Crafting the evolution of tissue making from past to future
Tissue paper is an essential product in households, businesses, and industries worldwide. From humble beginnings to today's highly sophisticated production processes, the tissue paper industry has undergone remarkable transformations over the past five decades.
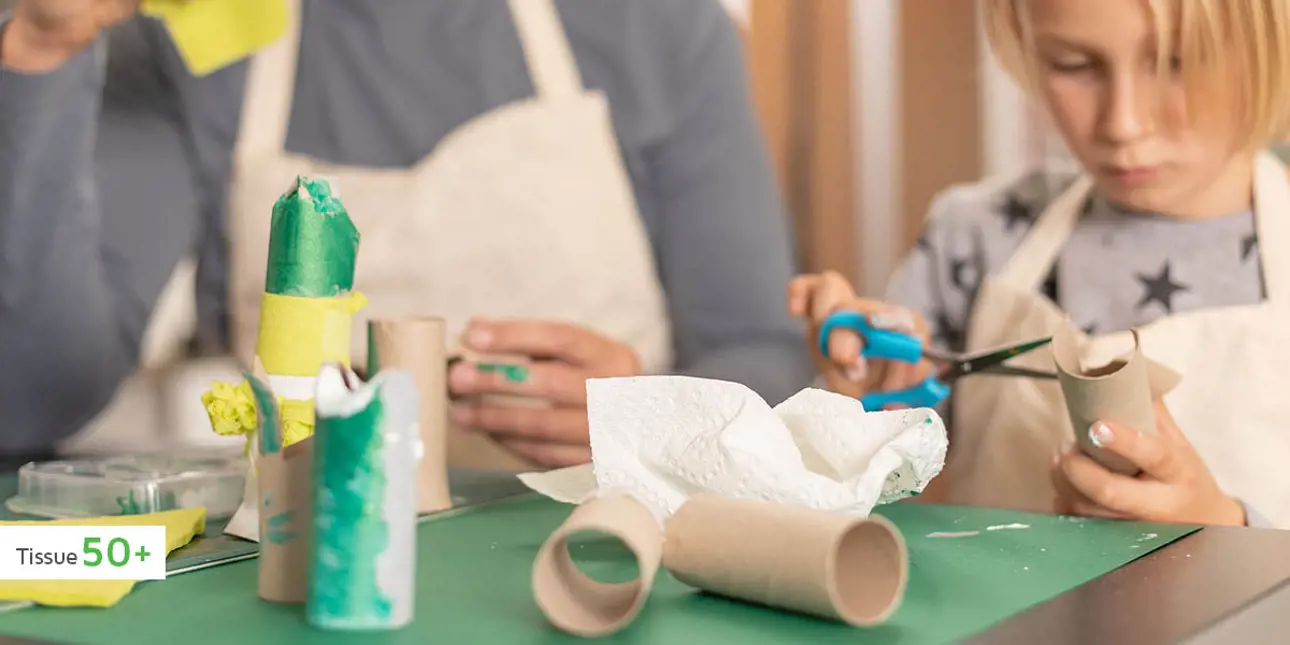
The early days with basic production methods
Fifty years ago, tissue paper manufacturing was a relatively simple process. Mills primarily relied on virgin wood pulp, and the production was energy-intensive, involving large amounts of water and chemicals. Paper machines were slower, and quality control depended largely on manual inspection. The range of products was limited, with basic toilet paper and facial tissues dominating the market.
The shift towards sustainability
As environmental concerns grew in the 1980s and 1990s, many tissue paper manufacturers sought ways to reduce their ecological footprint. The introduction of recycled paper fibers became commonly used and companies began incorporating paper waste into their products, reducing the demand for virgin pulp. Advanced deinking technologies allowed for the removal of ink and contaminants, leading to cleaner, higher-quality recycled tissue products.
Automation and efficiency gains
The 2000s saw a major leap in production efficiency, driven by automation and digital technology. Computerized control systems improved consistency, minimized waste, and optimized resource use. The development of high-speed paper machines allowed manufacturers to produce tissue paper at unprecedented speed, meeting growing consumer demand while keeping costs competitive.
