Ready for the challenge: Valves enhance fluidised-bed polymerization
The global olefins market is expected to grow by about 4% or more in the next several years. The packaging and automobile industries are examples of important users of polymers. The major source of olefins, the building blocks of polymers, namely ethylene, propylene, butadiene and isobutene, is steam cracking.
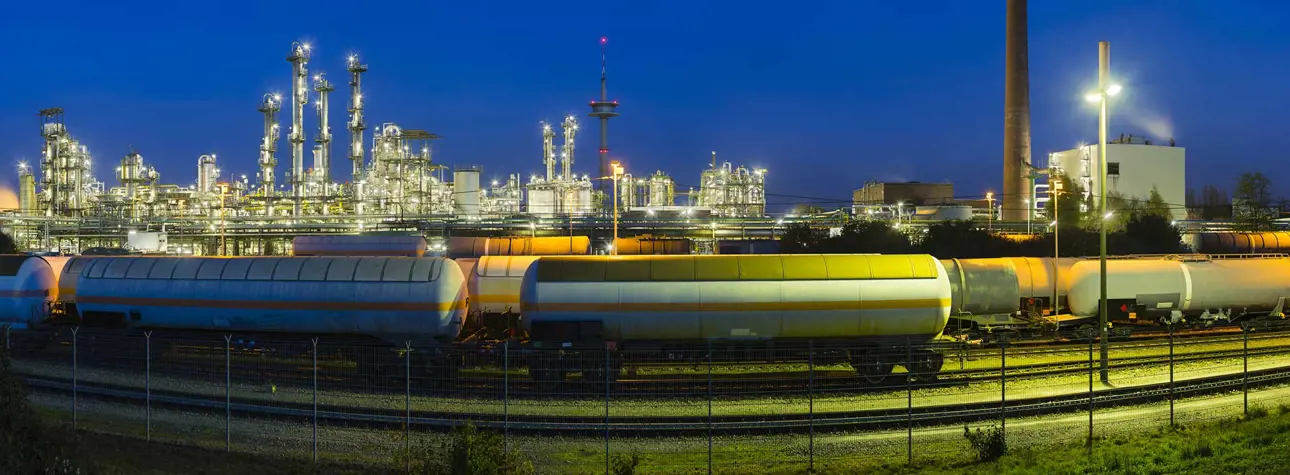
The global olefins market is expected to grow at approximately 4% or more in the next several years. The major source of olefins, the building blocks of polymers, namely ethylene, propylene, butadiene and isobutene, is steam cracking. Some volumes of olefins are produced from catalytic cracking. Technologies such as propane dehydrogenation are also becoming more popular to produce olefins, especially in locations short of olefin supply from naphtha cracking. There are several licensors offering technologies to produce polymers. Factors associated in selecting an appropriate technology license include, but are not limited to, the capability of the process to produce the desired polymer grades, diversity of the process technology, ability to produce specialty grades, catalyst options and cost.
- Highlights
- Global demand for clean and high quality polymer production is growing
- Gas-phase polymerization processes are very economical at producing commodity-grade polymers
- Valves play an extremely important role in the successful product discharge system performance of a gas-phase polymerization reactor
There are three major types of low pressure technologies, namely slurry, solution, and gas phase. Each type of process has limitations on the versatility of the resins it can produce. Gas phase processes are either stirred bed type or fluidised bed type. Gas phase reactors have the widest operating window, but they encounter difficulties in producing polymers with very low densities due to stickiness and particle agglomeration.
Gas phase processes are very economical at producing commodity grade polymers, and thus, are popular with polymer producers. These polymers, for example, are linear
low density polyethylene (LLDPE), high density polyethylene (HDPE) and polypropylene (PP). This article focuses on the fluidised bed type of gas phase polymer process, and in particular, the challenges facing valves to provide solutions for polymer product discharge applications to enhance process reliability and efficiency.
Process overview
In a gas phase fluidised bed reactor, gaseous monomer, comonomers and proprietary catalysts combine to produce a dry, comonomers resin. This resin, along with hydrocarbon vapour, unspent catalyst, and possibly polymer sheets and chunks, flows from the reactor to the product discharge system (PDS) where unreacted gas is separated from the product and returned to the reactor. The PDS consists of one or more product chambers, as well as an assortment of valves and piping for product conveyance, isolation, gas venting and recycling, and cross tying with other PDS legs. Downstream from the PDS, the product is purged with nitrogen to remove any remaining hydrocarbons. Finally, the granular polymer is pelletised with application appropriate additives.
Figure 1. Gas phase polymerisation PDS with valves.
There's a number of piping attached to the reactor, also called as 'legs' to discharge the polymer from the reactor on frequent basis. The discharge is based on pressure and gravity. The reactor pressure is approximately 30 bars. There is a continuous switching between the reactor discharge piping, ‘legs’. After the polymer flow to the leg is switched to the other leg, the leg is cleaned by flushing it with ethylene or propylene gas to ensure no polymer dust or chunks remain trapped anywhere inside. The largest reactors are capable of processing 400 000 – 600 000 tpy of polymer.
