What is AI in valve diagnostics and digital services?
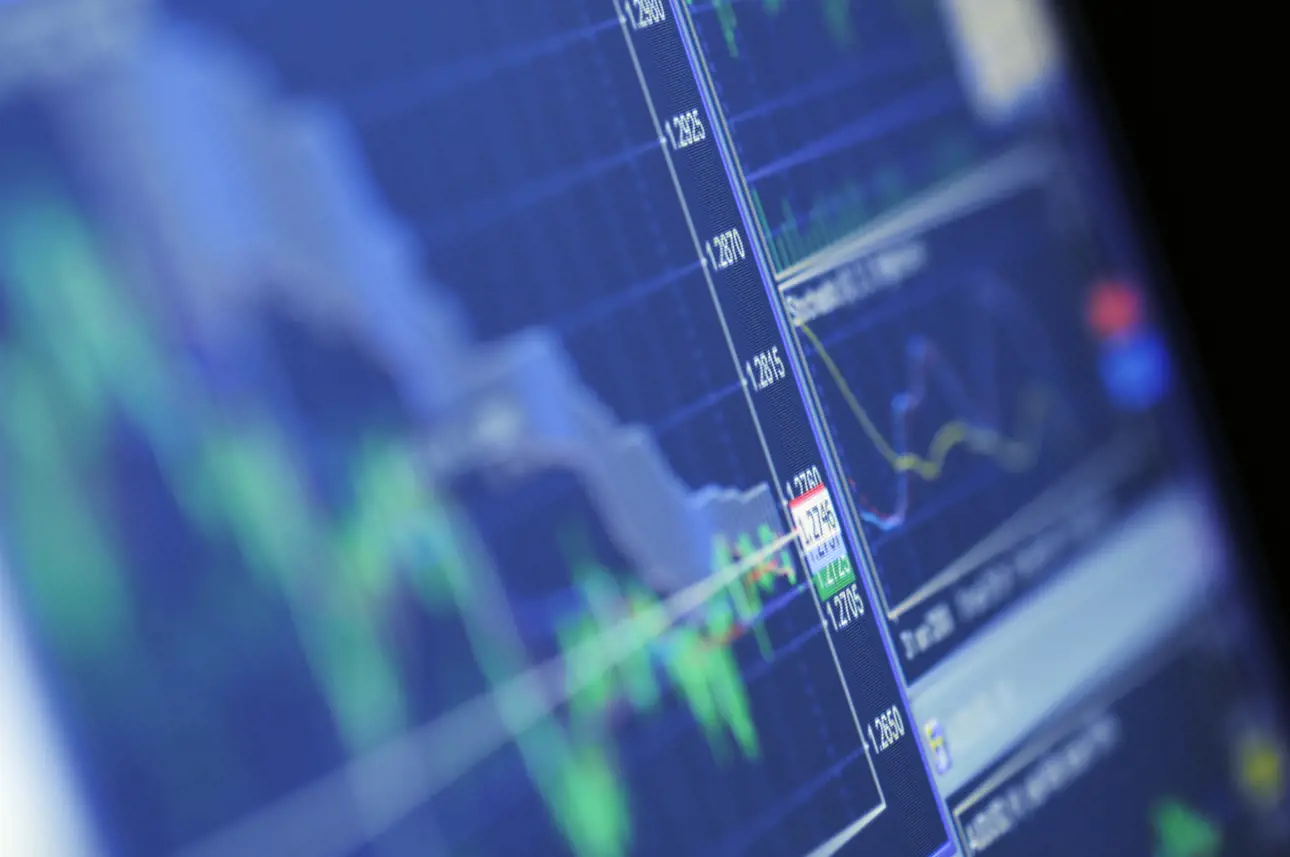
Artificial Intelligence is rapidly entering the world of valves. AI is not intelligent as such. It learns from what has happened before. It develops itself when presented with relevant information.
A lot of data is already available for both valve end users and valve manufacturers. Both parties can do their own AI separately: end users with process information; manufacturers with their experience of the valve service and global customer base. However, the best data for AI is achieved by combining these two sources. Valmet AI aims to achieve the best dataset for it to learn from.
