Valmet Dryer Fabric Cleaner maximizes fabric lifetime at Palm Wörth in Germany
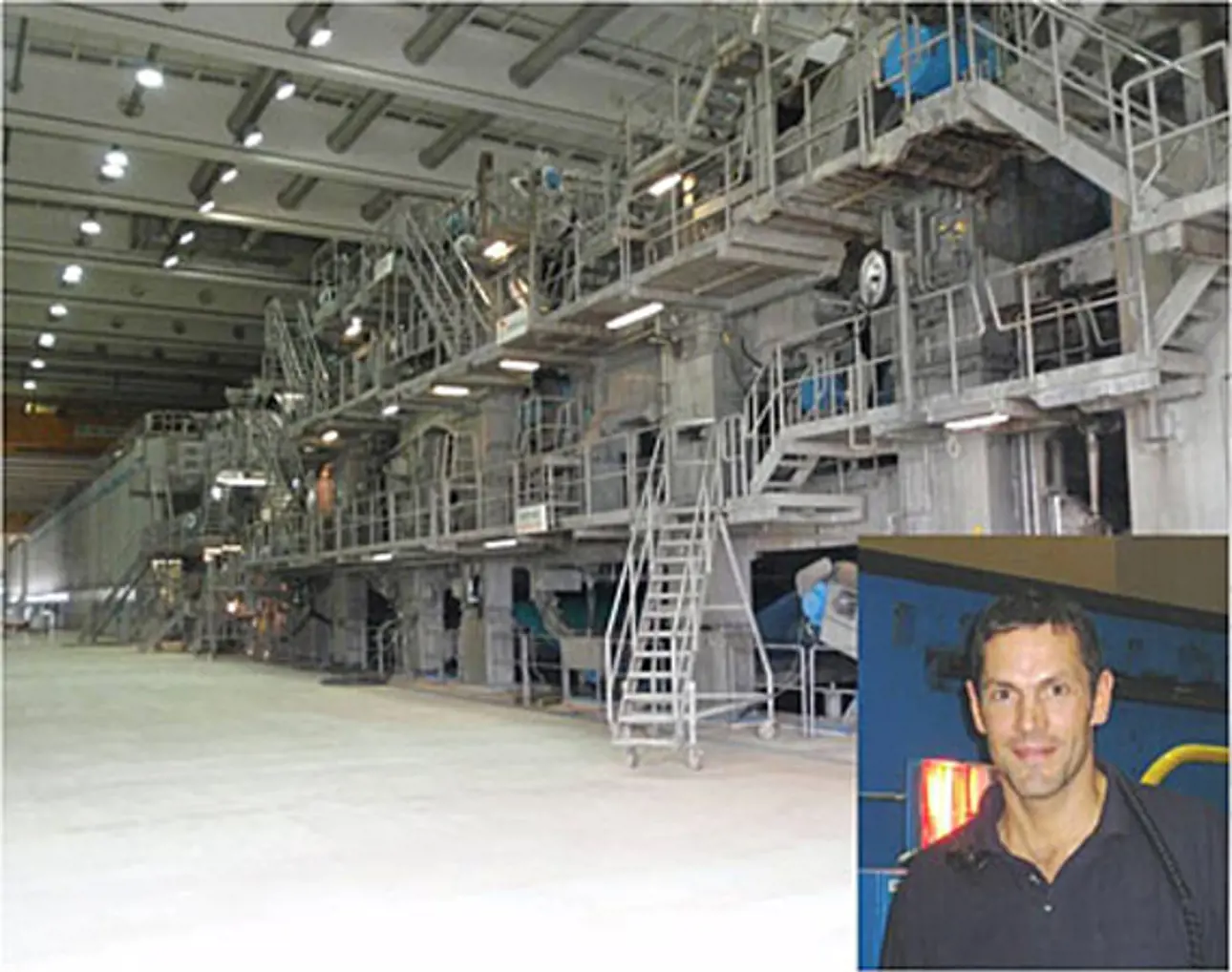
The cleanliness of the dryer fabrics has a significant effect on the production efficiency. This is generally seen as a reduced number of breaks, dryer section energy savings, and improved paper or board quality. This is also a fact at Palm Wörth PM 6 after the installation of Valmet Dryer Fabric Cleaner.
Effective cleaning operation
Valmet Dryer Fabric Cleaner (former OptiCleanerPro) enables continuous or intermittent cleaning operation during production. It cleans the fabric on the paper sheet side with a high pressure water jet coming out of the cross-machine traversing cleaning head. Water mist and dirt are removed by means of an air curtain and vacuum. An air comb blows the cleaning mist out of the fabric to prevent wet streaks on the paper sheet.
A cleaner removes dirt through a high-velocity air flow inside the cleaning head generated by a vacuum unit. Detached dirt and water mist are conveyed through a pipeline to a cyclone separator in a vacuum unit where heavy particles are separated from the air and directed to a container or sewer. The cleaning head, outlet pipeline and cyclone separator are flushed after a set of cross machine cleaning sequences.
![]() |
Valmet Dryer Fabric Cleaner effectively removes dirt from the fabric due to the cleaning head’s optimal design and high-velocity air flow generated by a vacuum unit. The daily maintenance need is minimal. Replacement of the nozzle housing is easy and fast with quick couplings. |
![]() |
Thanks to the Valmet Dryer Fabric Cleaner, the permeability has remained on a very good level at Palm Wörth PM 6.
|
Less daily maintenance
Dirt is conveyed freely and efficiently through an outlet pipeline out of the machine to a cyclone separator. There is no save-all or other components that require extra cleaning or maintenance work. This will reduce the need for daily maintenance and permits break-free operation of the cleaner.
The number of nozzles installed in the cleaning head can be selected separately for each application. The width of the area cleaned by the high-pressure showers depends on the number and type of the nozzles. Replacement of the nozzle housing is easy and fast with quick couplings.
The cleaning head is washed automatically at the washing station that is located normally on the tending side inside the hood. Duration of the washing sequence can be adjusted. In addition, nozzle body replacement, testing of new nozzle body and checking of vacuum level can be done when the cleaning head is at the washing station.
Combine with regular service
Service at regular intervals ensures the break-free operation of the cleaner, machine runnability and good end-product quality. Valmet offers a maintenance service agreement which includes scheduled service visits combined with fabric inspection and measurements. Follow-up through remote control is also possible.
Excellent cleaning results at Palm Wörth
Dryer fabric cleaner was installed in April 2010 at the 10th dryer group of the 11-m-wide Palm Wörth PM 6 in Germany, to ensure proper cleaning of the fabric. The cleaner works well with all grades and keeps fabric permeability at the desired, optimal level. Thanks to this, fabric lifetime and service intervals are longer, which gives cost savings.
The crew of PM 6 is impressed with the air comb because it enhances the cleaning effect. They are also content with the fact that the cleaner is connected to a separate vacuum unit. This is a better option than connecting the cleaner to the wet end vacuum system, which is typical with conventional cleaner solutions. The cleaner starts automatically by default. This feature was requested by the customer. “We are overall very satisfied with the OptiCleaner Pro dryer fabric cleaner,” says Jürgen Kosse, Mill Manager for Palm Wörth.