Digital solutions bring reliability and predictability to aging plants
The current trend toward digitalization is not limited to new, greenfield plants. In fact, older plants may actually be in better position to reap the benefits of digital solutions. This article will show you how to improve reliability and predictability by transforming plant data into useful, actionable information.
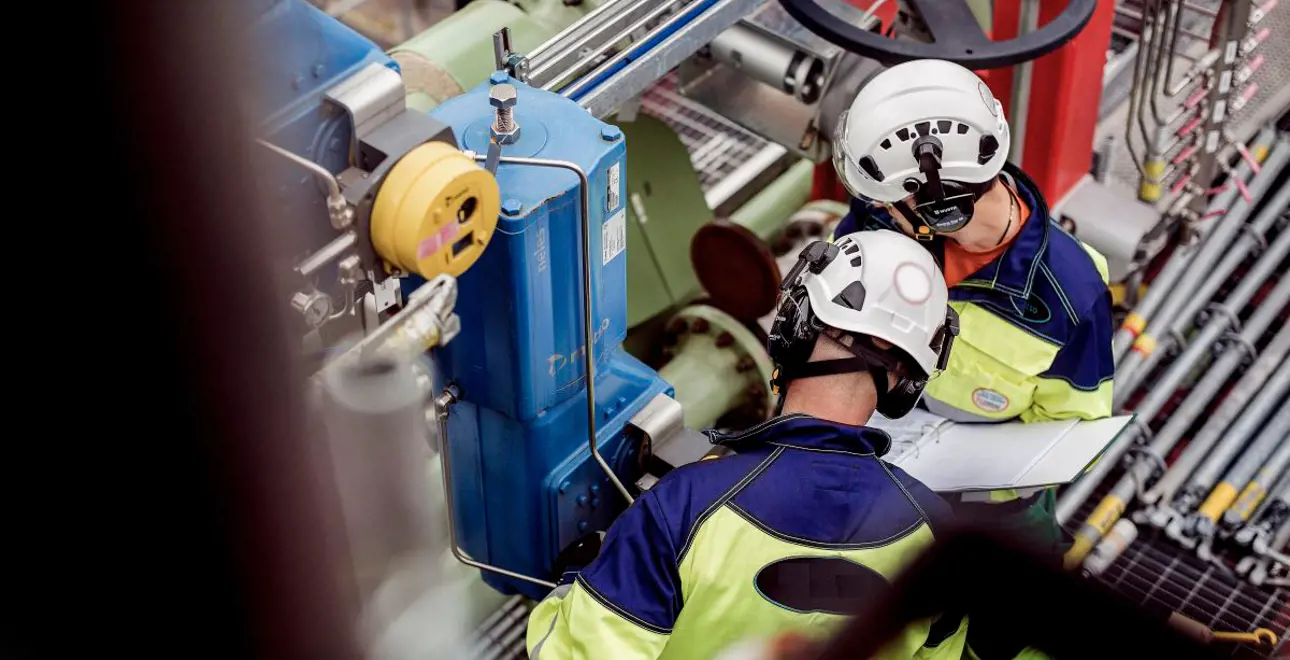
Aging plants have a lot of data
The manufacturing industry is flooded with data. According to a study by McKinsey, the manufacturing sector produces more data than every other industry, including banking, retail, and even government. Much of this data comes from real-time measurements directly on the plant floor. Instruments measure flow, level, temperature, valve positions, motor speeds, and more. Most of this data is fed to control systems, where it becomes electronic information. Smart devices, which appeared in the 1980’s, supply even more rich data.
The data it isn’t being used
Forbes reports that less than 1% of data is being analysed. This is consistent with our practical experience, as most plants have historical data stored, but only have limited tools and staff for analysis.
A follow-up study shows that, over a five-year period, only 20-30% of possible gains for manufacturing were achieved – and most of those by just a few industry leaders. The lost opportunity is obvious. Even the simplest forms of condition monitoring and predictive maintenance solutions can bring big gains, because they simply have not been applied at most plants. The ‘low hanging fruit’ can deliver gains in reliability, stability, production increases, and cost management. Neles’ own studies at process plants in Pulp & Paper, Oil & Gas, and other process industries show that over 30% of installed control valves have some mechanical or sizing issues, and over 30% of controllers are operating in manual mode. Resolving these two issues alone can bring significant improvement to plant operations.
