Complete control of energy and air flows
Valmet process ventilation for board and paper machines
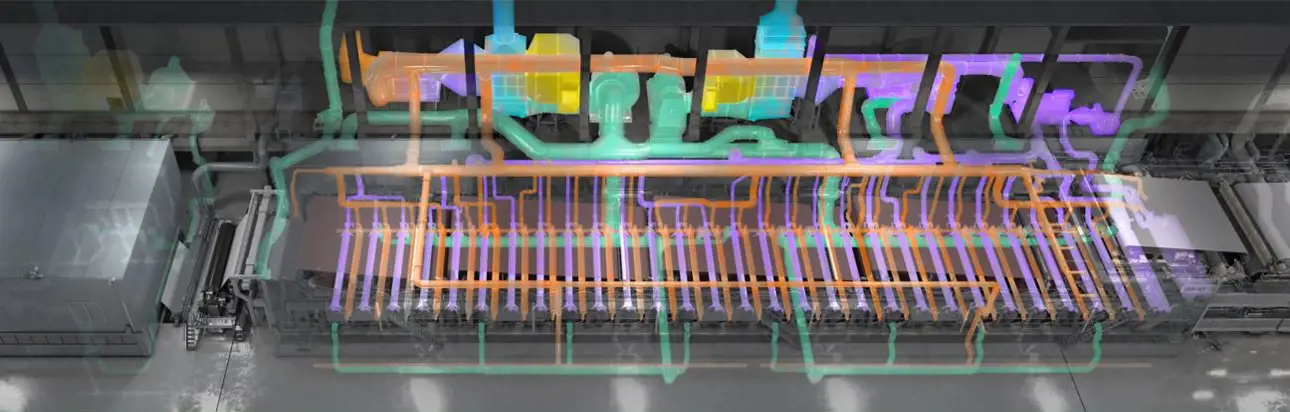
Valmet’s family of paper machine ventilation processes and products goes under one name – OptiAir. The OptiAir family is a complete energy-efficient set-up for paper and board machine process ventilation. The family consists of the OptiAir Hood, OptiAir Recovery and OptiAir Environment processes and products.
Energy efficiency is your key to improved productivity
In paper and board making processes, resources such as raw materials, water and energy, must be used in a more efficient way than today. A spotlight has been put on energy consumption – energy will continue to be a significant factor, influencing overall production costs. Any improvement in decreasing energy consumption will immediately pay back as a more profitable operation and decreased CO2 emissions. OptiAir process ventilation solutions provide excellent opportunities for reducing costs and increasing the profitability, of both new and old machines.
Air systems can reduce energy consumption significantly by:
- efficient and minimized heat and electricity use in air systems
- affecting the energy consumption of cylinder dryers
- decreasing the use of primary energy through heat recovery systems
The energy used in the paper drying and evaporation process is bound in the exhaust air. After that, the process ventilation and heat recovery functions practically define the total energy efficiency of the machine.
Once a huge amount of energy has been used for drying, the energy doesn’t disappear. The energy in the steam used in the cylinders is released by condensing the steam. Then this energy is transferred through the cylinder cell into the paper sheet. The steam energy will be bound in the evaporated water and finally all the evaporated water with energy from the steam will be in our exhaust air. Actually, we have more energy in the exhaust system than in the steam flow into the cylinders, because there is already quite a lot of energy in the incoming supply air flow. In a modern paper or board machine, over 50 MW of heat can be recovered. It is important to utilize this energy efficiently.
Significant energy content exists not only in the dryer section but also in other process exhausts such as the vacuum system exhaust and the exhaust air of coating dryers. In practice, there is enough energy in the process exhausts for all water and process air heating. Machine hall heating in cold regions can be also done with this secondary energy.
From the results of energy analyses, we can separate out the various actions and their impact on steam consumption.
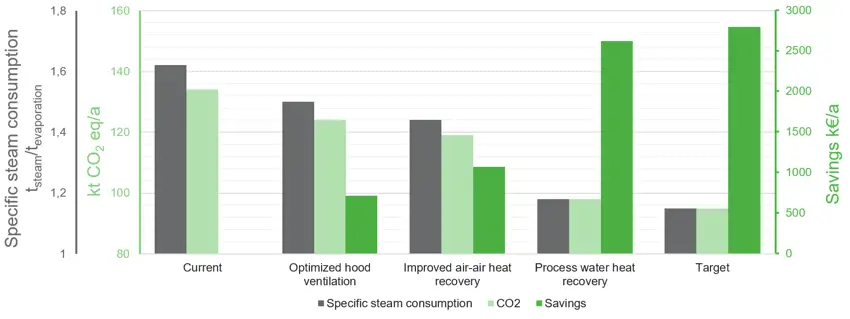
OptiAir process ventilation offers complete control of energy and air flows in the paper and board machines.
Less energy, more production, better quality
Global targets have been set for energy saving, the reduction of carbon dioxide and better energy efficiency. Energy is also one of the biggest costs in paper and board making, but we have good news for paper makers! There is still a lot of potential for saving energy.
