Nippon Dynawave Packaging: new pulp drying and baling line increases flexibility
Nippon Dynawave Packaging’s (NDP) new pulp drying and baling line will increase the ability to shift economically between the available fiber while maximizing the current pulp production capacity. Despite the project’s challenging and exciting nature, it marks a new success in the long collaboration between Valmet and Nippon.
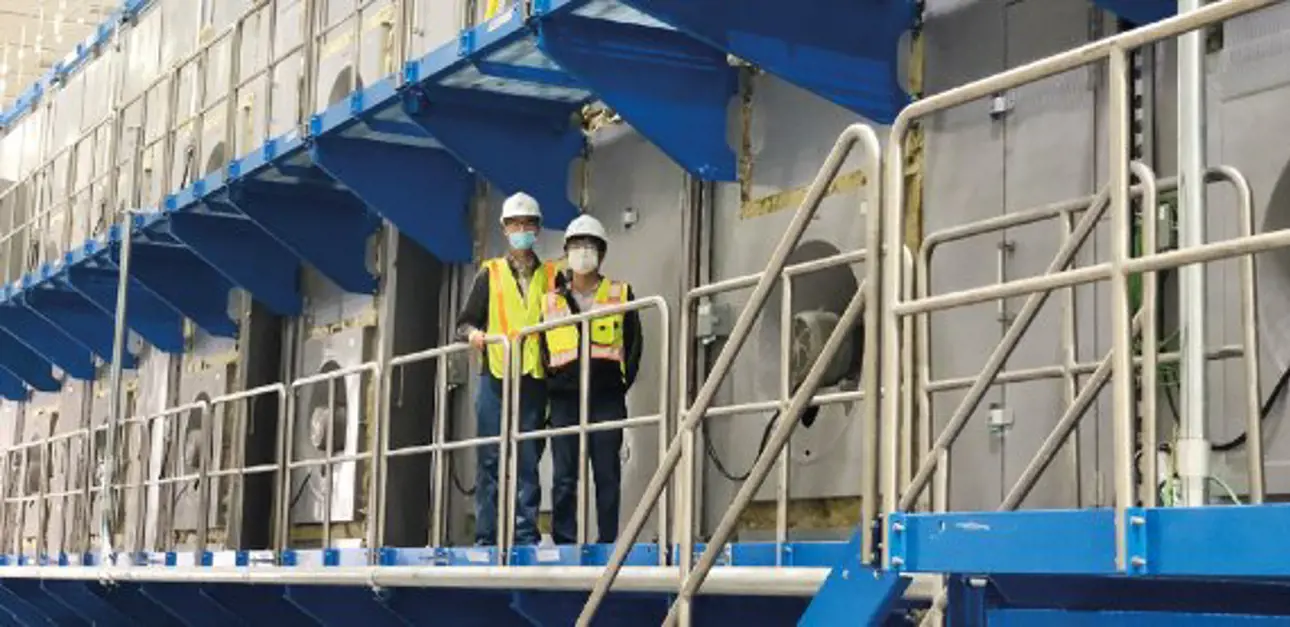
The NDP site in Washington, USA is a single-line facility producing liquid packaging board and market pulp in wet lap form. While the liquid packaging markets have remained largely stable, nonintegrated paper producers, the traditional customer base for wet lap market pulp, have decreased significantly in the Pacific Northwest. With a limited geographical range and declining customer base, there was a need for a product that could be shipped anywhere in the world. NDP therefore decided to invest in a new pulp drying and baling line and a pulper feed system to adjust to the changing market demand.
“The investment will allow the mill to supply a global customer base and give the business additional opportunities we’ve previously lacked,” says Andrew Cooper, Vice President, Operations at NDP.
A challenging and exciting project
Nippon Dynawave Packaging LLC was created in September 2016 when Weyerhaeuser sold its liquid packaging board business to Nippon Paper Industries.
“This new pulp drying and baling line project is the first large greenfield project executed since the acquisition. The project has been both challenging and exciting,” says Cooper. Jussi Rasi, Senior Project Manager at Valmet, agrees with Cooper and confirms that there have been challenges in the project, especially because of the Covid-19 situation. “Our engineers have designed a very economical wet end solution for this project. Another new feature is the fold-up hatches on the dryer ends, which will facilitate maintenance.”
“We’ve managed to keep things functional during the project, even though we haven’t been able to send people from the Nordics since the installation started at the dryer section. We’ve had to be creative and find local solutions and provide support remotely. We’ve also learned a lot together with the customer in this project and have had to adjust to the special conditions that apply in a seismic zone – for example, an extra heavy-duty foundation,” Rasi explains.
"Valmet has provided excellent regional sales and technical support for all our projects, and was very willing to engage with NDP in the development of this one " says Andrew Cooper.
A strong partner, willing to engage
Valmet has been a strong partner, having executed several projects across the site over the last ten years. That was also the reason behind the choice of the new pulp drying line’s supplier.
“In our experience, Valmet has provided excellent regional sales and technical support for all our projects, and was very willing to engage with NDP in the development of this one, despite its smaller size, to craft a solution to meet NDP’s goals,” Cooper explains.
The solutions presented by Valmet in this project have generally met every expectation.
“Our expectations in partnering on projects have focused on very high levels of cooperation, communication, responsiveness, technical support and knowledge. The size of our business means NDP also always focuses on cost savings and project returns. The solutions presented in this project have generally met all these expectations,” he continues.
Safe and efficient
A safe working environment has been of the utmost importance. Throughout the project, NDP has sought to build safety features into the facility. The installation is divided into safety zones: If anyone enters a safety zone, all the power sources are interrupted, ensuring the highest possible safety level.
“Overall, NDP has been satisfied with the safety performance of its contractors and Valmet during the construction phase. We’re expecting the new production line to be the safest in the facility. Beyond that, we expect the new line to offer world-class reliability, and to be energy efficient and as productive as any pulp line in the world per width of production,” says Cooper.
An automatic pulper feed system was chosen to ensure the safest possible operating system while minimizing the manpower requirements of feeding the pulper.
After the start-up at the end of 2020, NDP will be a flexible mill that can adapt to the market, choose the most economical fiber for the moment and maximize its pulp production capacity.
To meet a customer requirement, the baling line will be equipped with Allen Bradley PLC components in this installation.
Sustainable end products
NDP’s products play an essential role in delivering fresh liquids to nourish people all over the world. Their board holds fresh liquids for school milks, fruit juices, nectars, coffee and water, and provides packaging for various food service applications. NDP’s pulp is used by tissue and towel manufacturers, packaging and communication paper producers, and even pet bedding manufacturers.
Text Kerstin Eriksson
Basic facts
- Location: Mill site in Longview, Washington State, USA
- Start-up: Q4 2020
- Capacity: 525 ADMT/d
- Wood species: HW/SW
- Trim: 2,400 mm