Valmet Energy R&D Center - Leading the way in energy innovations
Valmet Energy R&D Center - one of its kind worldwide - enables energy producers to take circularity and resource efficiency to the next level and widen their fuel portfolio toward cheaper and more sustainable fuels.
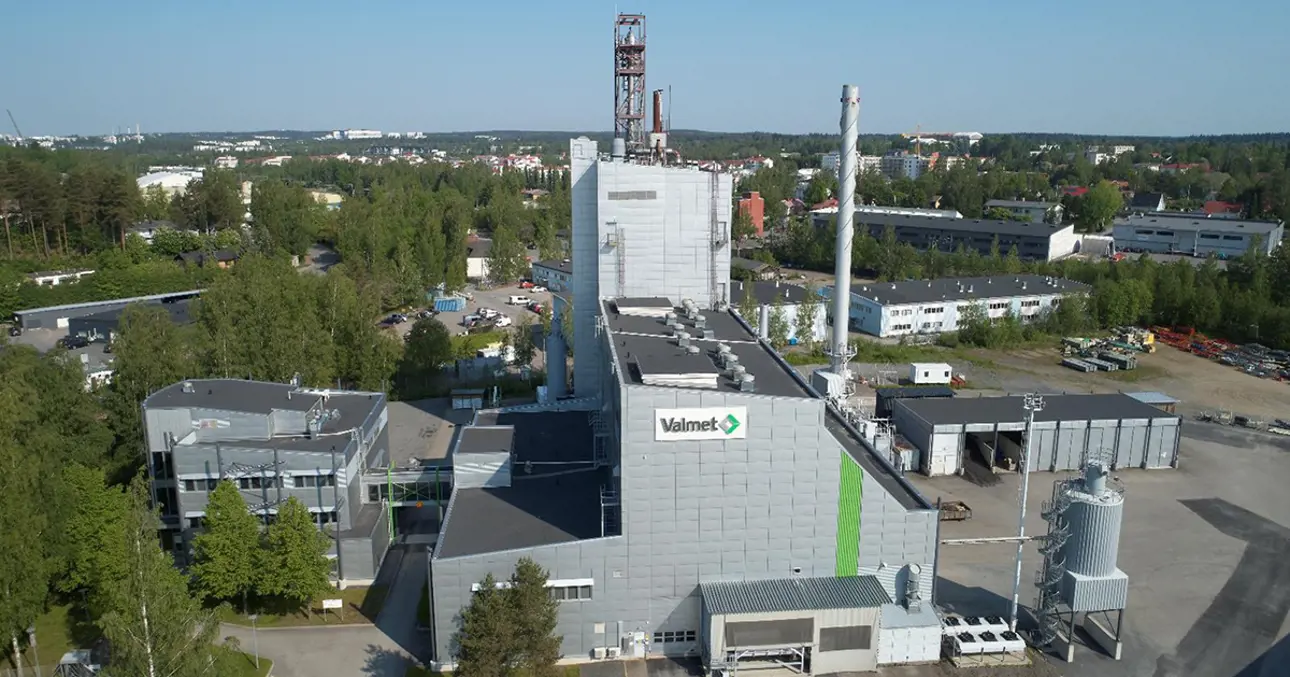
In Tampere, Finland, Valmet Energy R&D Center is renowned among energy producers worldwide for its process innovation and fuel testing capabilities. Since 1990, the center has tested 9,500 tons of various fuels in fluidized bed boilers, accumulated a vast volume of fuel data, and helped customers minimize their investment costs and risks, guarantee high-performance levels, and secure long-term investments.
The center carries out experimental testing to bridge the gap between the lab-scale tests and commercial demonstration plants. By combining high-end technology infrastructure and top talent, its target is to improve performance and efficiency, reduce environmental impact, boost circularity, and extend the fuel portfolio. Cooperation with universities and research institutes is close.
At Valmet Energy R&D Center, technologies are scaled up from ideas to proven industrial solutions. The stages consist of research (Technology Readiness Level 1-3), development (TRL 4-6), deployment (TRL 7-9), and step-by-step evaluation to find the optimal fuel blend for each customer. Proceeding step by step helps minimize investment risks and technological surprises later on, ensuring confidence that this new solution works on a large scale. Additionally, it allows for identifying limits and proper operation of the plant.
“The center plays an important role in enabling energy producers to use renewable residual fuels and to meet today’s challenges in dealing with resource scarcity and low-quality fuels,” says Marko Palonen, R&D Manager in Valmet’s Energy business. “We also support our customers in moving toward higher-value end products. Instead of producing heat, steam, and electricity from available resources, we develop also new solutions for producing fuels, chemicals, and materials from them.”
Valmet’s Beyond Circularity program aims at transforming waste and emissions into valuable resources for sustainable growth and accelerating the green transition. The program targets are closely connected to Valmet’s Technology vision 2030 and a climate program called Forward to a carbon-neutral future.
Catalytic pyrolysis to boost resource efficiency
One of the center's circularity-related R&D projects focuses on biorefining and a new biomass pyrolysis solution to turn local sustainable feedstocks into global renewable transportation fuels and biochemicals. Valmet’s catalytic pyrolysis—Valmet Pyrolyzer—is a robust technology that catalyzes the pyrolysis vapors directly without hydrogen.
