Raw material savings with refining rebuild
Raw material is the single biggest cost in papermaking. JSC Arkhangelsk PPM increased the competitiveness of finished products by rebuilding refining system. They were able to improve end product quality, reduce the costs of furnish components and save energy up to 20%.
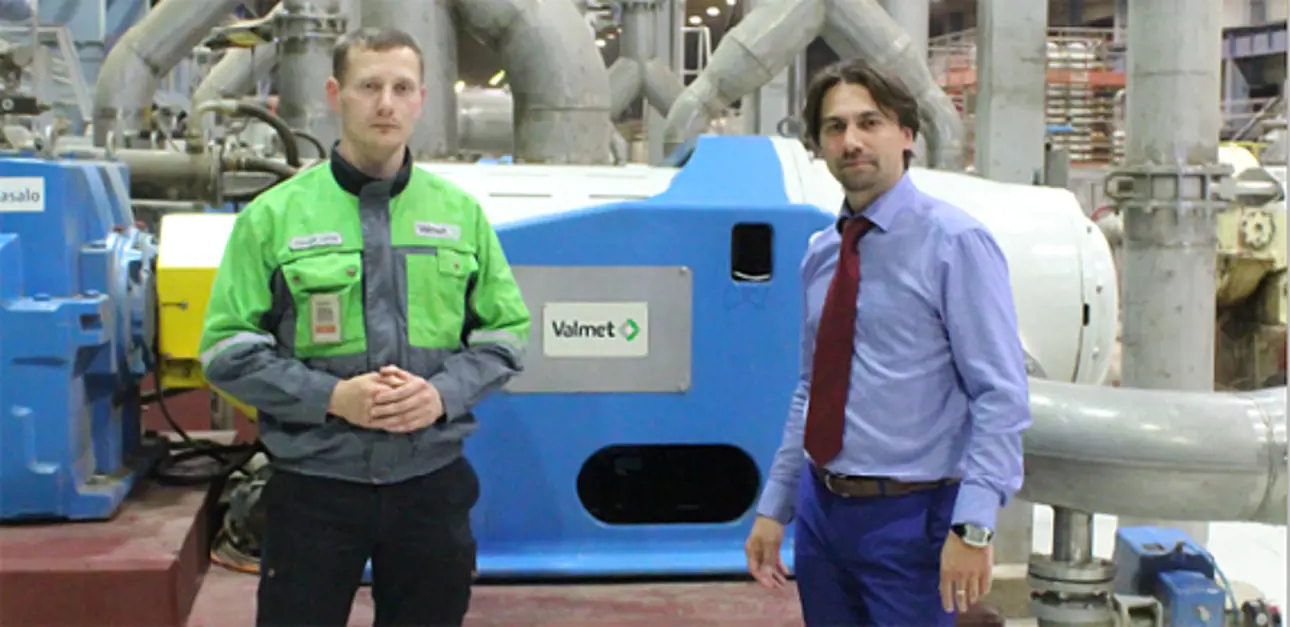
JSC Arkhangelsk PPM, the biggest containerboard manufacturer in Russia, has recently invested significantly as they strive to increase the mill’s capacity, product quality, cost efficiency and sustainability. Valmet’s OptiFiner Pro refiners helped the Novodvinsk mill to meet its targets with an upgraded stock preparation system.
“We wanted to increase the competiveness of finished products produced by our BM 1 and BM 2 machines”, explains Alexander Tufanov, Technical Director of board production development, about the factors behind the investment. “Our old refining system with several disc refiners had limited capacity and provided poor quality, and it was well worth looking for more modern solutions,” he continues. “Valmet’s solution was inviting because of Valmet’s proven track record in energy efficiency. We also felt that new refiners would give us better control over the refining process and improve the quality of the final product. The innovative refining principle was a factor as well,” Tufanov explains.
|
“The new refiners give us better control over the refining process and improve the quality of the end product.” |
|
|
Alexander Tufanov, Technical Director of board production development |
Raw material savings
The achieved refining results of the physical and mechanical properties of the finished product are promising. The main strength parameters, such as burst strength and compression strength, are showing increases. “This has provided us an opportunity to carry out tests with a higher proportion of semi-cellulose in the kraftliner and fluting furnish and reach good quality values for end product with lower cost furnish”, Tufanov explains. Tufanov also mentions that the opportunity to change the refining degree range without damaging the fiber has considerably increased since the installation of the new refiners.
BM 1 produces kraftliner and BM2 fluting and uniliner. Due to refining rebuild, main containeboard strength parameters such as burst strength and compression strength, are showing increases.
Increased production flexibility
During the upgrade of the stock preparation system, BM 1 – which produces kraftliner at a maximum speed of 730 m/min – got four OptiFiner Pro refiners for refining unbleached softwood kraft pulp. BM 2 produces fluting and uniliner at a maximum speed of 550 m/min, and it got four OptiFiner Pro refiners for refining both softwood and also a mixture of soft- and hardwood as well as new slot screening equipment for base ply stock. “Basically, the stock preparation process for BM 1 and BM 2 has not changed. The control of the rebuild refining process is now more flexible with quicker response, though. Visualizing the process allows equipment operation and the process to be more easily monitored. The time it takes to change the grades (between kraftliner and fluting) has been considerably reduced, which is extremely important for BM 2,” says Tufanov. The capacity of the refining system has also increased significantly.
Up to 20% energy savings
Dmitriy Hrapach, Board Production Director, explains the importance of further cost savings in the form of less refining energy, as their aim is sustainable and efficient production. “The new equipment met all our expectations. We achieved the target values for both energy efficiency and the quality of furnish components. The reduced power consumption in refining is considerable. For BM 1, we have witnessed energy savings of more than 5%, and BM 2 has been even better, with savings of about 20%,” he says.
“The stock preparation system rebuild for BM 1 and BM 2 is part of our board production development project,” Hrapach explains. “The results we’ve achieved are clearly visible in our current operations, as we have managed to improve our end product quality, reduce the costs of furnish components and save energy. The rebuild and the increased refining capacity are also a good starting point for further rebuilds of BM 1 and BM 2 as we continue to increase our production capabilities,” he says.
|
“OptiFiner Pro is up to date, compact and energy saving.” |
![]() |
|
Dmitriy Hrapach, Board Production Director |
|||