From machine rebuild to new quality control system
Valmet’s capability to cover the entire project scope sealed the deal when BillerudKorsnäs Karlsborg’s pulp mill was looking to replace their old quality control system. The package included a required machine rebuild and the installation of a new system for grammage and dry content control.
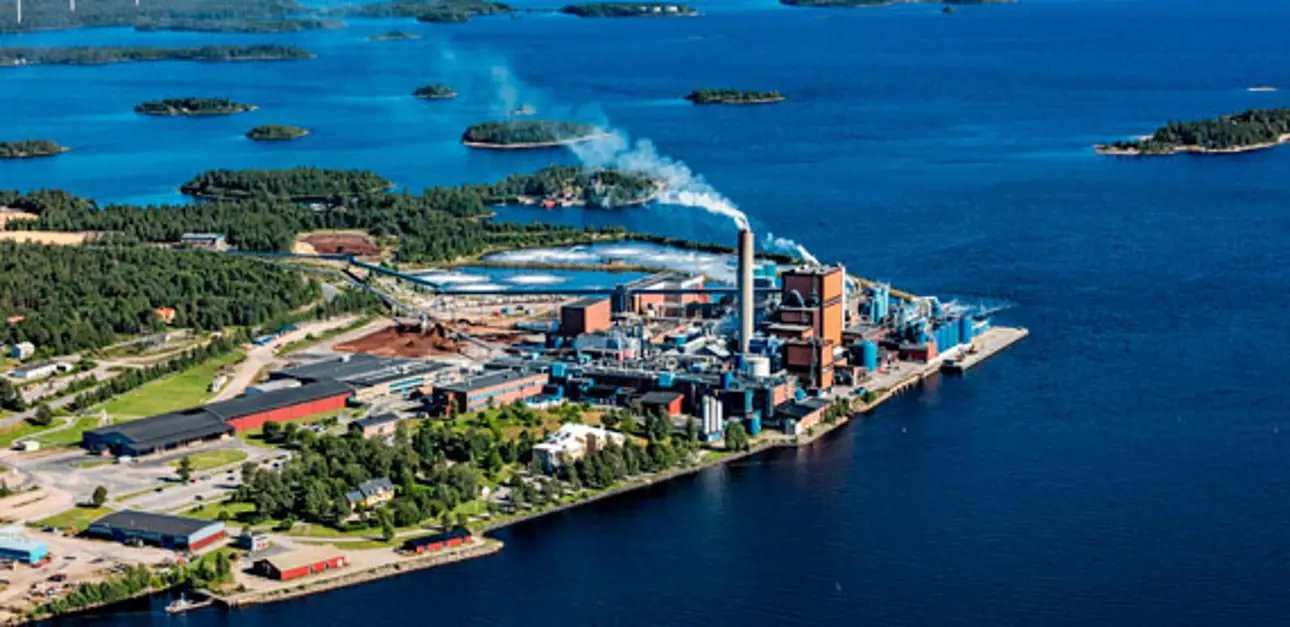
BillerudKorsnäs Karlsborg produces 330,000 tonnes of bleached softwood pulp, out of which 130,000 tonnes are pumped to the integrated paper mill producing bleached sack paper, kraft paper and formable paper (FibreForm). The remaining pulp production is dried on drying machine TM3 and sold as market pulp. The mill has a long history with Valmet and in 1980 Karlsborg, as the second mill in the world, installed a Valmet Damatic Classic control system for control of the fibre line and later also production of electricity and steam recovery.
Mikael Strand, Head of Section TM3, Bjarn-Olof Johansson, Project Engineer, Mattias Arvidsson, Project Leader, and Jan Johansson, Process Operator, TM3 at the Valmet IQ Scanner after the drying section.
“The previous control system in TM3 had passed its technical life span and we could no longer get spare parts so investing in a new system was necessary,” says Bjarn-Olof Johansson, Project Engineer at BillerudKorsnäs Karlsborg. “For the new system we had a long-term perspective regarding monitoring and control of dry content and grammage profiles in the machine direction and later maybe also of the corresponding cross direction profiles and maybe even more properties. Therefore it was important to get the best system and not be trapped in the future.”