Softness, strength, and performance enhancements
Over the past two decades, innovations in advanced technologies, fiber blending, embossing, and lotion-infused tissues have enhanced tissue paper quality. Modern manufacturing techniques enable the production of ultra-soft, strong, and highly absorbent tissues, catering to a more discerning consumer base.
The rise of sustainable and smart technologies
In recent years, sustainability has become a core focus in tissue manufacturing. Water recycling systems, energy-efficient drying technologies, and biodegradable packaging have become industry standards. Manufacturers are exploring AI-driven quality control systems and smart factories to further streamline production and reduce environmental impact.
Bridging the gap
Initially, the industry was dominated by two primary technologies: Through-Air Drying (TAD) for ultra-premium products with very high bulk, softness and absorption properties and Conventional Dry Crepe Tissue (DCT), which has been and continues to be, the most common and cost-effective process for manufacturing plain paper at low basis weight. In recent years energy efficiency and product quality have been significantly improved in conventional machines after the introduction of the adjustable pressing element (ViscoNip press).
The TAD technology has been the only way for producing ultra-premium quality tissue with superior softness and absorbency. The process is using hot air to dry the paper sheet which enables the high bulkiness. In addition, it comes with high production capacity and fiber saving opportunities.
However, in recent years, flexible hybrid technologies like Advantage NTT and QRT concepts have emerged as significant alternatives, offering premium tissue close to TAD level but utilizing Conventional DCT methods. The flexible hybrid technology aims to combine the best of both worlds by enhancing product quality while maintaining cost efficiency. The benefits include improved softness and bulk, reduced energy and fiber consumption, as well as greater flexibility in product differentiation.
Savings without sacrificing quality
Looking ahead, tissue demand in North America, for example, is expected to grow steadily at around 1.2% annually. While this may seem low, given the high per capita tissue consumption in the region, it translates to approximately 10,500 additional tons per year through 2030. Of this growth, about 70% is projected to be in consumer tissue, with the remaining 30% in Away from Home products. New investments are mostly focusing on production of premium and ultra-premium products where TAD machines are still the preferred choice. Due to a growing interest for energy saving solutions, the hybrid technologies offer a good alternative to balance quality, cost and environmental efficiency. The demand for premium tissue products remains strong, driven by consumer preferences for softness and absorbency.
Shaping the future of tissue making
The future of tissue paper manufacturing will be shaped by advancements in sustainable materials, artificial intelligence, and smart manufacturing. Virgin fibers continue to be the desired raw material especially for premium and ultra-premium products. However, it is likely that we will see other fiber sources, like bamboo, straw and other fast growing fiber sources as eco-friendly alternatives to wood pulp.
The challenge to attract skilled workforce will remain and is putting the pressure of tissue machine suppliers to continue developing AI driven tools and autonomous operations. The capability to develop the tissue making process from fiber in, to finished tissue product out, will have a significant impact on the development of production performance and end-product quality.
The journey of tissue paper manufacturing over the past decades showcases the power of innovation, efficiency, and sustainability. As the industry continues to evolve, retailers have an opportunity to capitalize on these advancements to meet consumer expectations and meet their business targets.
Emerging trends include:
Alternative fiber sources
Increased use of bamboo, wheat straw, and hemp as eco-friendly alternatives to wood pulp.
AI-driven production
Implementation of AI and machine learning to optimize production efficiency, reduce waste, and enhance quality control.
Waterless and chemical-free processing
Development of processes that minimize water and chemical use, improving environmental sustainability.
Biodegradable and smart packaging
Innovations in compostable packaging and intelligent packaging solutions that enhance product freshness and usability.
Carbon-neutral manufacturing
Investments in renewable energy and carbon offset initiatives to achieve net-zero emissions in tissue paper production.
By embracing these advancements, manufacturers and retailers can offer cutting-edge, sustainable, and high-quality tissue products, ensuring continued industry growth and environmental responsibility.
Explore Valmet's tissue making concepts
Learn more about our 50+ journey
2025 marks the year we're celebrating more than 50 years of delivering tissue technology to the world. Through a series of articles, we’ll highlight key milestones, share inspiring personal stories, and, above all, honor the people who have truly made a difference over the decades.
Tissue 50+
Decades of shaping the industry.
More insights from the tissue industry
Explore our customer success stories and learn more about our full-scope offering in the tissue industry.