How spray guards enhance safety
Our expert Peter Börjesson was asked to answer queries about an intriguing valve photo.
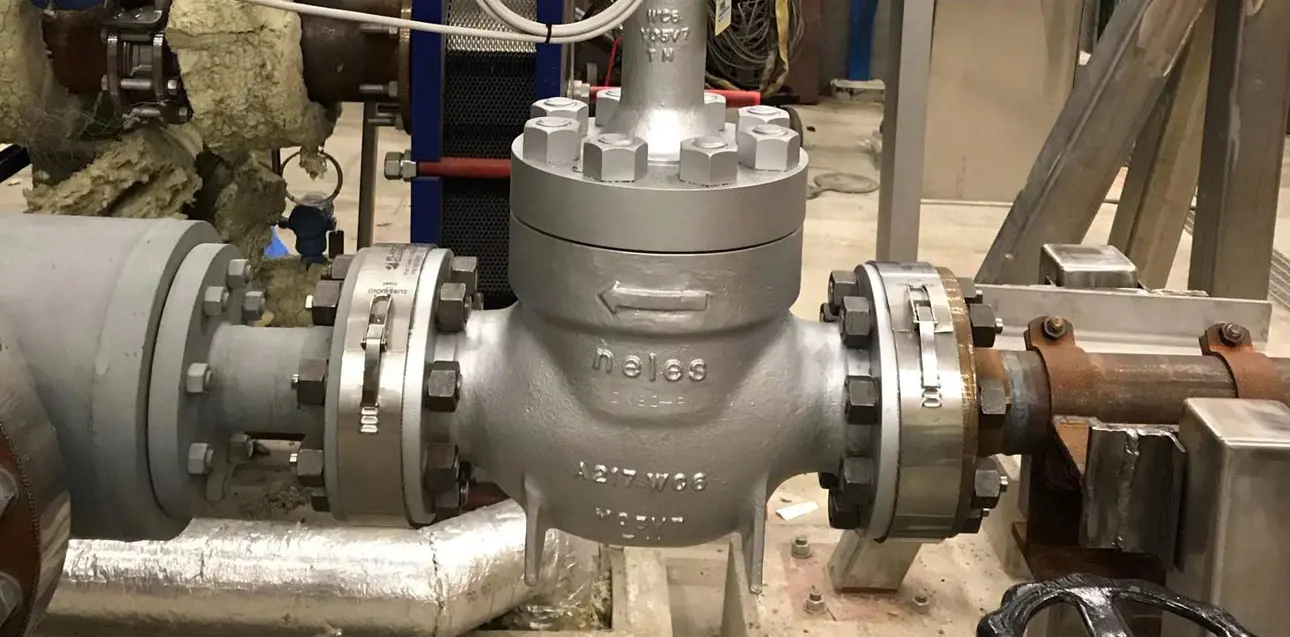
Peter, you recently posted a photo of an installed control valve on LinkedIn with an unusual-looking flange arrangement. What is that?
You are not the only person to ask! This is a standard flange joint that has been fitted with spray guards, which may also be called spray shields. In Sweden at least such guards are very common safety devices, especially in high-pressure applications. For the record, they are not part of the Neles (now Valmet Flow Control business line) portfolio. They are readily available and can be easily used on all types of flanged valves, irrespective of the manufacturer.
Note the spray guards fitted to the valve/pipe flange joints
How do flanged joints with spray guards work?
The integrity of flanged joints typically relies on the gasket material installed between the flanges. If for whatever reason the material degrades, or the force applied via the bolts changes over time, then the joint may be compromised. If you have a high pressure fluid inside the pipe that could then be emitted as a jet or as a mist, potentially causing harm to workers close by or, in the event of a flammable substance, result in a fire or an explosion. Spray guards offer an extra level of security. They are not designed to contain the leak indefinitely, but ensure that any fluid which does escape is depressurized and is released in drip form.
These guards look very simple devices. Are they effective?
Simple but effective!
Spray guards are simple but effective. They are therefore increasingly commonplace throughout the Nordic region, where safety is given top priority within process facilities.
They are therefore increasingly commonplace throughout the Nordic region, where safety is given top priority within process facilities. You know, spray guards are actually quite interesting, with a range of materials and designs available for specific circumstances. For example, stainless steel is typically used for steam applications whereas if the media is a chemical you mostly see a transparent plastic being used. Plastic spray guards normally encase the entire flange, enabling a cloth or pad to be inserted that can soak up any fluid that might potentially drip onto workers present beneath the pipes. These pads often change colour when wet, so the leak can be easily spotted and rectified by maintenance crews.
Just for the record, what type of valve is on the photo above?
It is a globe valve installed in a highpressure steam application. As we have a full control valve portfolio for all process industries we can always select the best possible control valve solution for each application. Globe valves are widely used in for example higher pressure applications while our rotary control valves are typically selected for control applications requiring higher flow capacity, for fibrous flow mediums or applications containing slurries, polymers or even hard particles.
Thanks to Peter Börjesson, Technical Sales for Neles in Sweden, for kindly providing these insights into spray guards.
Text by David Sear. This article was originally published in Valve World India & Middle East magazine, February-March 2021 issue.
Text originally published in 2017, and slightly updated in April 2022, due to the company name change to Valmet.
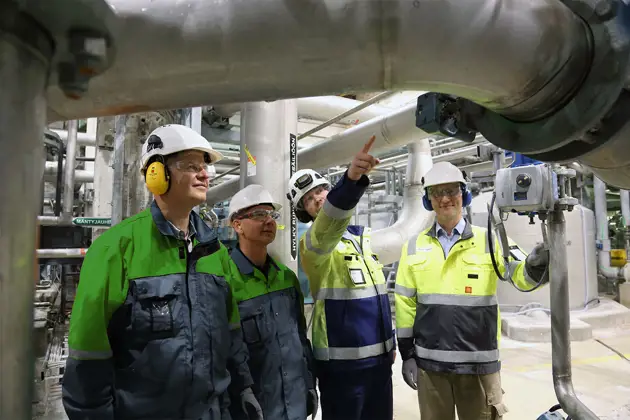
Subscribe to our newsletter
Subscribe now to flow control newsletter and receive the latest insights directly to your email.
SubscribeRead more insights and discover Neles control valves