Optimizing the continuous cooking digesters at Stora Enso Imatra Mills
Stora Enso Imatra Mills annually produces approximately one million tons of board and paper. The main production is of liquid packaging for beverage cartons, and food services boards for paper cups and other food packages.
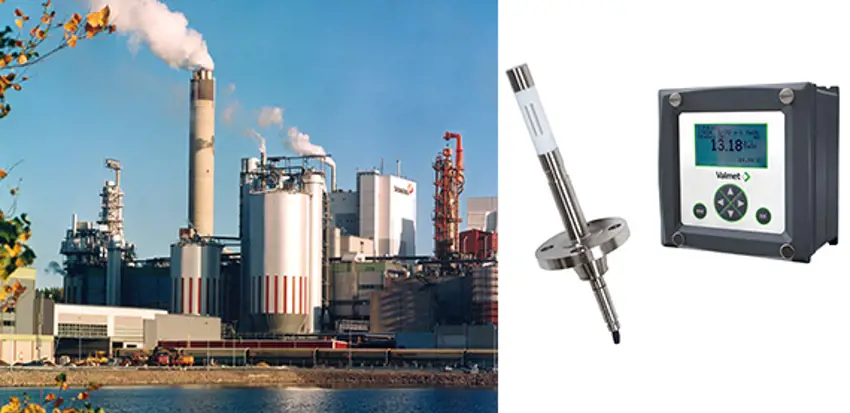
Summary
Location | Imatra, Finland |
Customer challenge |
Stora Enso decided to build a new short-fiber pulp line (line 3) for birch cooking, and later to modernize and convert the existing pulp line 2 to long-fiber. Thus, there was the need to optimize the cooking process. |
Solution | Valmet Cooking Liquor Measurements (Valmet Cooking 3400) for white liquor, transfer circulation, ITC, expansion ja extraction. |
Results |
Production targets were exceed quickly after the start-up. The pulp from line 3 is very pure, which is essential for boards for the food industry, and the pulp from line 2 has improved its strength. Less pulp has to be purchased, thus reducing costs and enhancing pulp quality. The carbon dioxide emission from fossil fuels has been reduced, because the increased pulp production has lead to an increase in production of by-products, like black liquor and bark, which are used as fuel instead. |
Keywords | Pulping and fiber, Automation, Improvements, Europe |