Presteaming bin
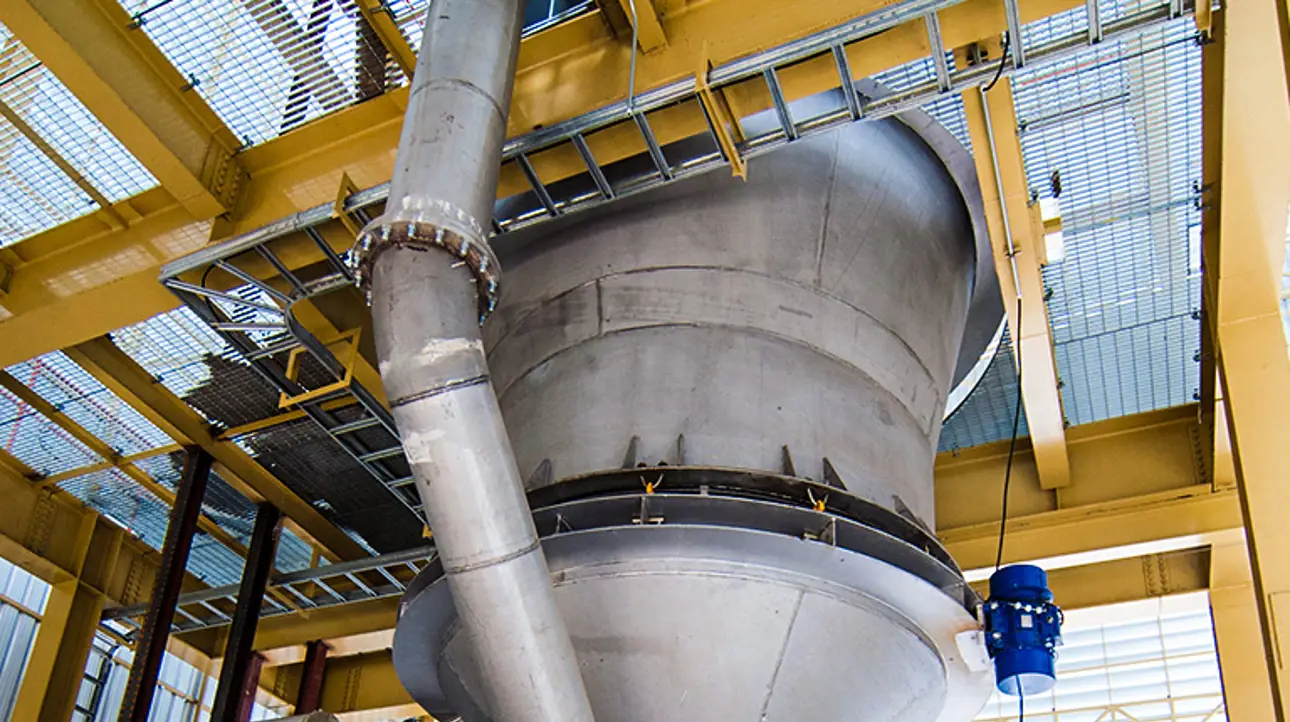
Presteaming softens the raw material before the screw feeder and makes it easier to compress, thus improving the dewatering capability and decreasing the wear of the screw feeder.
Moisture increase of the raw material
Reduction of natural wood resins
Improved dewatering in the screw feeder
The bin is of a hopper design and consists of a cylindrical and conical top section and a conical bottom section. The raw material enters the bin at the top and leaves through the conical bottom section.
In the conical bottom section a vibrating cone is inserted to help prevent bridging of the raw material in the bin. The preheated steam is introduced below this cone and distributed both in the middle and around the periphery of the bin where it meets the raw material passing down between the cone and the bin wall. The bin is designed for 15 to 20 minutes retention time.
Material available for download |
||
---|---|---|
Presteaming bin |
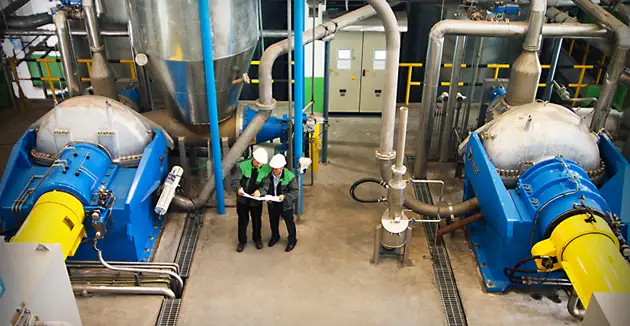
Our expertise is at your service
Our focus is to bring your performance forward. Get in touch with us through our website, or through your local Valmet office.
Contact us