“After having successfully commercialized fast pyrolysis, we now work on bringing catalytic pyrolysis for transportation fuels to the market,” says Jouko Latva-Somppi, Manager, Pyrolysis, at Valmet. “Pyrolysis with catalytic upgrading can produce biocrude for conventional refineries from biomass, such as forest residues. As the European Union will be requiring a higher share of biofuels in traffic fuels, the only way to do it is to add side streams from the forest industry to them.”
The center houses the world’s biggest catalytic pyrolysis pilot plant. Commissioned successfully in 2023, it is now piloting on a small industrial scale (400 kg DS/h). The target is to reach readiness for 5-20 tDS/h in 2025 and 50-100 tDS/h by 2027.
Recycling mixed plastic waste (polyolefins) and polystyrene offers another interesting field of research and development. Valmet is currently carrying out a pilot project with a partner.
Testing and finding the optimal fuel mixtures
As energy producers look for opportunities to boost sustainability and decarbonize their production, they often face uncertainty with the use of new, unknown, and sometimes quite challenging fuels, such as agro residues. Can they even be used for energy production in fluidized bed boilers and what are their combustion characteristics? To what extent do they cause corrosion or fouling? Are emission limits reachable at reasonable costs? What is the ash like?
“In our facilities, energy producers can test these features, get the much-needed answers and fuel data as well as secure their potential investment in advance. Testing decreases their technical and economic risks,” points out Mikko Varonen, Team Leader at Valmet Energy R&D Center. “Expanding the current fuel mix generally does not require piloting, as the limits can be determined with a Valmet Boiler Combustibility Study. This way, the Service helps customers expand their mix. However, if something new and exotic is added to the fuel mix, then piloting may be necessary.”
In the past years, Valmet has tested new fuels, such as various renewable agrofuels (e.g. straw and empty fruit bunches (EFB) from the palm industry), coal washery reject and asphaltene, a side stream of the oil refining process. Although classified as a fossil fuel, the combustion of asphaltene supports circularity by turning an otherwise useless waste into energy.
One-of-a-kind facilities and equipment
To carry out all these pilot trials, Valmet offers a complete fluidized bed boiler pilot facility, including comprehensive analysis services and access to its network of experts. The facility also serves extensive in-house R&D work. The facilities include fluidized bed boilers, tube reactors, cold models, equipment for full-scale field testing, and measurements as well as a flue gas scrubber. The plant is equipped with Valmet’s energy automation systems and its latest DSC version Valmet DNAe.
![]() |
For full-scale tests, Valmet has developed unique measurement devices that can be utilized for example in fouling and corrosion studies. Measurements together with the analysis of the results offer a solid foundation for decision-making concerning, for example, fuel changes. Valmet also has mobile additive injection units that can be moved to the customer plant to test the impact of different chemicals and define the needed amount for emission reduction. |
Oxycombustion now with biomass
Oxyfuel combustion presents yet another interesting field of research. As the technology was developed and proven by Valmet back in 2011, it does not need piloting as such. However, it was at the time carried out with fossil coal that behaves differently than biomass.
“Valmet is the leading expert in the thermochemical treatment of biomass and is well aware of the associated challenges and pitfalls. With our infrastructure and expertise, the likelihood of successful piloting is very high,” Varonen adds.
R&D for carbon capture, too
In addition to biofuel and combustion testing, the Energy R&D Center focuses on advanced air emission control technologies. Over the years, extensive work has been dedicated to developing the key components of the Valmet Bag House Filter (BHF) and Valmet Electrostatic Precipitator (ESP).
One of the latest additions to Valmet’s pilot facility is a flue gas scrubber, designed for testing and developing high-efficiency environmental systems for flue gas cleaning in both the marine and energy industries.
The facility also features a Direct Contact Cooler (DCC), enabling comprehensive testing of NOx reduction solutions and overall emission control strategies. Additionally, the center supports the development of Wet Electrostatic Precipitator (Wet ESP) technology, which plays a vital role in capturing fine particulates and reducing harmful emissions.
In reaching net-zero emissions, Bioenergy Carbon Capture Utilization and Storage (BECCUS) plays a crucial role.
Advanced flue gas pre-treatment is key to the successful implementation of carbon capture plants. More optimized flue gas cleaning solutions are needed not only to ensure compliance with stringent emission standards but also to improve the efficiency of the decarbonization process.
BECCUS could potentially generate revenue through carbon dioxide removal as well as generate a source of biobased green CO2 for Power-to-X (PtX) processes.
Read more about our Energy R&D
For more information, please contact:
- Mikko Varonen, Team Leader, Valmet Energy R&D Center
- Marko Palonen, R&D Manager
- Jouko Latva-Somppi, Manager, Pyrolysis
- Lari-Matti Kuvaja, Director, Environmental Systems, Carbon capture
Valmet’s R&D Center for Energy
- Focusing on fluidized bed boilers, pyrolysis, and environmental systems
- Facilities include fluidized bed boilers, pyrolysis pilot, tube reactors, cold models,
equipment for full-scale field testing and measurements - Equipment: 4 MWth CFB, 2 MWth BFB, pyrolysis reactor, 10–100 kW tube reactors, cold models
- Valmet DNAe, the latest version of the Valmet DCS system, has been piloted here
The typical targets of the testing include:
- Improving product performance and efficiency
- Reducing environmental impact
- Extending the fuel portfolio
Test facilities include:
- Fuel testing equipment, focusing on fluidized bed boilers
- Pilot scale pyrolysis equipment for biocrude production
- Equipment for flue gas cleaning development
- Equipment for full-scale field testing and measurements
- Test units on demand
- Automation R&D participation
Related articles