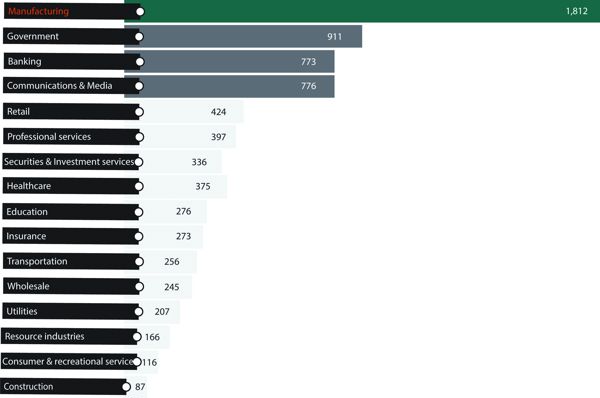
Figure 1. The manufacturing industries are the biggest generators of data.
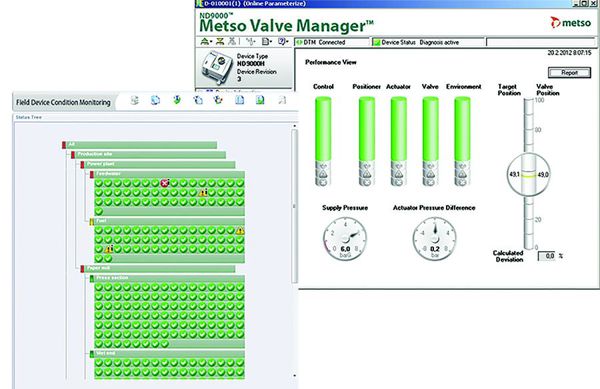
Figure 2. Plant personnel can focus attention and efforts with root-cause diagnostics.
Digital solutions at the plant floor
Smart instruments and smart valve positioners have been on the scene for over thirty years. They contain information from on-board diagnostics that can provide great insights. For example, a smart valve positioner can tell you if its air supply pressure is too low or too high. It can also trend the amount of force required to open the valve. When the opening force trends upwards, this can indicate damage to the valve, or even more specifically, to the valve seats. If this problem is not fixed, the valve can fail open (leak through), stick, or fail closed, depending on the situation. Resolving this issue may prevent quality issues and may avoid an unplanned plant shutdown.
By paying attention to early warning signs like the trends in valve opening force, you may be able to prevent shutdowns in your plant. Gateways and software solutions can simplify the task of gathering and analyzing the data from hundreds of smart devices throughout the plant. These are quite useful to minimize the effort but building out this infrastructure is not an absolute requirement. Handheld devices can gather the data from the instrument directly, or via connections at the I/O cabinet.
Even the simplest forms of condition monitoring and predictive maintenance solutions can bring big gains, because they simply have not been applied at most plants. The ‘low hanging fruit’ can deliver gains in reliability, stability, productions increases, and cost management.
Even analogue devices can provide smart advice
One of the biggest misconceptions of digitalization is that you must invest in large-scale instrumentation, networks, and web-connected software solutions. This is far from the truth. In fact, with the wealth of existing data already available at a plant, meaningful analysis is possible with legacy analogue instruments and valves. Even 20-year-old legacy control systems usually have some way to store and share data. Open standards, such as OPC, have been providing methods to extract the data for more than 20 years. Older systems can export text-based data and may require system-specific tools.
The combination of software for condition monitoring, with smart device data for detailed evaluation, provides the most complete solution. With this combination, it is possible to provide a very accurate diagnostic, from which accurate maintenance plans can be developed. Standard diagnostic algorithms also make it possible for personnel with low levels of experience to be provided with accurate diagnostics.
