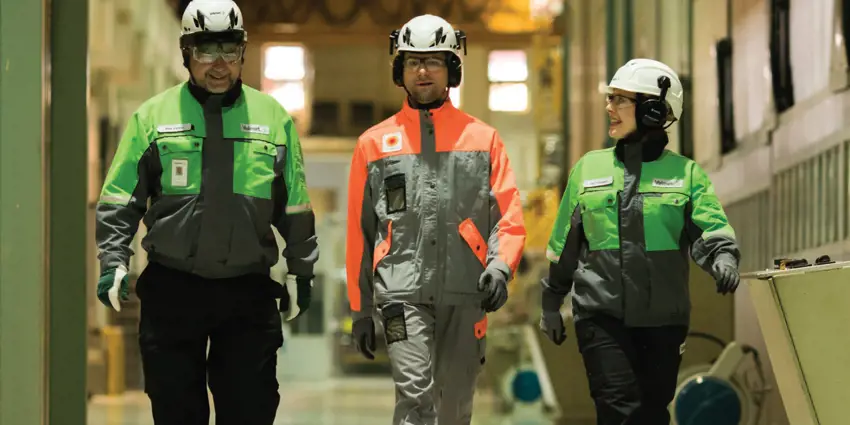
Feb 21, 2020
The mill worked with Valmet to develop a customized approach to annual outages at their site that combined OEM vacuum washer expertise, spare parts inventory planning, shutdown planning, project planning & execution, on-site field service and outage support.
We continue the relationship each and every shutdown. Year after year we are working together to evaluate what is needed for the year to come.” - Al Parsons, Mill Sales Manager, Valmet
Location |
Western Canada Pulp Mill |
Customer challenge
|
|
Solution
|
|
Results
|
|
Keywords | Canada, outage, planning, pulp washing, fiberline |