Refining innovation at Mondi Neusiedler
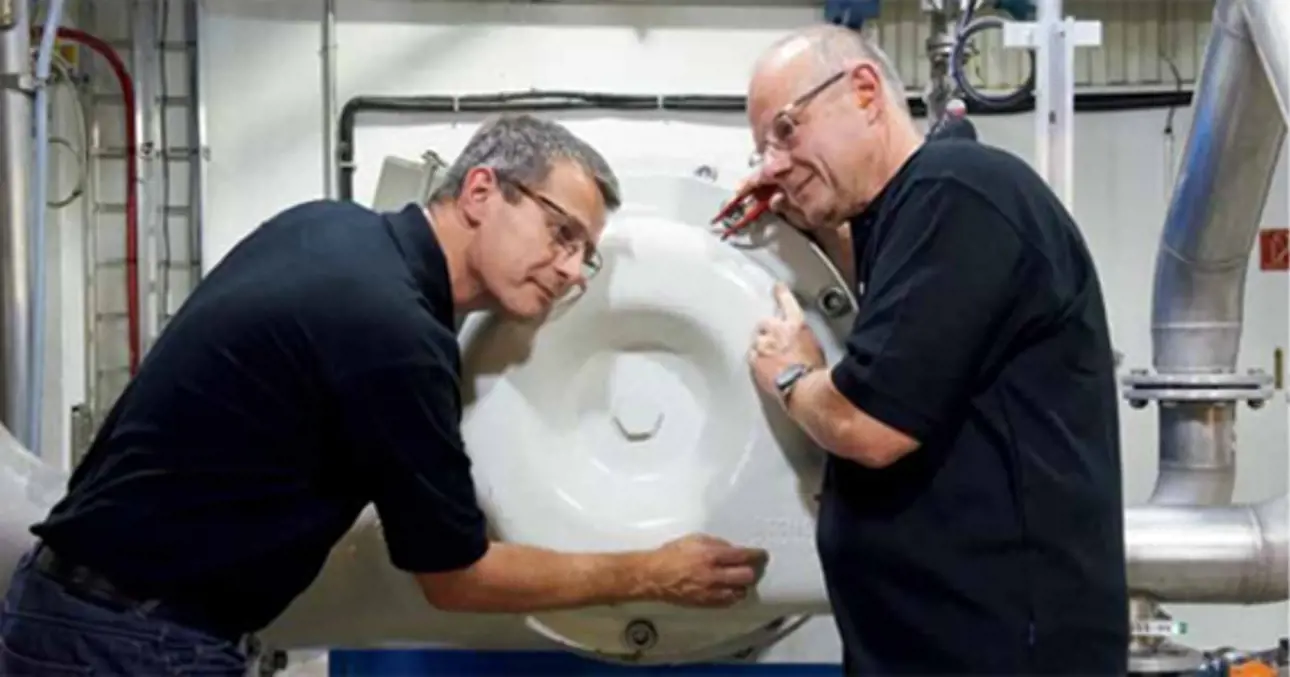
The Theresienthal mill of Mondi Neusiedler produces about 280,000 tpa from two paper machines, PM 5 and PM 6. The bigger machine, PM 6, started up in 1982, and after a complete rebuild in 1995 to a gap former machine with triple layer headbox (the first on fine paper) and shoe press, the machine currently produces mainly 80 g/m2 high quality copy paper.
Refining plays a decisive role in developing the fiber properties of the eucalyptus furnish to the machine and is a major energy consumer in the mill.
With several OptiFiner Pro installations up and running, Valmet* introduced the larger capacity OptiFiner Pro 3 in 2011. Mondi Neusiedler was quick to see the potential for energy savings and promptly commenced on a project to replace existing short fiber refiners. Early in the justification phase it was realized that it was possible to replace all 3 refiners with just one OptiFiner Pro 3.
“As with most European paper producers today, a major objective is the reduction of energy consumption, and over the last 10 years we have had the ambitious goal to reduce specific energy consumption by 15%. At the same time we have focused on quality and total efficiency, i.e. how to develop the fibers, optimize paper properties and improve the overall efficiency of the production line,” says Erwin Sversepa, Production Manager.
Results confirmed
“With OptiFiner Pro we have achieved 24% energy savings with the same refining result. The increase in hydraulic capacity means we have also been able to slightly increase machine speed – earlier attempts used to last only one or two days before the lack of refining capacity led to problems on the machine,” says Wolfgang Leitner, Mill Technologist. With confirmed energy savings, excellent machine runnability and no reduction in quality, the focus is now on throughput and flexibility.
![]() |
With the same refining conditions, the mill achieves 24% energy savings. |
Technological breakthrough
In 2004 the mill took the first crucial step by shifting from mixed to separate refining on PM 6. Following an extensive study and the resulting comparison of technological performance from three potential suppliers, the mill has worked together with Valmet to improve refining, and in particular the fillings design, to optimize strength and reduce energy consumption.
“The excellent results of cooperation with Valmet reconfirmed our common vision of the importance of hardwood refining and we had been successful but now the time had come for a technological breakthrough,” says Sversepa.
Valmet’s answer was OptiFiner Pro, the revolutionary new design providing a better refiner loadability and higher energy efficiency than any other refiner.Unlike conventional refiners, stock is fed evenly through the OptiFiner Pro segments and across the bars, directly into the refining zone where fiber treatment occurs and all fibers are treated evenly. A remarkably higher installed power and throughput is possible, and together with high utilization of the whole refining area and all bar edges, this increases refining intensity.
OptiFiner Pro on trial
According to Project Leader Walter Kronsteiner, it was easy to conduct a trial with Valmet. “They have experts and a technology center in Finland where laboratory trials can be comprehensively compared with our actual production conditions in order to justify our investment.”
The trial parameters employed in Valmet’s technology center on the mill’s pulp were meticulously duplicated with the existing refiners at the mill. This gave the mill a firm baseline for comparison and justification calculations. In addition to standard laboratory tests, such as tear and tensile measurements, the mill relied heavily on evaluation of fiber morphology through microscopic analysis. “Knowing how the fibers develop in refining in addition to the pulp properties was an essential part of the trial,” says Kronsteiner.
The trial showed that for the same physical pulp properties, OptiFiner Pro could achieve a 60% reduction in no-load power and a 20% reduction in effective power compared with the existing refiners. “It was quite easy to quantify these savings in euros and justify the purchase, and our record of previous achievements with Valmet made me very confident of the outcome,” says Sversepa. The decision to go ahead was made and installation on the PM 6 eucalyptus refining line was completed in the summer of 2012.
Short payback
n addition to energy savings and increased production, reduced maintenance and wear part replacement contribute to the return on investment. “Since the number of refiners is reduced from 3 to 1 and we have confirmed that the lifetime of OptiFiner Pro fillings is at least equal to the old refiners, maintenance costs have been reduced by two thirds,” confirms Sversepa.
The conservative estimate is that the whole project payback time will be about one year. Planning for a second OptiFiner Pro is already under consideration. Innovation has guided Mondi Neusiedler for many years and will continue to do so in the future as well.
Read the entire article: Refining innovation at Mondi Neusiedler
* Until Dec. 31, 2013 Metso Paper