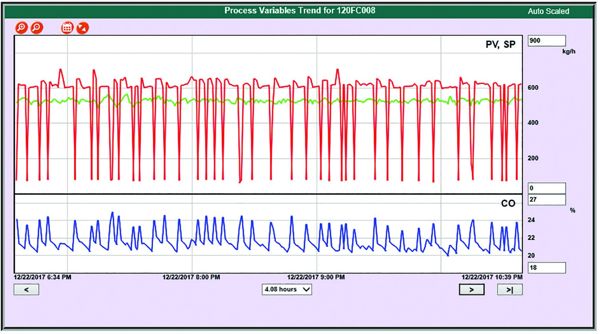
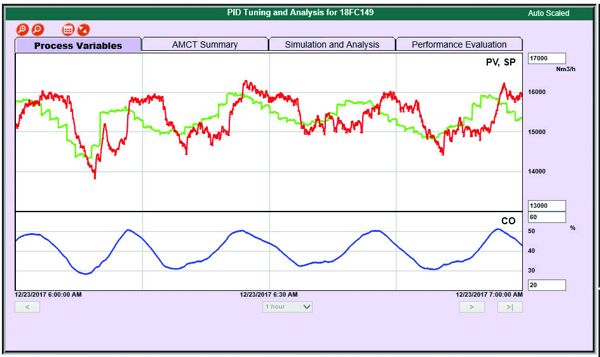
Diagnosing common issues with instruments, valves, and equipment
Instruments, valves, and equipment fail in many predictable ways. To improve reliability and predictability, you need to watch for certain specific patterns and trends in the data. While manual tracking is possible, software tools, such as Neles’ Expertune PlantTriage, can perform much of the initial screening. This allows plant personnel to focus on the corrective actions, rather than performing manual analysis.
Detecting imminent instrument failures
Instruments are the eyes and ears of the plant. Pressure, level, flow, and temperature sensors watch over the normal and abnormal situations that happen in the plant every day. When an instrument starts to fail, the operator may be presented with incorrect data, or even no data at all. Fortunately, instruments do not always fail suddenly. Common warning signs include:
-
High noise levels – may indicate a loose electrical connection, a poor tap, or air in the line
-
Low noise levels – may indicate sensing line plugging, or over filtering
-
Instrument drift – loss of calibration over time
-
Instrument spiking – for some instruments, indicates imminent failure
Many of these issues can be corrected while the process is in operation and may prevent an unplanned shutdown.
It is especially important that the use of condition monitoring tools is integrated into daily operation and maintenance.
Detecting valve mechanical issues
A sticky valve can create havoc in a process operation. Imagine trying to drive your car if the steering wheel sticks left of centre and sometimes right of centre. You will constantly be jockeying the wheel back and forth to attempt to drive in a straight line. Figure 4 shows how a sticky valve causes the same back-and-forth operation in a process plant.
A sticky valve may indicate damaged seats, process residue build-up, or partial actuator failure. Each of these cases is an early indicator of a bigger failure to follow. Finding and repairing the problem may avoid an unplanned shutdown later.
In addition to screening for problems, diagnostics can also provide greater accuracy in identifying the specific problem. For example, you may not be able to identify that the cycle in Figure 4 was caused by a sticky valve, rather than some other issue. However, if you plot the flow against the commanded valve position, you can immediately see the ‘steps on a ladder’ pattern that confirms valve stiction. This is shown in Figure 5. This accurate diagnosis stops the plant from wasting time on other possible causes, such as controller tuning, instrument failure, and air supply issues.
Mechanical linkages and assemblies are also known to fail. In one case at a paper mill, PlantTriage software detected strange behavior on a valve. Upon inspection, it was seen that the four bolts holding the actuator on to the valve had become loose. Had this been allowed to progress, the actuator would have literally fallen off the valve and onto the floor. Simple maintenance to fix the bolts prevented an unplanned shutdown that would likely have caused at least one hour of downtime, and tens of thousands Euro in lost production.
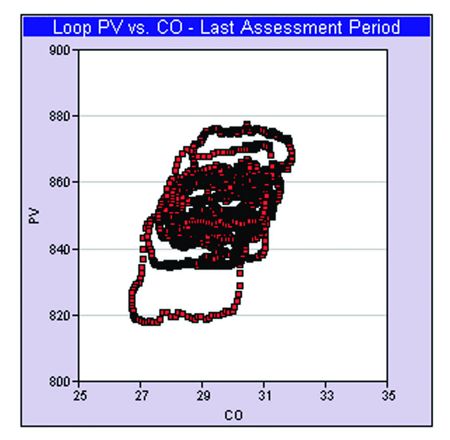
Detecting equipment failures
As with instruments and valves, there are known failure modes for other types of plant equipment. Vibration analysis of rotating equipment is one well-known form of condition monitoring. Other forms of detection are more specific to the type of equipment. Some proven examples include:
-
Detection of heat exchanger fouling by monitoring pressure drop
-
Detection of line plugging by tracking flow rate versus valve position
Condition monitoring software, such as ExperTune PlantTriage, automatically identifies the issue, prioritizes it, and delivers notifications to the right person.
It takes more than software and tools
Smart instruments, software tools, and diagnostic methods make a big difference. But they won’t have a lasting impact unless corrective actions are taken. It is especially important that the use of condition monitoring tools is integrated into daily operation and maintenance of the plant.
