Sappi Kirkniemi taps into a new fuel opportunity
A side stream from oil refineries - asphaltene - is now a cost-effective fuel at the power plant at the Sappi Kirkniemi mill in Finland. The high fuel flexibility of Valmet CFB Boiler plays a key role in this outstanding example of a circular economy.
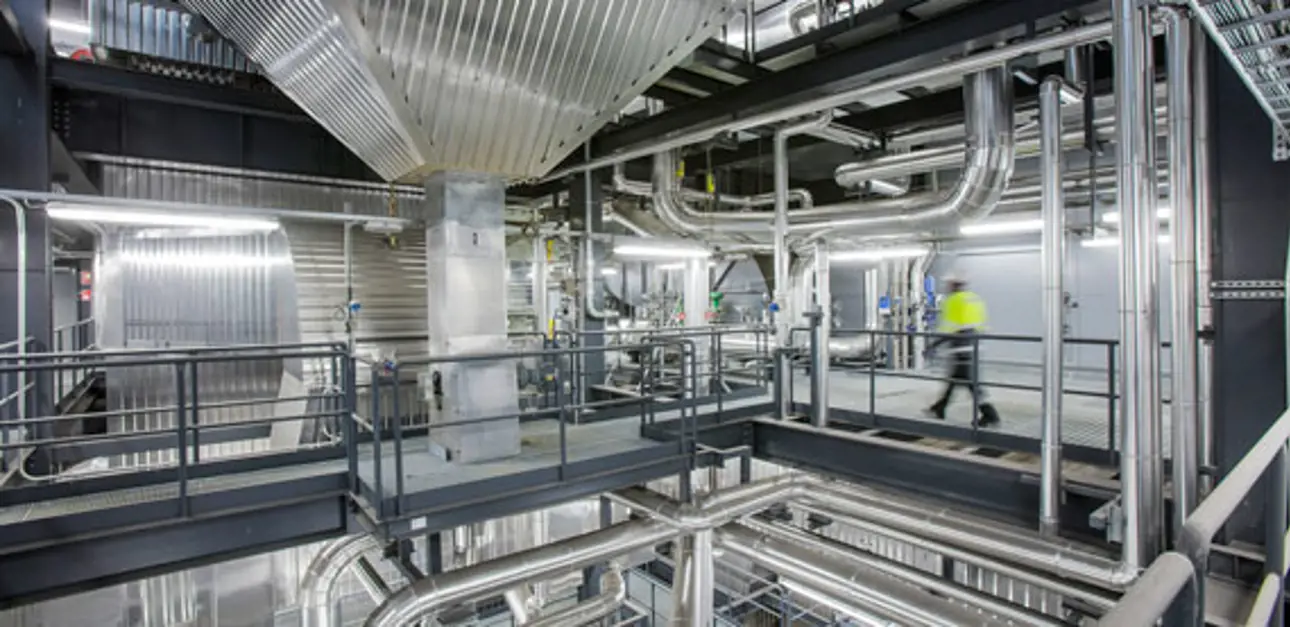
Most people have probably never heard of asphaltene, a side stream of the oil refining process classified as a fossil fuel. The liquid stream can be treated to become a solid form and ground into different size fractions to be used in energy production.
“We were approached by Neste’s oil refinery plant in Porvoo and asked whether we would be interested in a new fuel that might bring cost savings. The refinery has new processes in which it produces cleaner diesel fuel than ever, and asphaltene is a totally new reject from them. And yes, we were interested – as we always are – in finding new ways to improve cost efficiency,” says Kalevi Merinen, Power Plant Manager, Sappi Kirkniemi Mill.
Prior to this contact, Neste and Valmet had carried out combustion trials with asphaltene at Valmet’s R&D Center in Tampere for Neste’s new Kilpilahti combined heat and power plant.
Multifuel boiler plays a key role
In 2014–15, Valmet delivered a CFB Boiler (CYMIC at the time), featuring circulating fluidized bed (CFB) technology, to the Kirkniemi power plant. The multi-fuel boiler can flexibly use solid fuels such as coal, bark from the mill's debarking process and other wood-based fuels. The delivery also included Valmet’s solution for dry flue gas cleaning, the GASCON bag house filter.
“After being contacted by Neste, we wanted to verify the usability of the fuel. We commissioned Valmet’s R&D department to investigate how high the share of asphaltene would act in our fuel mix,” Merinen recalls. Valmet’s study showed that the share could be as high as 30%. “These results convinced us, and we continued our discussions with Neste. We also got the green light from our management for an investment that was needed to enable the combustion of asphaltene,” he continues.
The investment covered a new opening in the boiler and new conveyors. Valmet was awarded the contract over adding the opening with its air and water cooling, as well as commissioning and supervision. “The fuel is so exotic that we wanted to ensure safe commissioning with Valmet’s professionals,” Merinen adds.
No fouling at all
The new fuel was taken into use at the plant in November 2017. It has partly replaced the use of pulverized coal and currently accounts for the maximum allowed share – 30% – in the fuel mix. The rest continues to be made up of coal.
Recently, Finland’s Minister of the Environment proposed that Finland should move its ban on coal-burning for power from 2030, as agreed, to an earlier date of 2025. “If and when this happens, we will be able to use biofuels purely in our boiler. Asphaltene can be combusted with them, too,” Merinen points out.
“Asphaltene seems to suit the boiler perfectly. It burns very well. There is no fouling, although you would actually expect it, as the fuel is sticky and oil-based,” says Kalevi Merinen, Power Plant Manager at the Sappi Kirkniemi mill.
To date, the plant’s experience with this new opportunity fuel has been very positive.
“Asphaltene seems to suit the boiler perfectly. It combusts very well. There is no fouling, although you would actually expect it, as the fuel is sticky and oil-based. After running the boiler for one month with the new fuel, we checked the inside during our Christmas shutdown and found it to be perfectly clean. There were no visible signs of having combusted asphaltene,” Merinen says.
Emissions well under control
What about emissions, since asphaltene contains significantly more sulfur than coal? According to Merinen, NOx levels have risen somewhat, resulting in an increased need of chemicals.
“Valmet’s Selective Non-Catalytic Reduction (SNCR) system performs well and has sufficient capacity so that we are able to control our emissions and stay well under the tight emission limits.”
The plant has calculated the return on investment to be relatively short. “The investment and the combustion of asphaltene have been an economically rational decision. We wanted to increase the plant’s cost efficiency, and this solution helps us achieve it,” Merinen emphasizes.
In the future, Sappi Kirkniemi plans to keep the asphaltene share at 30% of its energy production.
Valmet has delivered a Valmet CFB Boiler featuring circulating fluidized bed (CFB) technology to the Kirkniemi power plant. This multi-fuel boiler can flexibly use solid fuels. The delivery also included Valmet's solution for dry flue gas cleaning, the GASCON baghouse filter.
Related articles