An ambitious project of grade conversion at Sappi Alfeld
The Sappi Alfeld Mill in Germany expanded into the market of specialty papers by rebuilding its one remaining graphic paper machine into specialty grades.
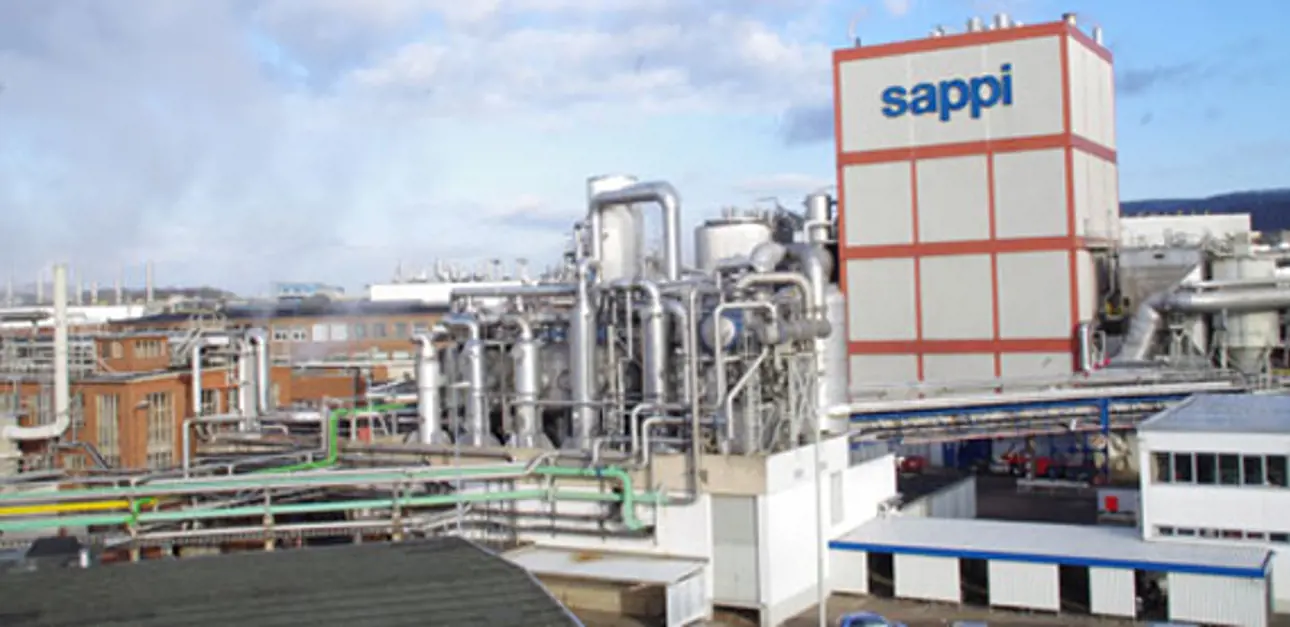
The Sappi Alfeld Mill near Hannover in Germany has been making paper since the 1700s. Over the last 80 years it has carved out something of a solid reputation in the field of speciality papers. Sappi recently took on an ambitious project to convert its one remaining graphic paper machine at Alfeld - PM 2 - into what is probably the largest, most innovative, automated and versatile speciality paper machine on the planet, with a capacity of 135,000 tonnes/yr. Sappi chose Valmet as a partner to help it achieve its goal.
Sappi is one of the world’s largest producers of high quality, coated graphic papers, but unfortunately – and no matter how good those products are - the introduction of the iPad, the Samsung Galaxy, the Kindle, and a raft of other electronic media devices have put a large dent in graphic paper demand.
At this crucial crossroads, Sappi could easily have introduced the unimaginative management philosophy of cut, cut and cut some more. However in the case of Sappi Fine Paper Europe’s Alfeld mill, a much bolder approach was taken; to significantly expand into the lucrative market for speciality papers.
“The existing PM 2 at Alfeld was losing us a lot of money”, says Sappi Fine Paper Europe CEO, Berry Wiersum. “And a graphic papers machine sitting in the middle of four other paper machines which were more than paying their way in specialities made no sense at all.”
Let Project Leopard commence!
The history of the idea for what was to become known at Sappi as Project Leopard started at the Alfeld mill itself. One of those people instrumental in the idea of the transformation of PM 2 is director at the Alfeld mill, Dr Stephan Karrer. “We had an unusual situation at Alfeld, four speciality machines that were doing really well in a growing market, and one graphic machine that was struggling in a declining market. We had to do something and we came up with the bold plan of going the whole way and doing a complete rebuild.”