Sure, a single skilled person can use diagnostics to find and fix issues. But what happens when that person moves onto another assignment? Neles recommends developing a work flow process to integrate diagnostics and analysis into daily operation and maintenance. The work flow process identifies the specific reports and analytics to be viewed, who should view them, and most importantly, what actions must follow.
Daily, weekly, and shutdown preparation workflows should be developed for all areas of the plant. A one-time investment of time can pay off handsomely the first time a new failure is detected early.
Vendors offer deeper expertise about equipment lifecycle, failure modes, applications guidance, risk reduction, and maintenance/shutdown planning.
Vendor partnership
There is an increasing partnership between operating plants and equipment vendors. Vendors offer deeper expertise about equipment lifecycle, failure modes, application guidance, risk reduction, and maintenance/shutdown planning. As such, vendors are becoming more of a ‘reliability partner’ than simply an equipment supplier. Neles, for example, is offering shutdown planning services, via field service engineers trained not only in traditional repair techniques, but also trained and equipped with the latest digital tools and methodologies. These engineers are linked to a global network of instrument, valve, and control experts. Beyond the basics of maintenance, a full partnership may also include risk reduction via the management of spare parts, and by developing plans to replace obsolete equipment. Project management and follow-through can be accomplished in partnership with shared responsibilities.
Getting started
Fortunately, you can get started easily and quickly. The simplest and quickest approach is to complete a survey of existing data from smart instruments and positioners, and via asset management systems. This survey can be done with internal personnel, or with a vendor partner. Neles’ team, for example, will evaluate your full installed base of valves, as well as storeroom stocks, and help to develop a plan to reduce risks from reliability, obsolescence, and performance-related issues.
After a first-pass analysis, it is a natural step to continuously collect and analyse the data from your plant. For the best results, consider services based on software tools, customized to your specific plant situation. This lets you leverage plant personnel, reducing risk in the fastest manner.
Don’t wait – the digital age is here
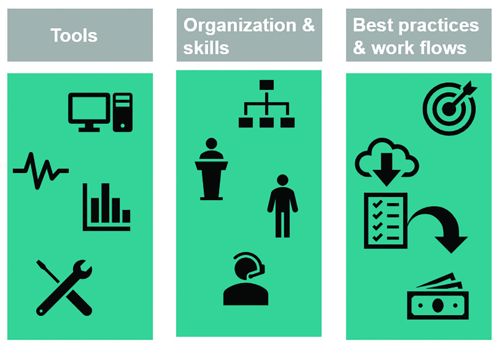
If your competitors are also analysing less than 1% of their data, you can develop a significant competitive advantage by spending a little time to get value from the data that you already have. Don’t wait to get started. No matter how old your plant may be, it is certain to have a large collection of under-used information that can be immediately used to improve reliability and reduce risk. The tools and methods are well-known and proven. From experience in hundreds of plants, one conclusion rings true: every plant has an opportunity for substantial gains.
Text by George Buckbee, Head of Performance Solutions, Neles.
Article originally published in Managing Aging Plants magazine March/April 2019 issue.
Text originally published in 2019, and slightly updated in April 2022, due to the company name change to Valmet.
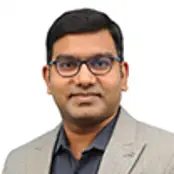
Ramakrishna Koti
Global Sales Manager, Control Performance
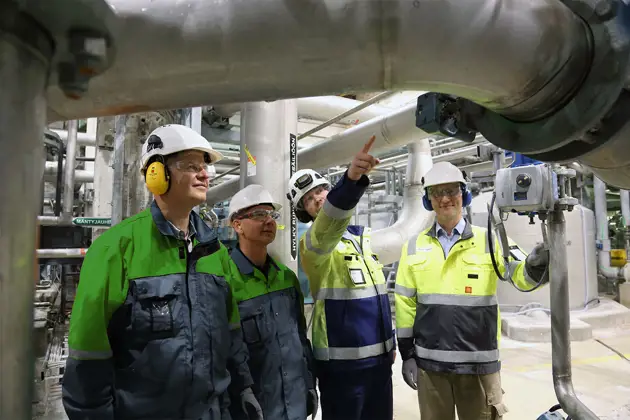
Subscribe to our newsletter
Subscribe now to flow control newsletter and receive the latest insights directly to your email.
SubscribeRead more about Neles' services and software