Cogeneration for increased energy efficiency
Tissue manufacturing involves extremely intensive activities, demanding vast quantities of electrical and thermal energy. Consequently, any solution that optimizes the use of these resources is of utmost importance from both economic and environmental standpoints.
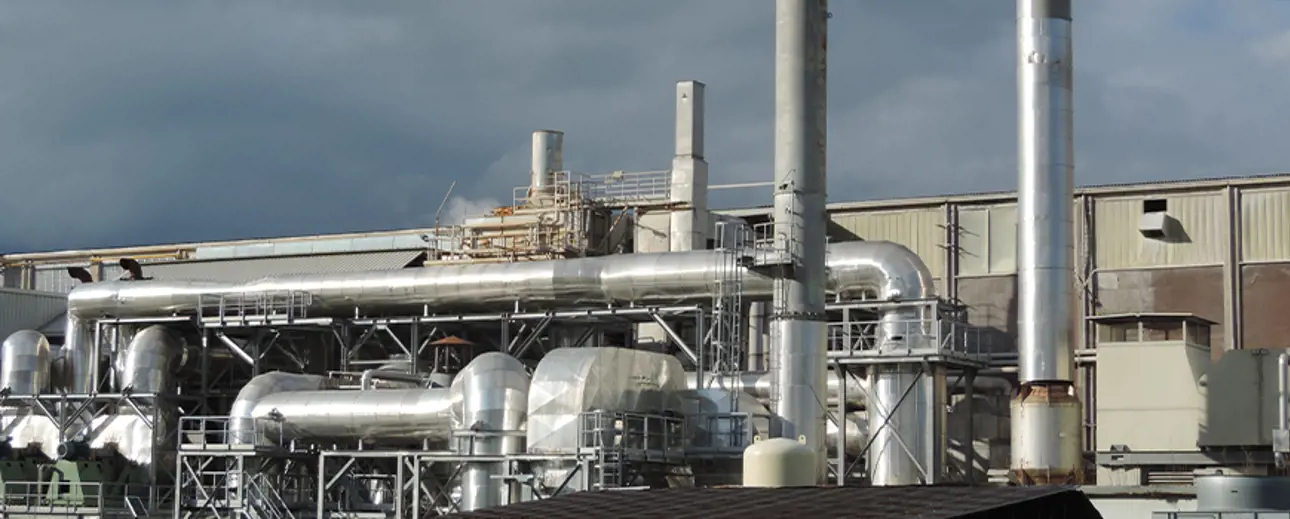
On average, up to about 70% of the total energy required during tissue manufacturing is thermal energy (in the form of steam) used by the Yankee cylinder and natural gas used by the Yankee hood (as fuel for its burners). For this reason, cogeneration systems – those that simultaneously produce electricity and heat – have become the standard technology in the industry.
A cogeneration system consists of a main engine – normally, a gas turbine or an internal combustion engine – connected directly to an electrical power-generating unit, and whose exhaust is fed into a heat recovery system. The heat recovery system is traditionally comprised of a waste heat steam generator (WHSG) and air/water heat exchangers. For systems using gas turbines, engineers at Valmet have developed a cogeneration system that takes advantage of another opportunity: the direct use of exhaust fumes to dry tissue.
Minimizing system weaknesses
As mentioned, the main engine of a cogeneration system is either a gas turbine or an internal combustion engine. The selection of which has a remarkable impact on the configuration, feasibility and economics of the system.
Gas turbines are less efficient at producing electricity (only 30–35% for larger size turbines), compared to internal combustion motors (45–50%). This means that the same amount of gas used by a motor generates more electricity. The downside of motors is that their steam production capacity is diminished.
A small tissue machine with a production up to 100 tons per day will use about 5 tons of steam per hour (t/h), whereas the electrical consumption of the whole production line, including ancillary equipment, is around 4.5 MW.
Nearly all gas turbine-based cogeneration systems producing electricity within a 3–7 MW range generate a surplus of steam, compared to system requirements. In comparison, internal combustion motors that generate electricity within a similar range will not produce enough steam for the tissue machine.
Conventional cogeneration system
Maximizing system strengths
Despite their less-efficient electrical production, gas turbines produce exhaust fumes of higher flow and temperature. These fumes are extremely clean and do not contain lubricant oil traces, as is the case with exhaust from an internal combustion engine. Moreover, the fumes exit the gas turbine within the temperature range normally used in high-velocity drying hoods.
A cogeneration system uses the exhaust from a gas turbine in the drying process, producing a higher global yield of steam, while simultaneously decreasing energy needs. The exhaust first goes through a plenum, which acts as a settling chamber to stabilize the turbine pulsations if necessary. The exhaust is then blown directly into the Yankee hood. Unused exhaust is redirected to a mixer, and together with the hood exhaust, transferred to a Waste Heat Steam Generator (WHSG).
The plenum/mixer combination is like a bypass, only blowing necessary exhaust to the hood, without dissipating the unused exhaust, which is still rich in thermal energy. The WHSG is equipped with a modulating bypass, making the higher temperature exhaust available for further heat recovery processes, if unused by the steam generator.
Valmet Advantage ReGen Flow Diagram
Finding the best solution
Choosing the right engine is critical for overall mill efficiency and success. Subsequently, identifying the correct electrical and thermal needs of the system is essential.
With focused audits – with particular focus on the press, Yankee dryer and hood – the requirements of every single production type can be precisely determined. With dedicated software, the operation of every new system can then be optimized.
Over the years, Valmet has developed the expertise to carry out dedicated feasibility studies and apply the best configuration to every new cogeneration system. To date, it has delivered and installed a total of almost 20 cogeneration systems worldwide.
For more information on Advanced ReGen Cogeneration systems, contact Valmet.
Article publisher: Paolo DellaNegra
Category: Operations
Industry level: Introductory
Est. read time: 6 minutes
Summary: This article takes a look at how hybrid tissue machine technology has offered different types of benefits to different types of tissue mills in different markets.