What can we learn from the energy industry about mill-wide optimization?
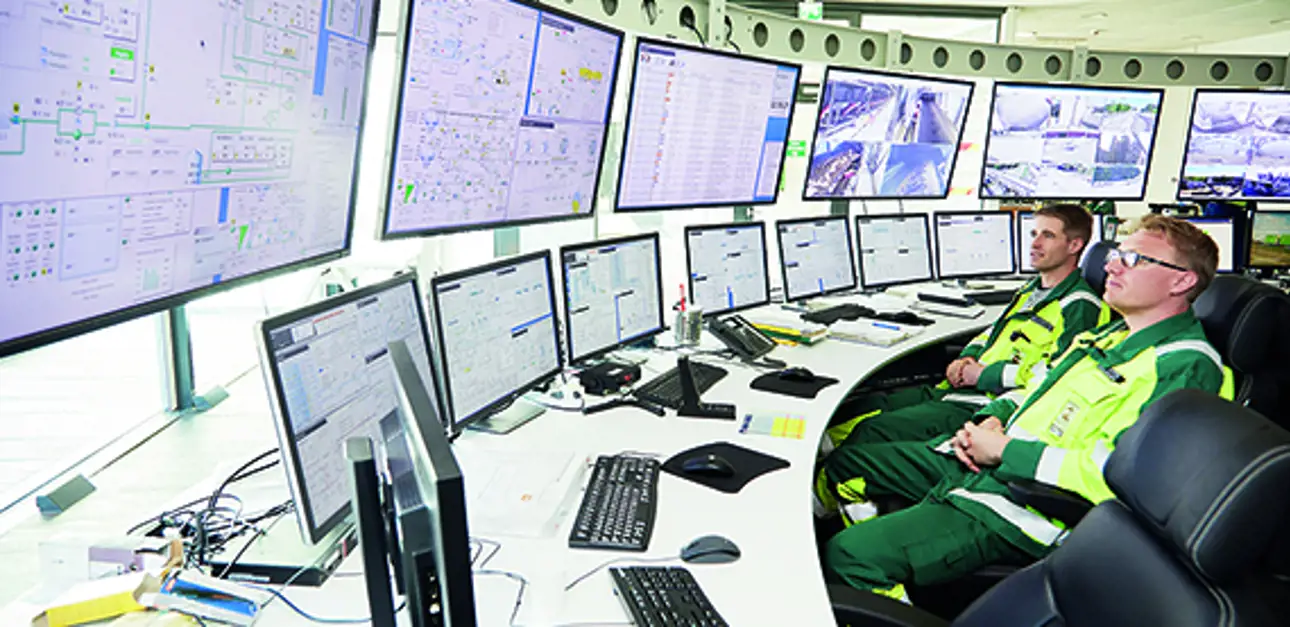
The development of the Industrial Internet toward Artificial Intelligence (AI) and autonomous mills will enable mill-wide optimization of processes. By “autonomous,” I mean machines or mills that can act independently without being controlled by humans.
In today’s pulp and paper plants and mills, much of the planning and preparation is still done manually on a daily basis. The mill and plant experts decide on the next day’s production rates and adjust things accordingly. This way of doing things makes it very difficult to achieve an overall optimal situation and almost impossible to make the calculations. This is where Industrial Internet applications can clearly help.
Remote control rooms and heat network optimization
Although making mills and plants fully autonomous is still a strategic target for many pulp and paper companies, some industries are already seeing positive concrete results from large-scale autonomous operations. For example, the energy industry has been taking concrete steps toward autonomous plants by making centralized remote-control rooms and heat network optimization part of their daily work.
One example is the energy company Helen, which is optimizing its district heating production and network in the city of Helsinki, Finland. The district heating optimization solution coordinates and automates everything from individual pumps and network flow to managing the capacity of entire heating plants, and it also predicts things like delays and different intra-day variations to improve overall network efficiency.
Another example is Turun Seudun Energiantuotanto’s power plant in Naantali, Finland, which runs with Valmet DNA, operating from one centralized control room. From overall process control and district heating management through monitoring emissions and on to managing biofuels from the forest to the gate – everything relies on automation and Industrial Internet solutions. Together, these systems compose one seamlessly functional entity – for basic control, optimization and advanced reporting.
Decision making goes to the next level
Coordinating processes as one big entity allows the optimization of production, quality and costs from a mill-wide perspective. This helps improve the profitability, efficiency and environmental impact of the whole mill.
In Helen’s case, the district heating optimization solution was integrated with its existing production planning and automation systems, and other existing process control and information systems, to ensure everything worked smoothly together. This allows Helen to see the big picture, so it can make decisions about electricity trading, and when to use the network for energy or heat storage. This network-wide approach has reduced Helen’s energy procurement costs and is also helping it to reduce its emissions.
Now: Imagine a morning at the mill when you start your day with a continuously optimized plan for production – and you know you’ll be making the right decisions.
Related reading