothing from the same supplier
“We need partners that can provide us with solutions to remain competitive, now and in the future,” says Ng Chuan Teik. “We chose Valmet as our main supplier for the PM 3 investment because of its many references from across the world, with all the latest technologies. And of course, the wide range of specialist support available from Valmet was another important factor in our choice.”
Valmet’s delivery included solutions from the broke and approach flow systems to a complete OptiConcept M containerboard machine and the winder. The automation delivery included a Valmet DNA Automation System for process and machine controls and a Valmet IQ Quality Management Solution. A paper machine clothing package was also delivered for the start-up.
“The main drivers for the PM 3 investment were the ability to produce lightweight grades and further increase the mill’s capacity,” says Ng Chuan Teik, Production Manager of PM 3 (right) and Kenichi Morishita, Technical Manager of GSPP (left).
“Valmet was the main supplier of the process technologies, automation and clothing. As we all know, it isn’t easy when you start up a paper machine with a lot of vendors. In the PM 3 project, we got all the expertise from one key supplier, Valmet, with all their specialist support. This was one of the key reasons we were able to start up the machine successfully,” says Ng Chuan Teik in summarizing the project.
The modern Valmet DNA automation platform makes it easy for operators to use and monitor the system.
Value from industry leading automation and Industrial Internet solutions
“The high level of automation played a fundamental role in enabling us to have a smooth start-up, with smooth operation and opportunities for further optimization. We have a single automation system that provides controls for the machine, quality and process. This makes it easier for operators to use the automation system and monitor it,” says Kenichi Morishita.
In the PM 3 project, we got all the expertise from one key supplier: Valmet.
Valmet can provide data-driven Industrial Internet applications with remote connections to their customers worldwide. PM 3 also benefits from these solutions. “Valmet Industrial Internet applications like the Dynamic Centerline Advisor help us compare the current process with the best performance,” says Kenichi Morishita.
Successful start-up in one day
The start-up of the most modern board machine in Malaysia was smooth, and GSPP is very satisfied with the project. “The project has been successful. We faced a very harsh environment during the installation phase, when Covid-19 hit us hard. But with all the collaboration and support from our suppliers, we got through it and were able to commission this machine successfully, with paper on the reel on September 13, 2021. It’s quite a remarkable result to be able to start up the machine in a single day. Very shortly after that, we were able to produce sellable paper,” concludes Ng Chuan Teik.
Text  Marika Mattila