The new normal – the opportunities of digitalization in industrial maintenance
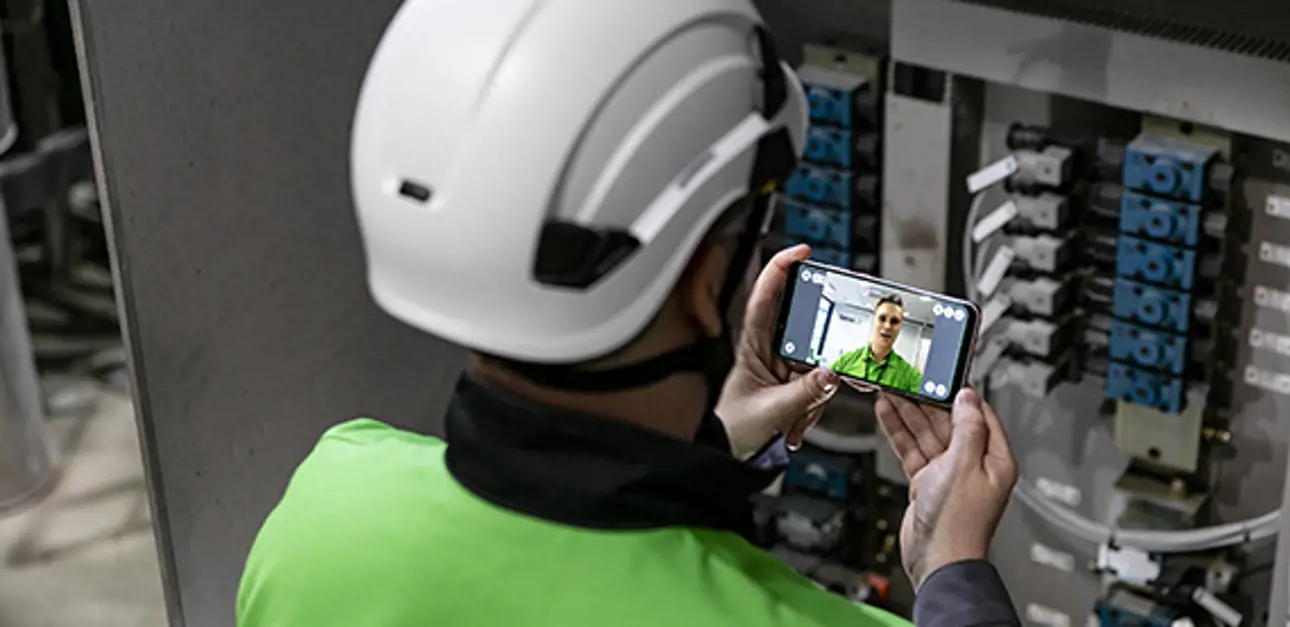
It has been said that exceptional circumstances and crisis situations strengthen certain trends and weaken others. The COVID-19 pandemic means that now more than ever, digitalization is a trend that is here to stay in working life. An everyday example of this is the numerous virtual meetings that follow each other during what is now a normal workday.
Maintenance visits in the digital era benefit from new tools and knowledge sharing
Digitalization, mobile applications and the Industrial Internet also impact industrial maintenance work. Let’s look at an example.
A mechanical or process failure in the customer’s production line appears. Thanks to the increasing number of smart sensors and the connectivity of industrial equipment and processes, maintenance experts can monitor and analyze real-time data remotely with the customer or a wider network of experts, and only then decide on the need to travel to the site. And even if it is decided to do so, the problem can be specified in more detail, and virtual reality (VR) applications can even help the maintenance expert study the situation in advance. With mobile tools, documents and reports can be made available to all parties in real time via a collaboration space (customer portal).
And the possibilities won’t stop there: autonomous robotics such as drones are already being tested at industrial sites with challenging or limited access, for example.
The benefits to the customer are obvious: A wide network of experts is available for support, regardless of location and time zone; service is faster and more transparent; and costs are optimized, because the maintenance need can be defined in more detail. And this is the case for the maintenance experts as well: Resourcing can be optimized; the need for travel decreases; work becomes more flexible; safety improves; and the information for completing the work is more easily available.
Continuous learning – and in an environment closer to reality
Managing and knowing all of the above require new types of skills of both the service supplier and customers. Of course, with new maintenance employees entering the field, digitalization and its uses have already been taken into account in the basic training. However, a lot of learning on the job and training offered alongside the work is also needed. At Valmet, an example of this is the maintenance technician’s certification training, which improves the preparedness to work with maintenance tasks in a digital environment.
But digitalization is also affecting how training is offered. Various possibilities offered by virtual reality and simulator training options offer the chance to increasingly operate in an environment that corresponds to the reality during maintenance training in the future. This also enables creating an inspiring learning environment with varied exercises. The same learning environment works equally well, e.g., for the maintenance work supervisor, supplier and the production plant’s maintenance personnel. So, learning can also be fun!
The “new normal” is here to stay – I will now continue my day by taking a virtual coffee break with my colleagues!
Related reading