“Initially we looked at four suppliers of systems for dry content and grammage control in the drying machine,” says Mattias Arvidsson, Project Leader at BillerudKorsnäs Karlsborg. “The machine is quite cramped which meant that a certain rebuild after the dryer section was needed in order to make space for the dry content and grammage scanner. Different suppliers had different solutions for how this could be done and by whom but Valmet was the only one who could take total responsibility for the whole package of rebuilding and control system. That is why Valmet was chosen as supplier, we did not have to take care of the rebuild and control it ourselves as it was in their hands.”
The Valmet IQ Scanner after the drying section measures grammage and dry content.
“To us it is of course a big strength in a project like this that we can involve our “heavy metal group”, i.e. Valmet Technologies, says Juha Mykkänen, Sales Manager Pulp and paper Industry, Automation Business Line, Nordics area, Valmet Automation Inc. “Therefore we do not have to involve external mechanical partners, we can give a guarantee covering the whole package. For the customer this means safety at the same time as we at Automation know that the total solution will be good.”
“As two Valmet parts were involved we demanded and got one contact person from Valmet in this project,” Bjarn-Olof Johansson continues. “It was not so easy to find the right place for the scanner after the dryer but with help from Valmet’s specialists we found a place which turned out to a be very good one. The solution was to move the carrying roller one meter forward to get the necessary space for the scanner and at the same time obtain a good solution for the threading so that the pulp web can fall down without any problem in the pulper.”
“The project consisted of two parts, the rebuild after the dryer including necessary mounts, which was done during the maintenance stop in August 2017, and the installation of the Valmet IQ System which was done in October 2017,” Mattias Arvidsson says. “It was a giant task for us to map all signals needed for a trouble-free system integration with the existing Valmet DNA system as well as with the DCS system from another supplier in advance. The DCS system controls among other parameters pulp and steam flows as well as machine speed. The integration between these systems had to be done seamlessly and hence the preparatory work was very important. In addition, we must not forget the great importance of Valmet’s education of our operators before and after the installation of the new system.”
There is a one-sided Valmet IQ One-Sided Scanner above the pulp web measuring dry content and temperature of the pulp web.
An important part of the project was that Karlsborg’s project group went to Tampere for a FAT, Factory Acceptance Test, of the Valmet IQ System for the drying machine. The purpose was to check that everything was built, that all process displays and controls were ready as well as a follow-up on the project status. The project group was very satisfied with the FAT results, both the technical side and the way Valmet had organised the tests. The Valmet IQ system for Karlsborg’s drying machine consists of a Valmet IQ One-Sided Scanner before the dryer, positioned above the pulp web measuring dry content and temperature, one Valmet IQ Scanner measuring grammage and dry content after the dryer and of course all the software needed.
“The start-up went better than expected and we had a good support by Valmet’s start-up staff,” Mattias Arvidsson emphasizes. “There were of course some minor things during the start-up period but they were quickly sorted out. We can now control grammage and dry content profiles as well as coordinated speed in the machine direction as the signals from the system influence the pulp flow, pressure in the headbox, machine speed and steam flow to the dryer.”
Mattias Arvidsson and Bjarn-Olof Johansson have a discussion at the Valmet IQ Scanner after the dryer.
“Our fears that the relocation of the carrying roller might cause problems with the pulper during threading were proven totally wrong as it has worked just fine”, Mikael Strand, Head of Section TM3 adds. “All in all, the project has been very smooth and due to the Valmet IQ System we can see that the drying machine is now run in the same way irrespectively of different shift teams. This confirms that the operators have confidence in the new system. The old system had passed its technical lifespan and needed a lot of maintenance and the traversing measuring unit even caused web breaks now and then.”
Process Operator Jan Johansson at the drying machine cutter where the bale set balance has been removed.
“As we now have stable grammage measuring and dry content control we have been able to remove one maintenance demanding unit in the drying machine, namely the old balance for bale sets. It used to control the set change in the drying machine cutter,” Bjarn-Olof Johansson points out. “Instead of weighing the set of pulp bales, the weight of each set is now calculated based on the measurement results from the Valmet IQ System and the set change in the cutter is controlled. However, we still weigh each pack of pulp bales on a special pack balance and this weight is the invoiced weight.”
“To sum up the whole project we are very satisfied with how it has been run as well as with the cooperation with Valmet. The result has been very good and we look forward to a continuation during which the grammage profile in the cross direction will be controlled as well as possibly some other quality parameter,” Mattias Arvidsson ends.
Mattias Arvidsson and Bjarn-Olof Johansson at the scanner’s field cabinet.
Bjarn-Olof Johansson shows that the measuring head can be run manually.
Text and photos Soren Back
Related articles