Valmet introduces a new environmentally efficient solution for starch cooking
As part of its climate program, Valmet is committed to developing new process technologies to enable 100 percent carbon neutral production for its customers by 2030. The latest example of Valmet’s sustainability-driven R&D is Enzymatic Starch Cooking ZE, a zero effluent solution that diminishes the carbon footprint of the starch cooking process while improving the operational reliability and quality of the process.
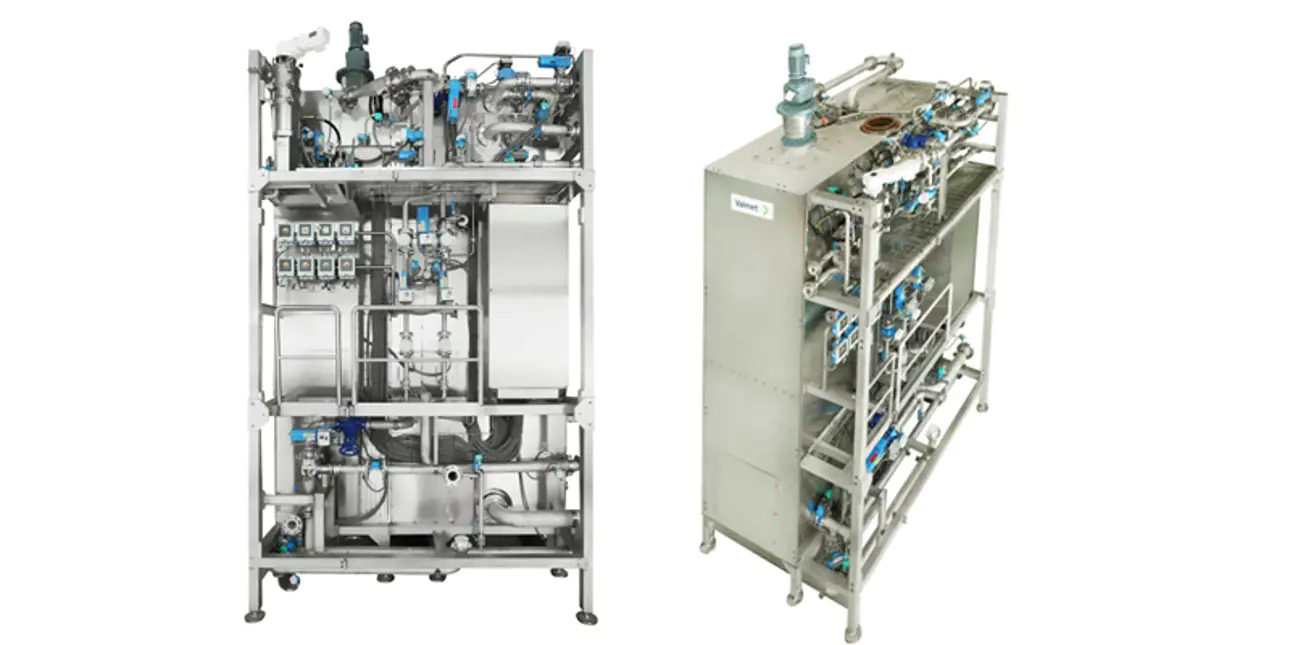
Compared to a conventional cooking system with one-way pipeline, Valmet’s Enzymatic Starch Cooking ZE offers a fully continuous operation with circulation loops. Even during normal production stops the system constantly circulates fresh, stable, and high-quality starch with an exceptionally wide capacity range of 20-120 tons of dry solids per day.
“Thanks to its improved design, our new starch cooking system has a smaller carbon footprint than the conventional system. It causes less wasted starch and utilizes the generated waste energy in its integrated hot water preparation. Our innovations are resulting in energy savings and decreased load and cost for water treatment – yet another step forward in improving the sustainability and cost-efficiency of our customers’ operations,” says Aapo Viiankorpi, Product Sales Manager, Board, Paper and Tissue Solutions, EMEA, Valmet.
Customer reports prominent results
Guangxi Jingui Pulp and Paper’s (GJPP) Qinzhou mill in China was the first customer to have the new Enzymatic Starch Cooking ZE installed. It was started up successfully in 2022 and has been operational since.
Among other benefits of Valmet’s solution, Lin Xiupeng, Chief of Paper Chemical Section at APP Guangxi Jingui Pulp and Paper is satisfied with the way it improves the mill’s sustainability targets.
Recycling hot water is in line with our targets for low carbon operations and the integrated design improves our field installation efficiency. It covers a smaller and more compact area than before, and the operation is easy to master,” Lin Xiupeng says.
Excellent news for those considering a starch cooking system rebuild
Engineering, installation, testing and startup of a conventional enzymatic cooking system can take months to complete, and the investment cost varies from EUR 0,5 to EUR 1 million. Valmet’s Enzymatic Starch Cooking ZE is a cost-effective and compact solution designed to fit into standard 40-feet sea containers.
“Compared to a conventional system, our solution comes with two preassembled and pretested skid units ready to be installed upon their arrival at the site. It has standardized dimensioning, engineering and software, leading to shorter installation time and a fast start up. Extensive support from our specialists guarantees peace of mind for the customer and added value for the investment,” Aapo Viiankorpi says.
Valmet Enzymatic Starch Cooking ZE |
|
Did you know this about starch in paper making? |
In paper and board making, native or modified starch is used at several stages of the production process: Wet end starch to control drainage and retention, surface size starch to increase strength and prevent dusting, and binder starch to bind pigments in the end-product. During the cooking process, starch reaches its desired properties such as viscosity and solids content. |