Carbon capture starts with clean gas: why pre-treatment is the hidden key to reliable CCS
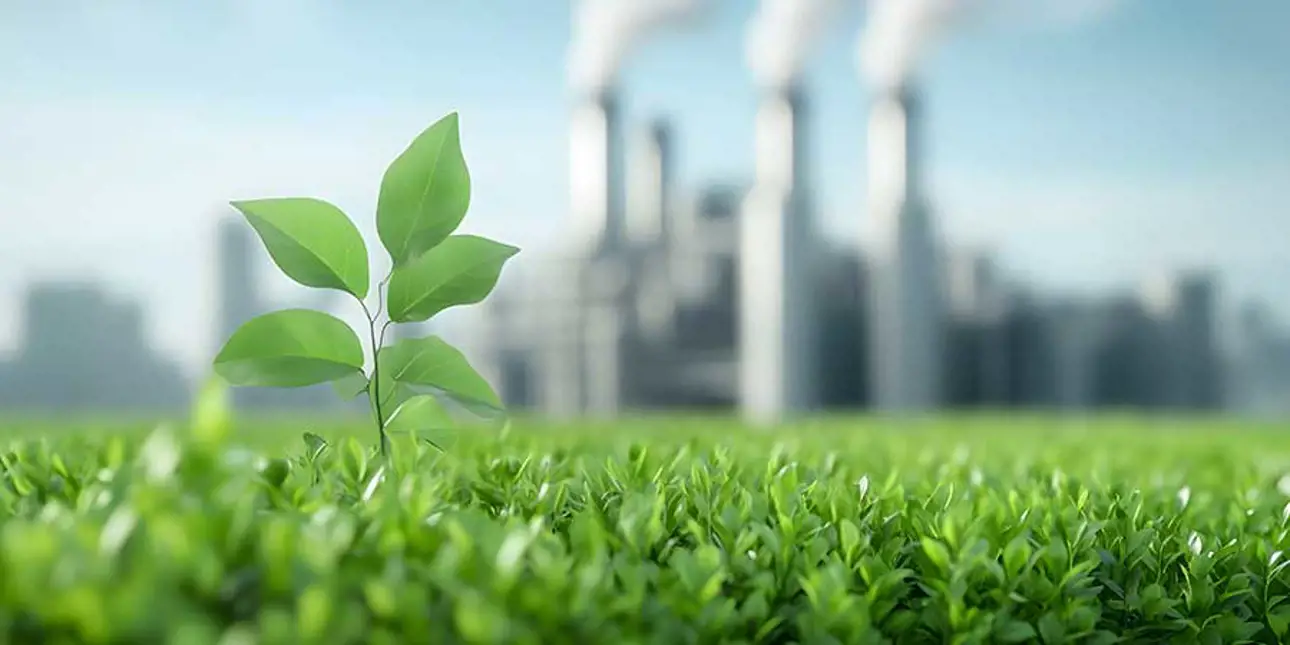
As CO₂ capture scales up, success increasingly depends on what happens before
Clean gas: the unsung foundation of carbon capture
As Carbon Capture and Storage (CCS) moves from pilot to full-scale deployment, focus often falls on capture chemistry, compression, transport, and storage. But one crucial piece is often overlooked: flue gas quality.
Capture systems—especially those using amine-based solvents—are chemically sensitive. Contaminants like SO₂, SO₃, NOx, particulate matter, and heavy metals don't just complicate the process—they compromise it. Even legally compliant flue gas may fall short of capture process needs.
From our experience in multiple industries, it's clear: successful CCS starts not with the absorber, but with reliable, tailored flue gas pre-treatment.
Legal compliance isn't enough
Consider a typical waste-to-energy or cement plant. It might legally emit 30 mg/Nm³ of SO₂ and 200 mg/Nm³ of NOx. These levels comply with EU BAT standards. But for a capture plant using MEA, even trace amounts of SO₂ can form heat-stable salts, degrading the solvent and driving up operating costs.
CCS systems require much cleaner gas than regulations mandate—lower SOx, NOx, particulates, and heat. These internal specs are far stricter than emission limits defined by frameworks such as the EU Industrial Emissions Directive (IED), the Large Combustion Plants (LCP) BAT conclusions, or national permits. While these set the regulatory baseline, carbon capture requires significantly cleaner gas to ensure long-term stability and performance. U.S. environmental standards, such as those set by the Environmental Protection Agency (EPA), play a similar role in North America, providing a legal framework that CCS systems must exceed to function reliably.
Without this, operators face solvent degradation, fouling, downtime, and higher costs.
What pre-treatment involves
Tailored flue gas conditioning isn’t just about adding an additional equipment. It depends on the fuel, site layout, existing equipment, and what the capture technology demands.
Most systems include a Direct Contact Cooler (DCC) to cool and clean the gas. DCC isn’t new, it’s long been known as a flue gas scrubber or condenser, used since the 1970s in Scandinavia to recover heat for district heating. The DCC can be integrated with other emission control technologies to go beyond cooling—enabling further purification of the flue gas in a compact, efficient step.
