Customer case:
Metsä Fibre's Kemi bioproduct mill
Metsä Fibre, which is part of Metsä Group, is building a new bioproduct mill in Kemi, Finland. The new bioproduct mill will have an annual pulp production capacity of 1.5 million tonnes and in addition produce various other bioproducts. The new totally fossil fuel free mill is scheduled to start-up in the third quarter 2023.
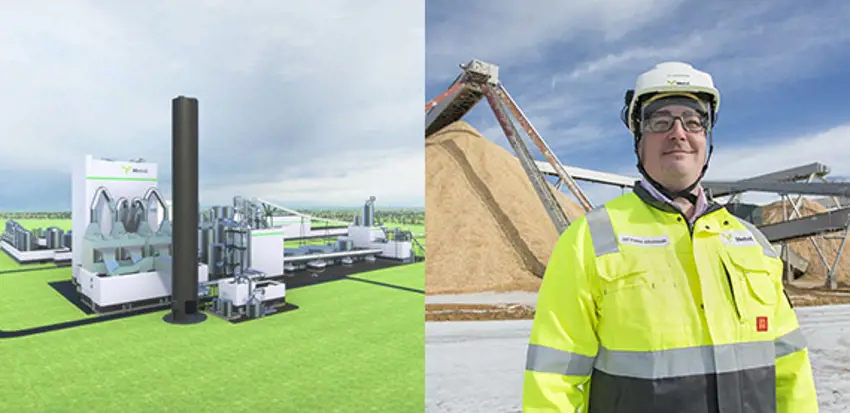
We want the best professionals in their field to partner with us to build a modern bioproduct mill in Kemi. We expect our partners to commit to the goals of the project in terms of safety, schedule and quality.”
Summary
Location | Kemi, Finland |
Customer challenge | Growing demand for softwood pulp Replacing an old pulp mill |
Solution |
New pulp mill with all main process technology and automation from Valmet: Woodhandling
Cooking and fiberline
Pulp drying and baling line
Evaporation
Recovery boiler
Ash treatment
Recausticizing
Fossil fuel free lime kiln
Sulfuric acid plant
Mill wide NCG solution
Mill wide automation system
|
Results |
The mill is optimized for:
|
Keywords | Chemical pulping, Complete pulp mills, Automation, Europe, Finland |