100th order proves flexibility of CFB boilers
The more challenging the fuel, the more flexibility Valmet’s circulating fluidized bed (CFB) boiler shows. It has evolved from a coal-only boiler to combusting biomass and anything in between.
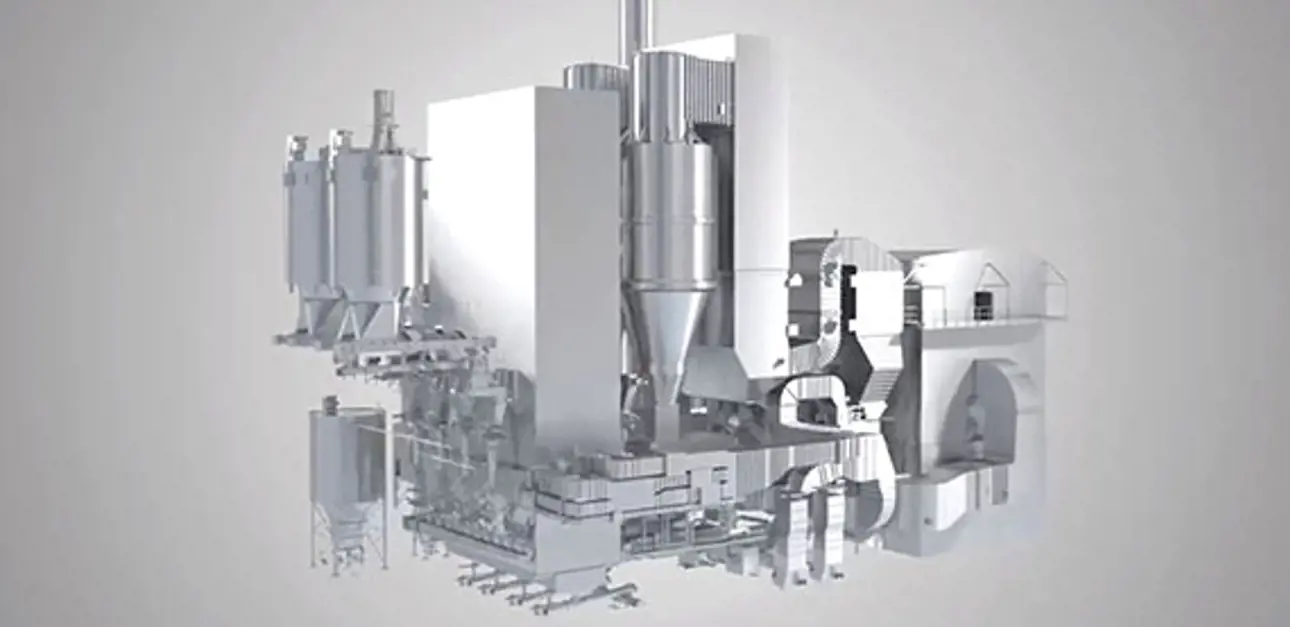
Over the past decades, fuels used in energy production have thoroughly changed and presented the design driver for Valmet’s CFB boiler development. Back in the 1980s, energy producers wanted to use low-grade waste coal because it was cheap. Valmet was able to deliver CFB boilers to solve the problem. Next, it was biomass that changed the boiler design dramatically in Scandinavia. In the late 1990s, as energy producers were faced with shortage of reasonably priced biomass, Valmet modified its CFB boiler for a wider design fuel portfolio and introduced its multifuel approach.
In the early 2000s, there was a brief boom of pet coke and high-ash coal projects, especially in the US. They were followed by new challenging fuels, such as waste fractions and agro-biomass fuels either fired alone or with other fuels.
“Coal will not disappear from the CFB fuel portfolio but due to political decisions its importance as the main fuel for boilers is decreasing. Also, more and more demanding biomass fuel qualities must be accepted, and the utilization of waste will continue to increase as big cities have to consider waste as a source of energy instead of incinerating it,” says Tero Luomaharju, Product Manager, CFB boilers at Valmet. “The evolution of our CFB technology is a result of systematic development work as well as lessons learned in projects in a world where everyone is trying to find the most competitive fuel combination.”
Components that make a difference
During the nearly 40 years that Valmet and its predecessors have been developing and delivering CFB boilers, there has been a huge evolution in technology to meet ever-increasing customer and emission requirements. The company has introduced pioneering conceptual boiler designs and mechanical structures to enable the combustion of high volatile content fuels with very demanding fuel chemistry.
One of the component design highlights is the first water-cooled cyclone built in 1985, and since 1995 a membrane cyclone has been included in Valmet’s every CFB delivery. Its introduction was a huge step forward with regard to maintenance needs and boiler reliability. Scaling up the membrane cyclone has been successful; today even a 100 MWe CFB can be constructed with only one cyclone.
Another major development in CFB design took place when demanding biomass fuels with high chlorine and alkali metal levels entered the fuel portfolio. Corrosion minimization had to be improved due to these fuels. Valmet developed special loop seal and final superheater solutions to tackle the issue.
Valmet CFB boiler development.
Focus on fuel flexibility
The CFB success story and component development owe much to Valmet’s energy R&D center in Tampere, Finland. “Over the years the center has accumulated significant amount of fuel data and tested dozens of new technological features. By testing 9,000 tons of various fuels on an industrial pilot scale, we have test data for over 50 fuels and over 100 fuel mixtures for operation on fluidized bed boilers,” says Marko Palonen, Manager, R&D Portfolio.
Today, it is normal to have four to five design fuels in a boiler to decrease the price and availability risk of fuels. “The biggest benefit of CFB technology is fuel flexibility. Regardless of what the future fuel portfolio will be, CFB will ensure the plant’s future. Thanks to fuel flexibility, the customer will always be able to use the most economical fuel combination,” emphasizes Ari Kokko, Director, Technology and R&D, at Valmet Energy Business Unit. Indeed, it seems all future fuels will be waste-streams or by-products from various processes or industries rather than virgin fuels. This means a very resource-efficient approach to energy production will be needed,” he continues.
TEXT Marjaana Lehtinen
Article published in Forward magazine 2/2019.
Related articles