Trouble-free production at Burgo’s Verzuolo paper mill
Remote condition analysis with Valmet’s expert services has proved an invaluable tool for achieving trouble-free production at Burgo’s Verzuolo paper mill in Italy.
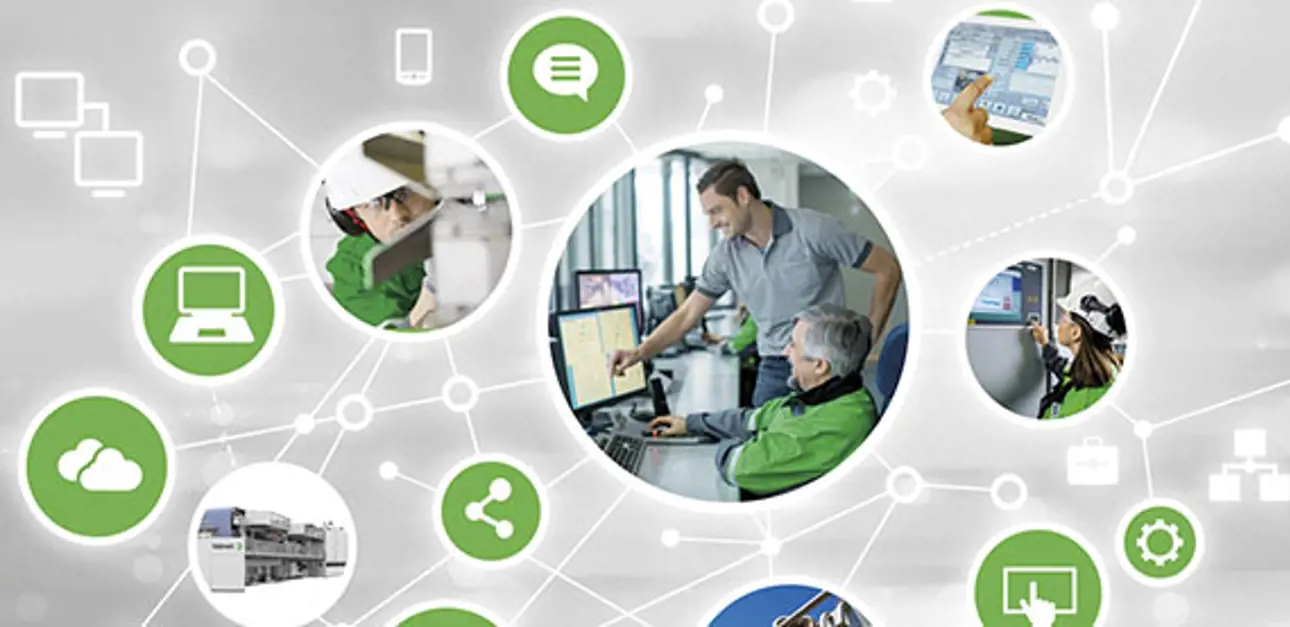
Burgo Verzuolo’s paper machine PM 9 is equipped with full scope control and quality systems automation to help monitor machine condition. In addition to the system, the mill utilizes a condition analysis service contract with Valmet to receive expert appraisals of the machine’s vibration conditions. Andreas Nuesse, a Valmet vibration specialist located a thousand kilometers from the mill in Dörpen, Germany, uses a remote connection to examine machine conditions and prepare a regular report for the mill.
An expert analysis allows time to plan, order spare parts if necessary and avoid unplanned downtime.
Tool for predictive maintenance
Condition monitoring, which covers mechanical condition measurement and the performance of machines based on vibration measurements as well as other machine parameters from the Valmet DNA Process Automation System, is an essential tool for the mill’s predictive maintenance. While the mill has access to the various tools the system provides, expert vibration analysis is a very skilled function, requiring both extensive training and experience. Freed from the day-to-day maintenance activities at the mill, Nuesse can focus on examining trends or other changes in the vibration spectra the system measures and advise the mill of where to focus maintenance resources. If he finds a problem, his expert analysis allows time to plan, order spare parts if necessary and avoid unplanned downtime.
Burgo Verzuolo mill: Valmet expert services via Industrial Internet
Advance alerts
There are also occasions when a system alarm alerts the mill to a problem which requires immediate expert analysis. Recently, a dryer cylinder vibration raised concern, and at the mill’s request Nuesse was able to remotely examine the situation and give advice about the severity of the problem. His investigation showed that the bearing would not last until the next scheduled shutdown, and the mill was able to take earlier action and avoid a complete bearing failure.
Nuesse has also been able to alert the mill to problems before they emerge: during one regular check, a severe imbalance at the second press (more than 20 mm/s and getting worse) made it necessary to contact the mill urgently. The machine was stopped immediately, and several loose screws, some of which were completely missing, were discovered on a cardan shaft. The mill’s quick response to the warning avoided both serious damage and a longer unplanned shutdown.
Article published in Forward magazine 1/2019.
Related articles