White liquor oxidation system
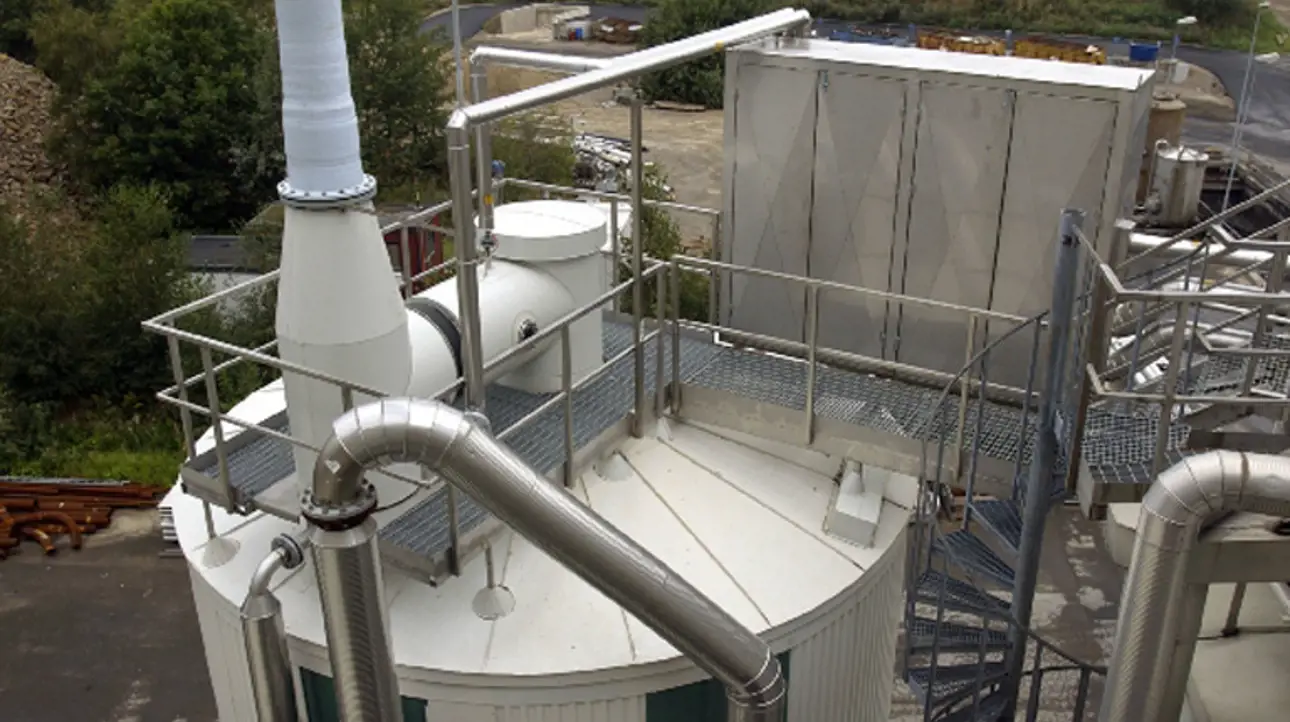
The purpose of white liquor oxidation is to improve the Na/S balance of the Kraft process by replacing make-up caustic with internally generated alkali. Valmet offers two well-proven and efficient alternatives, an air-based oxidation system for the production of partially oxidized white liquor for oxygen delignification and an oxygen-based system for the production of fully oxidized white liquor for bleaching and oxygen delignification. Oxidized white liquor can also be applied for many gas scrubbing applications.
Air-based system
With the air-based system, oxidation takes place in a multi-stage reactor. The air is fed to the reactors from a rotary air blower. Primarily, partial oxidation takes place and the sulfide is converted into thiosulfate. The cost of operation is low as atmospheric air is used to supply the required oxygen. This process is highly suitable if the main target is the elimination of sulfide.
Sulfide conversion to thiosulfate: 97-98%.
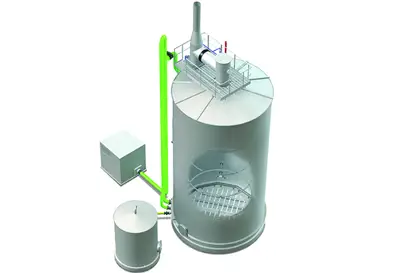
Oxygen based system
In the oxygen-based process, oxidation is carried out in pressurized loop reactors. High-efficiency jet mixers secure that the liquid phase is saturated with oxygen at all times.
This technology provides a good environment for a high reaction rate for the conversion of sulfide to sulfate – an inert compound that will not be further oxidized in downstream processes.
Sulfide conversion into thiosulfate: 98–99%
Sulfide conversion into sulfate: up to 60%
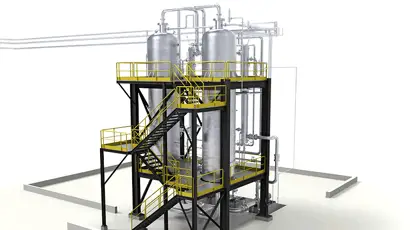

Our expertise is at your service
Our focus is to bring your performance forward utilizing our extensive experience and in-depth knowledge of pulp process technology. Get in touch with our experts through your local Valmet office, or the link below.
Contact us