Challenges for valves
Valves should be able to withstand a high cycling rate, with a range from 200 000 to 1 million cycles yearly, depending on the type of reactor and discharge piping. Meanwhile, in most applications, a fast cycle time of less than 2 - 3 sec is required. Therefore, high cycle design and construction of both the valve and the actuator are essential. High pressure differences over the valve, combined with pipe vibration and blending forces, require that the valves are highly rigid and have long lasting tightness. Some medium may contain hydrocarbon vapour, nitrogen, resin, unreacted polymer, and sometimes even sheets and chunks of polymer. The valve seat and bearing must resist the growth of polymer in cavities and grooves due to the continued polymerisation of the media. Valve leakage poses both an environmental and safety issue due to risk of fire, toxicity, and the volatility of gaseous hydrocarbons. Graphite packing is usually not allowed due to the tight colour specs of the final polymer product; the polymer has to be very clean, bright and clear. Modern catalysts used to improve the end product polymer quality, when combined with the produced polymer, are harder and therefore more abrasive to piping and valves.
The market requires clean and high quality polymers. It is important that the process is stable, flexible and under control. Proper valve performance in the piping attached to the reactor, product chambers and the whole polymer discharge system improve the accuracy and reliability of throughput control and favourably affects the plant performance. Valves play an extremely important role in successful product discharge system performance. Polymer resin producers are looking for longer plant run times, since downtime means production losses and represents significant costs that include maintenance costs. This calls for unquestionable equipment reliability.
Withstanding high cycle polymerisation demands
Metal seated ball valves equipped with high cycle piston actuators, such as Neles’ rugged trunnion mounted ball valves, have been the choice for many polymer producers for critical applications in the gas phase product discharge system, such as block valves and discharge line valves. This choice has been made due to the polymer proof metal seat that prevents polymer from penetrating behind the seat and seizing the valve, and due to the anti abrasive feature that makes it a perfect choice for hard polymer and more abrasive catalysts, which are nowadays widely used to improve the end product polymer quality. The valve seating principle is very simple: the seat has continuous contact with the ball, wiping the seat surfaces with every cycle to prevent polymer build up. This provides a means for reliable, long lasting tightness and cycle life in these demanding applications.
“Polymer resin producers demand unquestionably reliable equipment for their fluidized-bed type of gas-phase polymer processes.”
The use of rotary valve technology provides a way to keep the volatile hydrocarbon emissions low during the whole cycle life. This is based on a certified, emission proof stem sealing with live loaded packing that is designed to keep its tightness, even in very high cycle applications. This kind of high cycle application calls for an actuator that is tested and field proven to withstand a high number of cycles without failing. An intelligent, integrated PDS valve controller, such as Neles™ SwitchGuard with unique embedded diagnostic features, enables users to guarantee the availability of high cycling PDS valves.
This type of controller gives the possibility to set the on/off valve stroking times and profiles according to the process needs. This means that the valve opening and closing times, as wellm as the stroking ramp profile, can be defined independently. This feature is especially useful in minimising the pressure impacts on piping (water hammering). Its high pneumatics capacity also gives the possibility to reach fast stroking times without the need for any additional accessories, such as volume boosters or quick exhaust valves. An integrated controller reduces installation costs by eliminating the need for external solenoid valves. In addition, predictive maintenance can be practiced with the help of the diagnostics provided to secure continuous PDS valve operation.
Conclusion
Global markets are calling for more polymers. Gas phase polymerisation processes are very economical at producing commodity grade polymers, and therefore, are popular with polymer producers. The market demands clean and high quality polymers. It is important that the process is stable, flexible and under control. Valves play an extremely important role in the successful product discharge system performance of a gas phase polymerisation reactor. High cycle design and construction of both the valve and the actuator are essential. An intelligent, integrated PDS valve controller, with unique embedded diagnostic features, enables users to guarantee the availability of high cycling PDS valves.
TEXT: Sari Aronen
Published in Results flow control customer magazine 2/2015.
Originally published in HYDROCARBON ENGINEERING October 2014.
Text originally published in 2015, and slightly updated in April 2022, due to the company name change to Valmet.
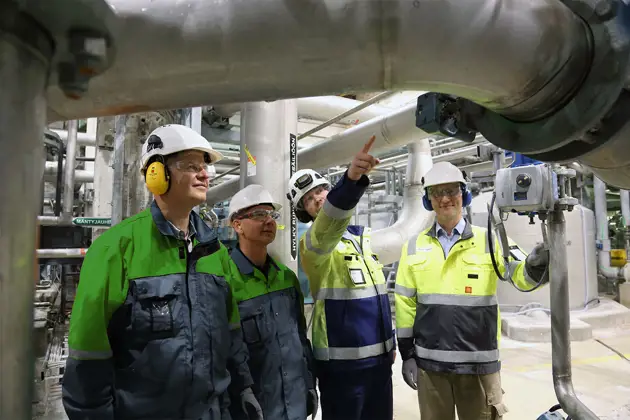
Subscribe to our newsletter
Subscribe now to flow control newsletter and receive the latest insights directly to your email.
SubscribeRead more about polyolefins and polymers