Twice as smart: Combining digital and human intelligence
Our unique approach combines the deep expertise and insight of our dedicated service personnel with the latest advances in digital tools and technologies, including AI. This synergy allows us to provide instantaneous global access to our expert services, ensuring better, faster, and more reliable solutions. Our digital services portfolio is built on the foundation of smart data and human intelligence, offering comprehensive support, from valve selection and installation to operational reliability and maintenance. As your single responsible partner, Valmet is committed to delivering availability, reliability, and performance across your valve installed base, regardless of brand or manufacturer. With Valmet, you can be confident that you have a partner who can provide it all, combining the best of human and digital intelligence to meet your needs.
Utilizing AI for predictive services for valves
Valve automatic diagnostics
Valve diagnostics is daily work for many process plant automation and maintenance teams. Critical valves are checked often to make sure they are working properly. The problem with this approach is that there may be thousands of process valves to monitor, and there are neither the time nor resources to handle them all effectively.
Valmet Industrial Internet (VII) and ValvesNow approach provide on-time, continuous, automatic monitoring of your equipment. They employ expertly crafted decision trees and analytics, using diagnostics data from positioners such as Neles™ ND9000 and PlantTriage process analytics. This diagnostics analysis not only flags and alerts you about the problems, it also puts them in order of priority. The platform helps our customers identify the worst-performing valves in their valve fleet, enabling the efficient use of maintenance resources by pinpointing areas that require immediate attention or with the most potential for beneficial changes.
Service demand forecast
What is the maintenance interval for a valve? When you become familiar with valves, you understand that this is not a straightforward question. Even when two valves are exactly the same, they can be in very different environments. One might be serving motor oil at an ambient temperature, and another very abrasive gravel. The maintenance intervals for these valves are not the same.
With our service demand forecasting we utilize AI technologies to estimate the lifecycle of valves and recommend when to service devices. Service demand forecast utilizes machine learning, data science, and AI-powered models. These models leverage extensive service data and the vast installed base among other information. This helps estimate the lifecycle of valves and in recommending the next service time, enhancing reliability by providing insights into when valves should be maintained.
Inventory management
With preventive and predictive maintenance, unexpected valve events are minimized, but every now and then something happens, regardless of proper planning and monitoring. To minimize the downtime during these events, a suitable spare inventory is needed.
Our inventory recommendation is designed to provide spare part and device inventory recommendations for end-user plants, helping customers define optimal spare stocks. Inventory recommendations are based on a novel AI algorithm that uses service demand forecasting, installed base, parts availability data, and geographical locations, as well as the customer’s own maintenance strategy.
AI offers numerous benefits to both Valmet and our customers. By leveraging AI, we enhance reliability, predictivity, and efficiency, ultimately providing superior value-added solutions. At Valmet, we adhere to five responsible AI principles to ensure fairness, privacy, and security: traceability, transparency, oversight, governance, and security.
Read more
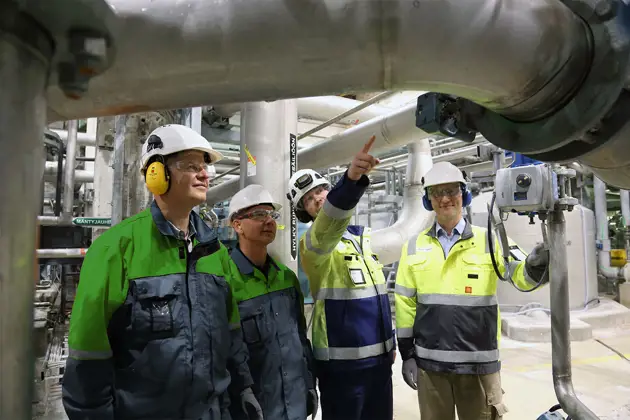
Subscribe to our newsletter
Subscribe now to flow control newsletter and receive the latest insights directly to your email.
Subscribe