SCA pulp and paper plant sets new standards
Sustainability and high plant availability are the main requirements of the paper and pulp industry. This goes for SCA as well, which operates its largest European integrated plant for the manufacture of tissue products in Mannheim, Germany. Among other products, some 120,000 tons of pulp are produced here annually in a continuous digester.
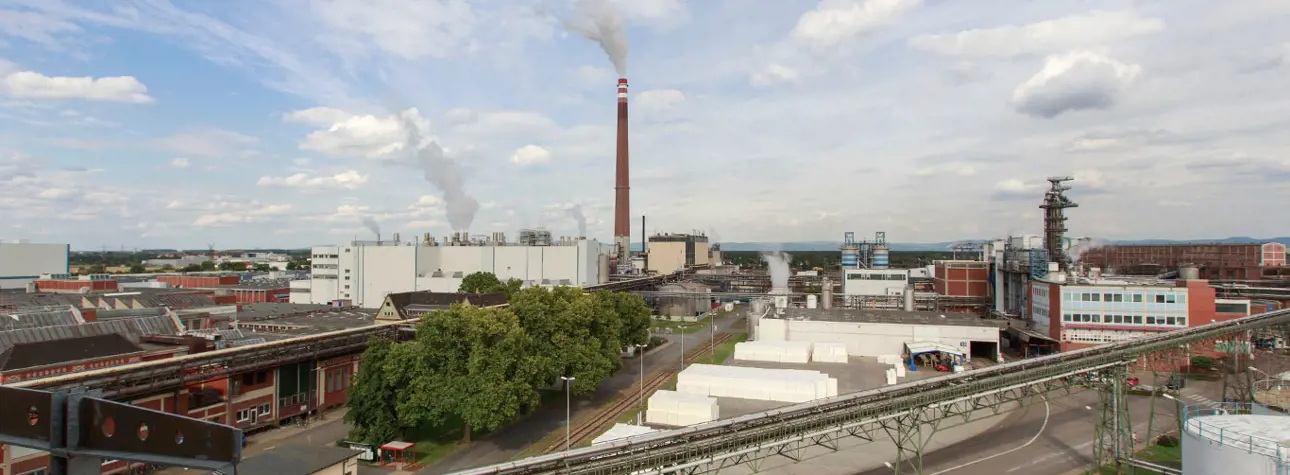
Scheduled system shutdowns twice a year for guaranteed throughput
SCA operates two pulp production lines in Mannheim: one for spruce and one for beech. The production process on the spruce line involves many steps, such as brown-stock washing, sorting, and chlorine-free bleaching. More than 3 million rolls of paper towels, toilet paper and tissues is produced at the Mannheim pulp and paper plant every day.
To minimize potential component and system downtime, SCA conducts scheduled system shutdowns twice a year. At these junctures, the heavily stressed valves on the continuous digester are regularly replaced as a safety precaution, because the digester, after all, delivers the bulk of the spruce pulp that is urgently needed for paper production.
“The valves in our continuous digester have to work under extreme conditions,” points out Jan Wattendrup, head of maintenance for electrical, measurement and control technology on pulp line B at the SCA plant in Mannheim. He is referring to the difficult environment where the on/off valves are installed: “The acidic waste liquor contains process chemicals that are relevant to the cooking operation but can bake onto the valve and cause localized corrosion. Over time, hard deposits form inside the valve and also clog the sealing ring. Since we know about this problem from years of experience but can’t simply switch off the continuous digester mid-operation to make repairs, we replace all valves at regular intervals as a precaution.”
Substantial improvements in the service life of valves
“Regardless of the state of the valves, we routinely replace eight of the segment valves for the continuous digester during each scheduled shutdown,” Wattendrup says and goes on to explain the reason for this action: “As a rule, 75 percent of the valves are no longer operational after one year. Only a few valves can be reconditioned and kept on hand as spare parts for the next shutdown. Our ultimate goal is therefore to extend the service life of valves.”
In order to achieve this, SCA tested high-alloy stainless steel segment valves. “The Valmet valve impressed us first with its design, which is identical to that of the previously installed valves,” said Wattendrup. “In contrast to the second test valve with a longer form, we didn’t need to make any modifications to the pipes, which of course saves us labor and costs. The Valmet valves are also more compact and lightweight, making them easier to transport up to the digester.”
While these benefits apply initially only to assembly, the newly installed V-port segment valve went on to demonstrate further special properties during the first six-month test phase. “During the scheduled shutdown, we removed and inspected both test valves. The results were so striking that we immediately reinstalled the polished Valmet valve for a further round. In the meantime, these valves have been functioning for almost one-and-a-half years without damage or restrictions,” confirms the maintenance manager.
This is why the newly installed on/off valves from Valmet, made of high-alloy stainless steel, polished on the media-affected inside surfaces, represent a key solution that allows SCA to substantially extend the valves’ service life.
Valve technology used at SCA
The complete valve technology at the SCA plant comes from Valmet. “Based on decades of positive experiences, we have chosen Valmet as our standard supplier for valve technology,” says Jan Wattendrup, adding: “We always get quick help and support – both for technical questions and with regard to the components themselves. That’s why we feel we are in very good hands with Valmet as a trusted partner, especially because we can rely on a consistent total package, from product to service.”
TEXT: Ursula Gehl
Text originally published in 2017, and slightly updated in April 2022, due to the company name change to Valmet.
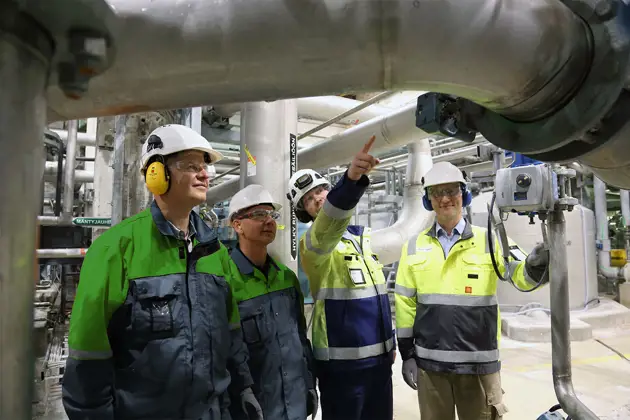
Subscribe to our newsletter
Subscribe now to flow control newsletter and receive the latest insights directly to your email.
SubscribeRead more customer success stories