Nine days without a break
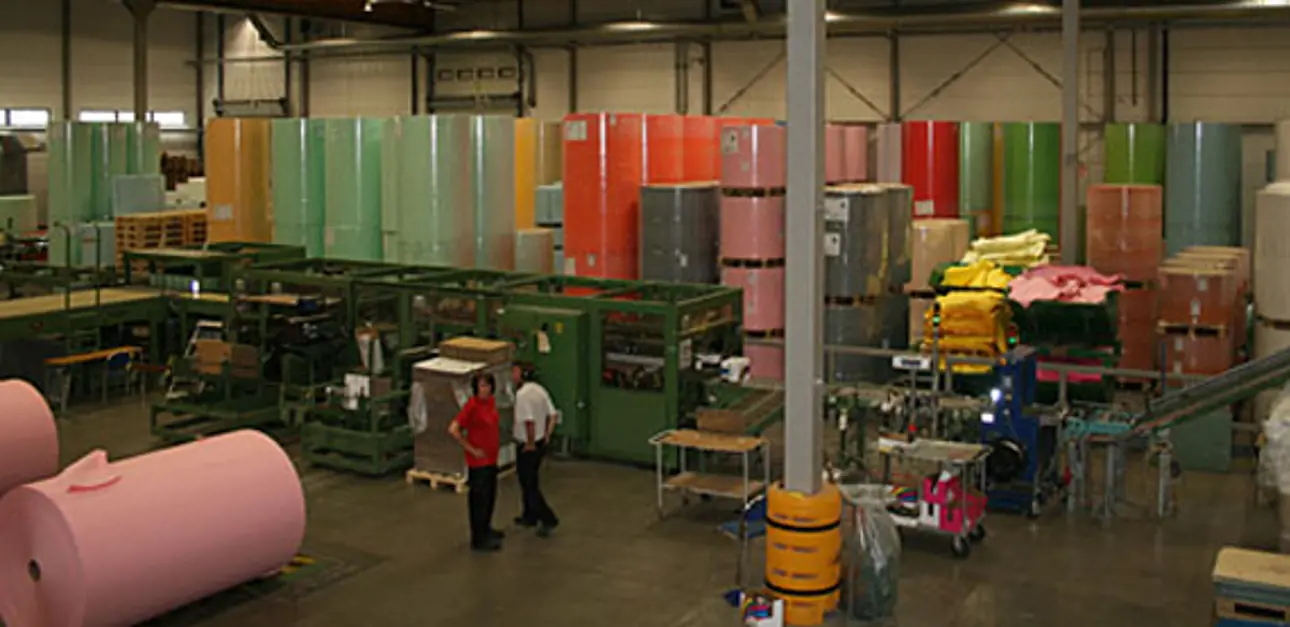
When Production Manager Öistein Vedahl of Lessebo Bruk realized they had a screening problem on PM 2 he contacted Valmet for a solution. “Customers were complaining of colored fibers in our superior white paper and threatening to change suppliers. When we opened up the headbox and screens and saw the condition, something had to be done. I am happy to say that with Valmet’s screening solution our customers are really satisfied with our quality, and breaks due to poor screening are a thing of the past.”
One screen basket to replace four!
The headbox approach used two machine screens in parallel, and when opened mill personnel could see that the baskets were worn out and full of pulp spinnings (strings). This was definitely the cause of the quality problems. The screens were strainer types, equipped with two milled hole baskets (an outer basket and inner basket). This meant they had a total of four screen baskets to replace. On advice from Valmet, the mill decided to idle one screen and rebuild the other with just one wedge wire screening basket. This was made possible by the use of Valmet’s Nimax LD wedge wires in the screening basket. With conventional wedge wires and milled hole baskets, the narrow slot size or hole size needed to guarantee the accept pulp quality leads to an increased pressure drop over the screen basket and can require two or more screens in parallel to achieve the desired screening efficiency. The patented Nimax LD (Laminar Design) wedge wire reduces the pressure drop by optimizing the flow at the screen boundary layer as well as reducing flow resistance through the slots and the following accept channel. The result is high screening efficiency, reduced stringing or spinning and excellent runnability.
Production Manager Öistein Vedahl is very happy with the screen rebuild. Customer complaints are down and quality is up.
The rebuilt screen with Nimax LD wires in the outer basket and a blind metal plate replacing the inner basket was started in May 2013. “No problems have occurred with screening since start-up,” says Öistein Vedahl. “After two months we have fewer breaks than ever and production is at record levels with no more colored spots in our superior white grade. From having 2 to 3 breaks per day, we recently achieved a record run of 9 days without a single break. We are now thinking of a similar rebuild of the other basket, now idle, for use in another position.”
For Valmet's screening specialists the results are no surprise, “We have seen this kind of a result in many mills. Lessebo Bruk can count the return on investment in terms of days, not months.” Vedahl is in agreement. “The main issue,” he adds, “is that for our customers, the quality is better than before and we have fewer breaks.” In addition to the quality improvement and the substantial reduction in breaks, other savings will soon be evident: “In addition to better paper machine runnability, there are energy savings and less maintenance, because the second screen can be shut down. There are also fewer wearing parts, as there is now only one basket instead of four.”
The Lessebo Mill is located in a densely forested area between large shallow lakes in the inland region of Småland, southern Sweden. The mill has a long history of paper production going back to 1693, and today Lessebo Bruk is completely focused on forest based products, with a modern product mix of graphical papers, dissolving cellulose and energy. |