The concept for the new PM 2 was for a world-class, prototype speciality machine with a width of 5,150 mm that could handle intricate grades from a basis weight of 40-180 g/m² and run at a production speed of 1,200 m/min. This would mean that production would leap from the five or six tonnes per hour norm for a speciality machine to 20 tonnes per hour. The machine would also have to cope with numerous, complex grade changes.
In July 2012, after a lot of serious studies, discussions and site visits, Project Leopard commenced, and Valmet was appointed as the main supplier for the project.
![]() |
![]() |
|
Director of the Alfeld mill, Dr Stephan Karrer, was instrumental in the idea of the transformation of PM 2. "It was the biggest experience of my life". | Wim Devens, the company’s manager of central technology and engineering, was Project Leopard’s leader from the Sappi side. |
Sappi Alfeld: A Challenging Customer Valmet’s scope of supply was a complex and all-encompassing one; the new PM 2 has a completely new headbox with dilution circulation, forming, press and dryer sections rebuilt. One of the essential ingredients in the rebuild is a brand new solid casting 6.4 m diameter Yankee cylinder with hood. The machine also has a completely new coating section with air dryers plus two OptiCoat Jet (prev. ValCoat) coating stations, a multinip calender rebuild with existing Nipco rolls, a reel rebuild and broke collection. The automation supplied also included a DNA quality control system and machine control PCS7.
Mauri Laurikainen, Valmet’s senior paper technology manager for paper mills says: “From the beginning when the concept was first presented, it was clear this was going to be an unusual one – a totally online concept with finished products coming off the end of the machine. Added, interesting challenges are the wide basis weight range and the differing speciality grades, at the same time being produced on a wide machine at speed. The Yankee cylinder of course was an absolute must to obtain the base paper surface quality.
“We trialled many of the grades at our pilot plants in Finland making sure that the coatings and calendering demands would work across the grades needed,” continues Laurikainen. “There is no doubt that the Sappi Alfeld mill was a demanding customer for this project, but they knew what they wanted and they always came at us with their ideas in a cooperative fashion.”
Showtime after the completed project. Customers and partners paid a visit to the machine during the inauguration on March 27, 2014.
A carnival atmosphere
Wim Devens, the company’s manager of central technology and engineering was Project Leopard’s leader from the Sappi side, he says: “We went through the whole process with the main suppliers, and in the end it came out that Valmet had the experience and know-how in specialities, as well as the facilities for the casting of the Yankee cylinder. There was also a gut feeling among the team at Sappi that Valmet was the right choice of supplier.”
With the order in place, it was then left to Devens and the project team, the mill team, and the suppliers to ensure the deadline for timing was met, as well as the guarantees of quality. But first, there was transportation of the massive Yankee cylinder to arrange.
The journey itself from Sweden to Germany by boat and barge was not so much of a problem, but the road trip from the river port to the mill was full of challenges, says Devens: “It took over 100 local authority approvals to allow the Yankee to pass through towns and villages and over bridges to the mill. Street lighting had to be dismantled, high voltage cables lifted and over 120 trees had to have branches sawn off – 10 trees had to come down completely.
When the Yankee finally arrived in Alfeld, it was to something of a carnival atmosphere as this was not only one of the most exciting projects the town of Alfeld had seen for some time, but it was also the biggest engineering project going on in the whole of Germany which was being hit by the economic turndown. Devens said, “When the Yankee arrived, it was as if the whole county had turned out to watch, people were out on the streets, and houses alongside the route were hosting barbecues and parties. We had a small viewing area in the woodyard, and on the first weekend something like 1500 visitors came to see the huge Yankee.”
The Yankee cylinder aroused a lot of interest along the roadside during its transportation to Alfeld and people gathered to see the huge equipment.
The race is on
On the 30th of August 2013 the ‘old’ PM 2 was shut down and the serious race to the finish began, there were only 39 days available for the installation of the Yankee and the rebuild.
Valmet gave the assurance that the project would take 39 days, and on October 12th 2013, exactly according to plan, there was stock on the wire. “We couldn’t quite believe it,” says Devens.
On the 17th October, and again absolutely according to plan, Alfeld produced the first two saleable jumbo reels. “It was part of the agreement with Valmet that we had to have two jumbo reels full of saleable paper to go out to our speciality customers,” adds Devens.
“We are really happy all in all with how it has gone and we have had splendid support from Valmet whenever we have needed it during the installation and start-up phase.”
“Biggest experience of my life”
Perhaps the most important person to finally ask about the success of the PM 2 project is mill director, Dr Stephan Karrer who originally came up with the concept: “Apart from the birth of my two children, this project really has been the biggest experience of my life. The last few months we have been optimizing the start-up and have been tiring for everybody, but it makes me so proud that the whole PM 2 team are still so delighted to be working on what is going to be such a remarkable machine when it is fully up to speed.”