A critical technical driver is the presence of pollutants like SOx and NOx, which form heat stable salts (HSS) with amine solvents. These salts are not removed during normal solvent regeneration and require expensive reclaiming. If left untreated, they accelerate solvent degradation, increase corrosion, and drive-up operating costs.
Beyond DCC, it’s case-by-case, depending on the existing plant process and emissions, but always, the pre-treatment design impacts plant layout, heat flows, and cost. Whether or not, it's taken into consideration or not in carbon capture PRE-FEED and FEED studies. As always changes done later come with higher costs.
A crucial part of planning is to treat the existing plant and the new carbon capture unit as an integrated system—not as separate processes. In many cases, existing emission control equipment can be optimized or upgraded, avoiding the need for additional systems and unnecessary complexity.
The goal: meet capture specs with minimal added equipment or energy. Many carbon capture vendors supply precise flue gas specs—pre-treatment is the bridge that makes real-world emissions fit those requirements.
Why it unlocks
Pre-treatment done right offers real, concrete value:
- Solvent protection, lower solvent use (often 15-30% total OPEX)
- Capture stability, making financing and warranties viable
- Heat recovery, which can cover 10–20% of the process’s own energy demand
- Revenue, when low-grade heat is sold to district heating (often €90–140/MWh)
- Funding alignment, especially where sustainability co-benefits are required
Chemical costs are a significant contributor to operating expenses in solvent-based CCS systems. Solvent losses may represent 10% of capture costs. It preserves solvent integrity, reduces make-up, and cuts waste handling.
As highlighted by the U.S. Department of Energy’s National Energy Technology Laboratory, integrating heat recovery into CO₂ capture systems can reduce overall energy penalties by as much as 26%. Similarly, reports from the U.S. Energy Association emphasize that thermal integration is essential to the viability of large-scale CCS projects and should be treated as a core design element, not an afterthought.
Demonstrating value
In early projects and industrial trials, tailored pre-treatment has helped reduce solvent-related operating costs by 20–30%, by reducing degradation and solvent reclamation. In parallel, optimized heat recovery through pre-treatment systems—such as integrating Direct Contact Coolers with district heating—can meet more than 10–20% of the carbon capture process’s total heat demand, depending on the process and scale.
These aren't theoretical—they're real gains from treating pre-treatment as core CCS design.
Making the heat work for you
Pre-treatment protects the process and enables heat recovery.
Many plants have untapped heat in their flue gas. Pre-treatment systems that include a Direct Contact Cooler (DCC) can reclaim low-grade thermal energy that would otherwise be lost. This energy can often be redirected to:
- District heating networks, supplying useful heat to nearby communities
- Internal process loops, such as boiler feedwater pre-heating
- Heat pump integration, boosting efficiency and enabling even broader thermal reuse
The financial value of such recovery can be substantial. In district heating markets, recovered heat may be sold—often at rates between €90 and €140 per MWh, according to publicly reported district heating tariffs in countries like Denmark (€93/MWh), Germany (€104/MWh), and the Netherlands (€144/MWh)—creating a direct revenue stream. When integrated effectively, this can add hundreds of thousands of euros per year to the value proposition of a carbon capture project.
This heat can also offset part of the capture process’s energy demand—particularly for solvent regeneration, which is one of the main energy consumers in post-combustion capture. Studies have shown that well-integrated systems can reduce the overall energy penalty of carbon capture by up to 26%, making the economics more attractive and reducing net CO₂ emissions.
This integration is no longer optional—it’s expected. In regions with strong sustainability targets or energy price pressures, the ability to couple CCS with efficient heat recovery can make or break project viability.
Pre-treatment is more than a gatekeeper—it’s a thermal integration point in the broader energy system.
¹ Sources: Euroheat & Power, "District Heating and Cooling Market Outlook 2024"; Energinet (Denmark), Bundesnetzagentur (Germany), and ACM (Netherlands), 2023–2024 data.
Lessons from the field
Flue gas pre-treatment is no longer an optional accessory; it’s a core design function. It affects not just chemistry, but layout, thermal balance and overall efficiency.
- Early pre-treatment planning avoids redesign and delays
- Investing in flue gas characterization upfront avoids overspec or underdesign
- Optimizing existing emissions controls can reduce the need for new equipment
- Integration challenges are often solved by considering the full system—gas, water, heat, and control
- When planned early, pre-treatment helps unlock performance, funding, and long-term reliability
Supporting regulatory compliance and meeting funding criteria are increasingly linked to environmental co-benefits. Done right, it delivers both. Carbon capture doesn’t start at the absorber. It starts with clean, conditioned, stable gas.
As projects scale, pre-treatment is no longer optional—it’s foundational. For technology providers, operators, and EPCs, earlier pre-treatment planning means greater value—in performance, cost, and funding.
By Lari-Matti Kuvaja, Director of Environmental Systems, Valmet
Related articles