Process ventilation systems provide exciting new opportunities for reducing costs and carbon footprint and increasing profitability. However, these opportunities need to be investigated – simply because the systems are running, making paper, do not assume that they are running efficiently. You have to look for the opportunities, they are there!
We invite you to reduce your energy footprint step by step!
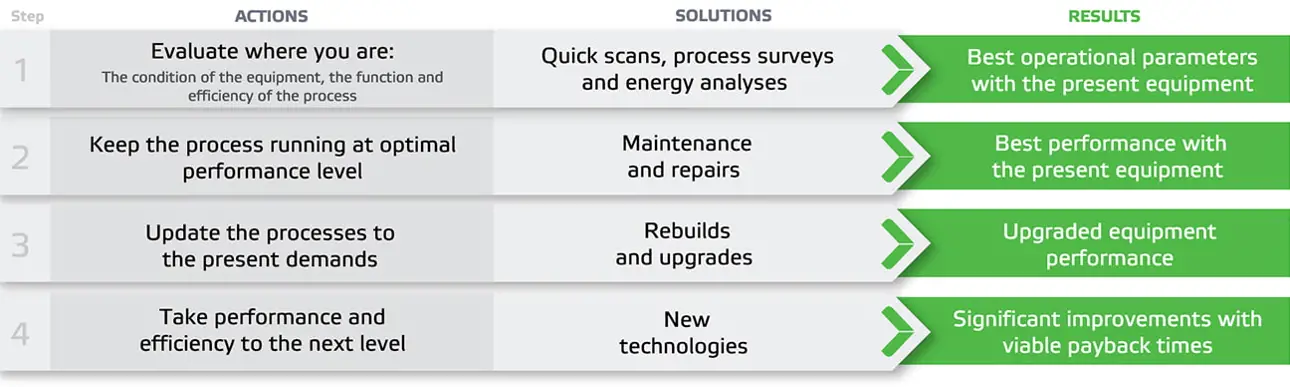
Air systems energy efficiency improvements
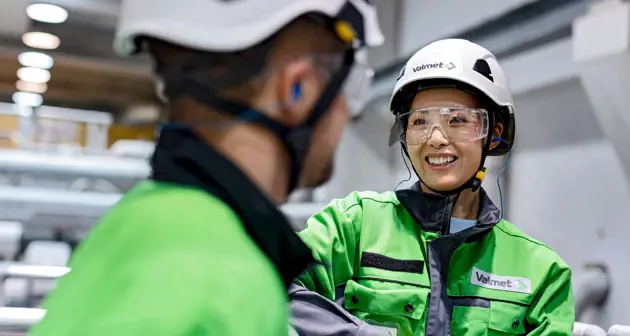
Want to talk to our process ventilation experts?
If you wish to get further information like technical specifications, need a quotation, or wish to discuss different solutions, fill in the contact form and our experts will contact you shortly.
Contact our experts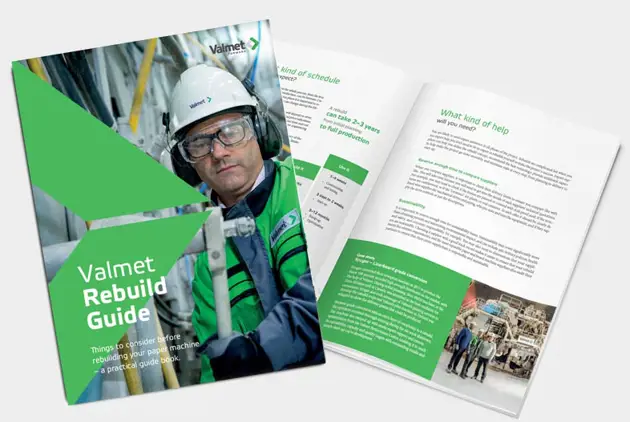
How do you plan a successful rebuild?
Rebuilding a paper or board machine can improve the competitiveness of your business and your processes. But where do you start? Download our e-book to learn how to develop a winning rebuild concept, how to minimize rebuild related risks, and how to ensure smooth ramp up to full production.
Download e-bookExplore our latest board and paper press releases
- Jun 13, 2025Dr. Jin-Doo Kim awarded with a Medal for Extraordinary Achievement for decades-long work for promoting board and paper technologies
- May 26, 2025Valmet to supply a fifth Advantage tissue production line to Lila Group in Turkey
- May 21, 2025Valmet to supply a major paper machine rebuild to Sylvamo in North America
- Mar 27, 2025Successful start-up of Zhejiang Forest United Paper’s PM 6 production line
- Mar 27, 2025Valmet to supply two winders to Wuzhou Special Paper in China
- Mar 6, 2025Valmet to supply a high-capacity winder to Jingxing Holdings in Malaysia
- Jan 21, 2025Valmet to supply an off-machine coater to a customer in Asia-Pacific
- Nov 12, 2024Valmet to supply a complete papermaking line to one of its major customers in Asia-Pacific
- Oct 21, 2024Valmet’s change negotiations completed in Finland in its Paper business line’s Board and Paper Mills business unit
- Oct 3, 2024Valmet to supply an OptiConcept M board making line to Anhui Linping Circular Development in China