Stora Enso Veitsiluoto extended their roll change intervals on coating stations using Valmet Coater Roll Cover CC
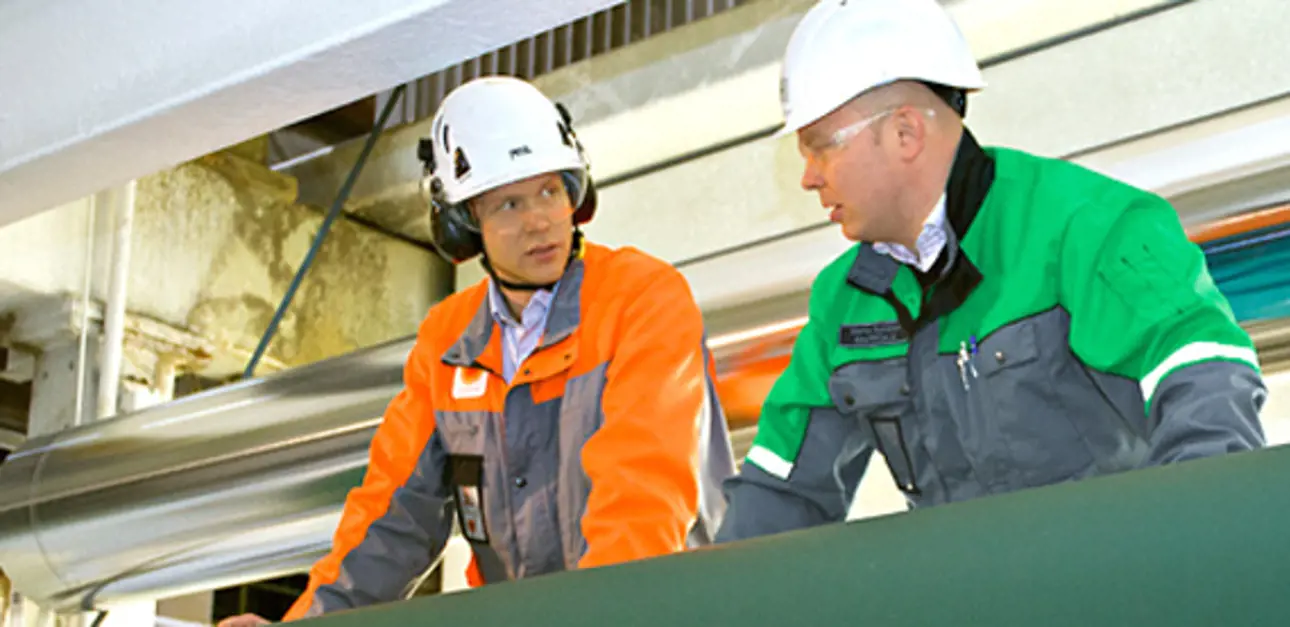
“Within a year, we have managed to eliminate about five roll changes and grindings,” says Janne Harjuniemi, Veitsiluoto mill. Valmet’s (until December 2013 Metso Paper) Marko Nykänen on the right.
Blade coating requires a lot of the backing roll cover. It needs to be very homogeneous to achieve a flawless coated paper surface. The cover has to be evenly hard and rough across the entire roll width. It also needs to be easy to clean and wear-resistant in order to maintain good coating profiles during long operating cycles. Usually, backing rolls must be changed when the coating profiles of the blade coating station no longer meet the set paper quality requirements.
Today, hard-coated coater blades are mostly used on blade coating stations, with the advantages of better runnability, better paper profiles, and a longer useful life. The downside is wear of the backing roll cover. Problems usually appear at the edges where the roll cover and the blade meet.
This happened at Stora Enso Veitsiluoto PM 1 in Finland, a paper machine producing 180,000 tonnes of coated printing paper per year. The line includes an offline coater with four blade coating stations.
“The backing roll change interval was quite short, no more than 4–6 weeks, on the blade coating stations due to wear at the cover edges,” says Markku Åman, Production Manager.
The hard-coated coater blades wore the cover edge very quickly. The situation varied between stations and was worst on the first and fourth stations.
A solution was sought using Valmet’s (until December 2013 Metso Paper) new Valmet Coater Roll Cover CC polyurethane cover, designed for all blade coating stations. It is particularly well suited for coaters that use hard-coated coater blades. Valmet is the first cover manufacturer to supply a polyurethane cover for this application.
Wear- and marking-resistant
With the new polyurethane material and mixture, Valmet Coater Roll Cover CC* resists wear and marking much better than conventional roll covers. As a result, it can be used on the machine much longer, considerably reducing the need for roll changes. With online coating in particular, the difference is significant as roll changes can be scheduled according to other shutdown needs on the line.
During web breaks, covers are often locally subjected to strong forces that may cause dents in them. The polyurethane material has excellent strength properties, enabling it to resist even heavy local impacts without any marking. The amount of material removed during grinding is also reduced, extending the overall useful life of the cover.
Excellent results led to a second order by Stora Enso Veitsiluoto mill
At Stora Enso Veitsiluoto PM 1, the first experiences of the new Valmet Coater Roll Cover CC have been excellent. For the first operating cycle, continuous operation for 15 weeks was set as the objective for the fourth station. During this time, the cover was hardly worn at all, so the cycle was extended to 24 weeks. Runnability and coating profiles remained good for the whole period.
During grinding, only 0.4 millimeters of material was removed from the diameter, which is considerably less than normal. During the second operating cycle, the cover has been in use on the first station for 20 weeks already. The Veitsiluoto mill has been very satisfied with the results.
“The roll change interval on the most problematic stations has been extended from the initial situation without any detrimental impact on runnability or profiles,” says Janne Harjuniemi, Operations Manager. “Within a year, we have managed to eliminate about five roll changes and grindings, which has led us to acquire a second Valmet Coater Roll Cover CC for the line.”
*earlier known as CoteCondor. Article published in Results customer magazine 2/2013.